往復走絲電火花線切割加工技術發展瓶頸及研究思路
2016-12-21 來源:南京航空航天大學機電學院 作者:劉志東
摘要:分析了當前往復走絲電火花線切割機床在高效切割、解決絲耗、導絲定位等方面遇到的技術瓶頸,提出了相應的解決思路。對于高效切割,關鍵問題是要解決大電流加工條件下工作液在極間迅速汽化的問題;對于絲耗問題,提出了一種往復走絲漸進送絲的新走絲方式;對于電極絲導絲問題,認為采用非強制間隙約束方式是導絲器的發展方式。
關鍵詞:往復走絲;電火花線切割加工;發展瓶頸;研究思路
具有中國自主知識產權的往復走絲電火花線切割機床自20 世紀70 年代步入市場后,以其很高的性價比為模具加工市場所接受,目前已成為機械加工領域不可替代的加工手段,且其應用領域在不斷拓展,技術水平也在不斷提升,并正在逐步為世界各國所接受[1,2]。近十幾年來,伴隨著具有多次切割功能的往復走絲電火花線切割機床(俗稱“中走絲線切割機床”)的發展,往復走絲線切割加工技術獲得了長足的進步, 但由于其自身的加工特點,目前遇到了如高效切割、電極絲損耗處理及導絲持久性等一系列技術瓶頸。本文的目的在于針對這些問題,從放電加工機理方面加以分析,為業內的研究人員提供一個解決問題的參考思路。
1.往復走絲的“非對稱性”加工特點
往復走絲電火花線切割加工雖然冠以往復的名稱,但在往復走絲的加工過程中,由于受到重力的作用,從微觀角度而言,其加工過程中的冷卻、排屑及消電離均是非對稱過程, 因此其加工始終是“非對稱”的,也即走絲形式上的對稱由于遭遇到重力的影響而被改變,從而顯示出了正反向走絲時各自差異的特性。這種“非對稱”的特征在高效、小參數精加工及高厚度切割時體現的尤為明顯,主要體現在切割表面在工件的上下端面表面質量包括燒傷情況(圖1)不同甚至會影響到切割的精度;在正反走絲時也會因為切割穩定性不同導致進給速度的不同;切割過程中電極絲張力會逐漸出現單邊松絲[3]等問題。因此在細化研究往復走絲切割時,應該針對其“非對稱”加工的觀點,通過改變正反向走絲時的高頻電源參數、伺服跟蹤速度、走絲速度等來達到提高正反走絲加工工藝指標均勻性和一致性的目的,如果再考慮到切割方向不同導致的因導輪對電極絲定位的影響,這個問題將更加復雜。
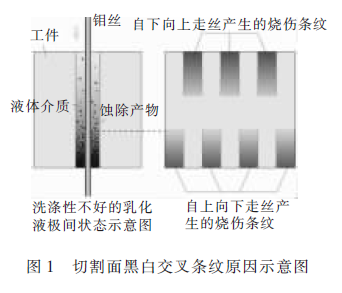
2.往復走絲的技術瓶頸問題
2.1 高效穩定切割
往復走絲電火花線切割加工的工藝指標尤其是切割效率在解決了極間冷卻的指導思想、經歷了從20 世紀80 年代至21 世紀初的沉寂后, 目前已有了質的提高。但由于其自身往復走絲的特點,使其切割精度不可能與單向走絲電火花線切割加工進行最終的抗衡,其良好性價比的一個重要體現在于能進行高效、長期穩定的切割加工,尤其體現在高厚度切割方面,因此對于往復走絲線切割加工而言,切割效率的提高及持久性是一個永恒的話題。往復走絲線切割加工效率方面的研究重點可分為兩方面:其一是提高實用的、持續穩定的切割效率,目前持續穩定的效率已達120~140 mm2/min,今后努力的目標希望能達到160~180 mm2/min,且對于150 mm 以上厚度的工件也同樣適用; 其二是提高最高切割效率,目前采用智能脈沖電源,配合復合工作液,最大切割效率已達300 mm2/min。上述指標已接近或達到中檔單向走絲線切割加工的一般效率要求,但運行成本僅僅是單向走絲線切割加工的幾十分之一甚至百分之一[4],因此在中小批量零件的切割生產中具有十分明顯的優勢。
但必須注意的是:往復走絲線切割加工當切割效率超過150 mm2/min 后, 工件表面將逐漸產生嚴重的交叉燒傷痕跡,其最根本的原因還是高效切割時極間放電狀況惡化所致。圖2a 為極間有充足工作液的切割示意及工件切割后表面情況,此時切割表面色澤基本均勻,但如持續增加放電能量(平均加工電流>6 A)至效率超過150 mm2/min 后,切割效率隨著放電能量的增加將上升十分緩慢,而工件表面燒傷則更嚴重,且電極絲斷絲幾率大大升高(圖2b)。此時導致切割效率的提高又遇到另一個瓶頸。工件表面出現嚴重的交叉燒傷痕跡,說明極間處于十分惡劣的放電狀態,其主要問題在于隨著放電能量的增加,放電形成的熱量將使得電極絲帶入切縫(單邊放電間隙約0.01~0.02 mm) 的有限工作介質瞬間汽化,導致極間尤其是在電極絲出口區域處于工作介質很少甚至無工作介質狀態,致使該區域的冷卻、洗滌、排屑及消電離狀態惡化。由于工件和電極絲在該區域得不到及時的冷卻, 造成排屑困難,從而使工件表面產生嚴重燒傷且斷絲的幾率大大增加。在此種加工條件下,任何對于高頻電源的改進措施及伺服控制策略對于切割工藝指標的提高都將收效甚微,因為此時最關鍵問題已轉化為極間放電狀態的惡化及不穩定,所以如何能及時將工作介質帶入放電間隙并將蝕除產物排出切縫已成為能否進一步提高切割效率的首要前提。
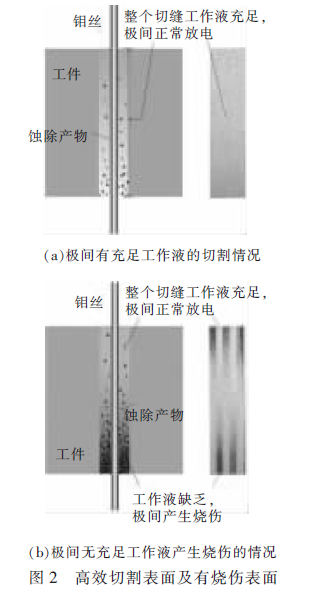
下面分兩個部分來論述提高切割效率的途徑。一方面為在洗滌冷卻較充分前提下(一般切割電流<5 A),提高單位電流蝕除效率;另一方面是在大能量加工前提下(一般切割電流>6 A)提高高效切割效率。
(1)在洗滌冷卻較充分前提下(一般切割電流<5 A),提高單位電流蝕除效率的主要措施:
① 進一步提高脈沖電源的脈沖加工利用率。目前一般的脈沖取樣伺服進給配合佳潤復合工作液的使用,可使脈沖電源的放電脈沖利用率接近甚至超過90 %,而采用智能化的脈沖電源可結合放電間隙狀態的檢測、等能量脈沖電源(圖3)的應用、放電能量的控制及有害脈沖的抑制等技術,在進一步降低電極絲損耗的同時,提高放電脈沖的利用率至95%以上;同時由于抑制了有害脈沖的輸出(如一旦檢測出現持續短路情況就及時切斷脈沖電源), 可使單位電流的切割效率從25~30 mm2/(min·A) 上升至30~35 mm2/(min·A)。但客觀而言,在洗滌、冷卻較充分前提下, 智能電源對切割效率的提高貢獻限,研究的重點主要在電極絲使用壽命的提高方面。
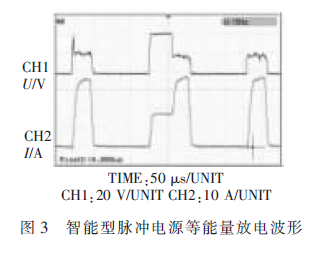
② 對脈沖蝕除方式的研究。放電后工件表面材料的蝕除形式主要有熱熔化蝕除和熱氣化蝕除兩種,業內對于往復走絲線切割加工脈沖能量蝕除方式的研究仍處在一個模糊階段。蝕除方式不僅與蝕除效率有關,還與加工表面的完整性、電極絲的損傷程度等一系列指標有關,是一個值得深入研究的課題。
③ 工作液性能的進一步研究。目前以佳潤復合工作液為代表的工作液主要解決了平均切割電流<5 A 條件下極間的洗滌、冷卻及消電離問題,使極間處于正常的放電狀態[5-7],而切割效率的提高還有一個重要的因素就是單個脈沖的放電蝕除量問題,該問題與放電后能量在極間的傳輸、熱量的擴散等因素有關。鑒于上述機理,工作液應具有更低的電導率,以減少在放電過程中漏電流的能量損失,同時應具有較高的動態粘度, 以有利于壓縮放電通道,使放電能量集中,達到高效蝕除材料的目的,此外還應具有較高的氣化點,以減少極間工作介質的氣化量。
④ 張力控制問題。張力的控制并不能直接獲得加工效率的提升, 但可通過改善加工的穩定性、提高切縫的均勻性獲得切割效率的提高。圖4 是檢測到的一般加工區電極絲張力與絲筒轉速對應圖。從圖中可看出電極絲正反運行時張力的變化是十分明顯的,出現一邊松一邊緊的問題,且換向時導輪的轉動慣量會造成張力的突變[8]。電極絲正反走絲張力的變化會導致切割中電極絲的振動加強,并產生切縫寬度變寬及不均勻,因此如果能解決電極絲張力不均勻問題,將使放電脈沖利用率進一步提升且切縫寬度均勻及收窄,從而能從這方面獲得因為切縫材料蝕除量降低所帶來的切割效率的提高。

⑤ 電極絲進電問題。目前最常用的電極絲進電方式是導電塊進電,導電塊由硬質合金或鎢鋼材料制造,鉬絲以8~12 m/s 的線速度貼著導電塊表面滑動摩擦運動,兩者接觸處為一個短圓弧線段。由于鉬絲與進電塊之間的接觸電阻不穩定,放電能量傳輸到加工區域必然因為有接觸電阻及電極絲自身的電阻產生能量損耗。如能盡可能將進電點移動至靠近加工區域(圖5 所示虛線框位置),減少能量消耗并盡可能獲取更接近于加工區域的取樣信號(通常取樣點和進電點在一起), 將由此獲取加工效率的進一步提高。
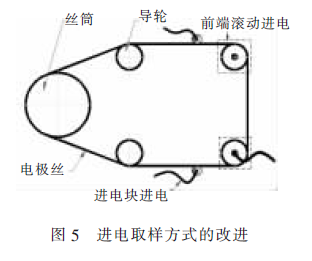
(2)大能量前提下(一般切割電流>6 A)提高高效切割效率問題:
在大能量前提下(一般切割電流>6 A)提高高效切割效率關鍵在于如何解決工作液在極間迅速被汽化[9]的問題,為此采用的主要措施可分為增加極間工作液的進入量的主動措施及減少極間工作液的汽化量的被動措施。
主動措施有:
① 增加噴液壓力及放電間隙。以往往復走絲均采用澆注式冷卻,基本是通過工作液吸附在電極絲上并隨著電極絲帶入切縫,而實驗表明,采用一定壓力將工作液噴入切縫,可將工作液盡可能多地帶入切縫[7],但前提是,必須研制一種不產生泡沫的工作液, 以防止在高壓噴射條件下形成大量的泡沫,影響加工的穩定性,且采用這種方式還須借助脈沖電源的改進,以增加放電間隙的寬度。
② 電極絲的外觀形狀及材料的改變。通過電極絲外觀形狀的改變,如采用絞合、螺旋形狀的電極絲或使電極絲表面具有更好的吸附工作液性能,如毛化電極絲表面,使電極絲能將更多的工作液帶入極間,同時帶出更多的蝕除產物,其中雙絞合電極絲示意如圖6 所示。
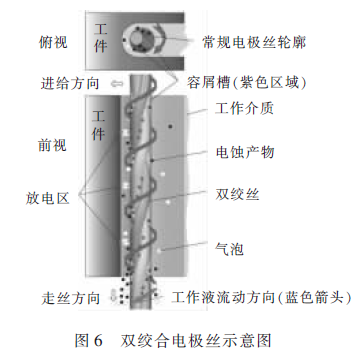
絞合電極絲在走絲過程中可通過自身螺旋狀容納空間及走絲時形成的對液體介質的螺旋吸入效應,盡可能多地“拖拽并吸入”外部及已加工切縫中的工作介質進入放電間隙,同時及時將蝕除產物“強制拖拽”出放電間隙,以提高高效切割時極間的冷卻、洗滌、排屑及消電離作用。由于洗滌、冷卻、排屑及消電離作用大大增強,尤其是強制性“拖拽并吸入”更多的工作介質,將使極間獲得充分的冷卻環境,解決極間因為高效切割產生的工作介質瞬間氣化問題,使電極絲能獲得及時冷卻,從而承載更大的加工能量,提高切割效率。
被動措施有:
① 工作液方面, 在保障極間處于良好洗滌、冷卻、消電離的條件下,使工作液具有更高氣化點的組分,以減少工作液在極間的氣化量,此外還可增加工作液在電極絲表面的吸附性能,讓電極絲能盡可能多地將工作液帶入切縫。
② 設計并采用使工作液氣化率低的脈沖電源及參數,增大放電間隙,并采用“非對稱”脈沖電源。脈沖電源在一個脈沖期間的能量分配及脈沖間隔分配均會導致對工作液產生不同的汽化率,且在正反向走絲時采用不同的脈沖間隔均會在一定程度上減少往復走絲的“非對稱性”。
目前從實施的可行性而言,改變電極絲的截面外觀以提高高效切割效率可行性較強,但電極絲截面形狀的改變還需解決電極絲應力、變形、電極絲直徑控制等問題。
3.電極絲損耗的解決途徑
現有的往復走絲線切割加工由于采用單絲筒循環往復走絲,必然會產生以下缺陷:
(1)貯絲筒通常一次上絲的長度為200~300 m,由于這段電極絲一直在進行往復放電切割,電極絲產生損耗是必然現象。目前采用佳潤復合工作液,以100 mm2/min 的切割效率連續切割時,切割15 萬mm2,電極絲直徑損耗0.01 mm(從直徑0.18 mm 開始)。因此在大面積切割時,將由于電極絲的損耗導致起始切縫與最終切縫因為電極絲損耗而產生寬度不同,對切割精度形成影響。
(2)在大面積切割過程中一旦發生斷絲,由于此時電極絲已從開始到斷絲處有了損耗,如果采用通常的退回原起割點、重新換鉬絲再進行切割的方法,從起割點到斷絲點,就會因為切縫寬度逐漸變窄的原因(暫時不考慮工件變形及軌跡精度等問題),影響電極絲從起割點到斷絲點的進給速度,也就是說, 此時從起割點到斷絲點并不是空切了,而是需要再次切割才能到斷絲點,這樣就會大大延長總切割時間并影響加工精度。
(3) 傳統的往復走絲線切割加工在走絲過程中,存在單邊松絲問題,也就是在絲筒的兩頭,存在電極絲一頭松一頭緊的問題,雖然目前采用的恒張力裝置(如機械重錘式張力機構、機械彈簧式張力機構等)可部分緩解該問題,但同時也會增加斷絲的幾率。
(4)電極絲的損耗會影響到多次切割修整的精度。
為解決上述問題,目前已有廠家在控制系統中采用軟件補償方法來彌補切割中因為電極絲損耗帶來的切縫寬度改變產生的誤差[10],也有廠家采用絲筒上電極絲分段投入加工的方法,如一次切割用絲筒上的一段電極絲,而多次切割,為減少因電極絲損耗對修整的影響,采用另外一段沒有損耗的電極絲進行修整,但上述方法都不能完全解決電極絲損耗帶來的對加工精度的影響。
目前由于電極絲冷拉工藝的日趨完善,鉬絲在冷拉過程中,可按定長拉制。由此提出一種電火花線切割雙絲筒電極絲往復漸進式走絲方式(已申請發明專利), 通過雙貯絲筒使得電極絲在完成高速往復走絲的同時通過往復走絲的不對等控制,使電極絲整體微量推進,以抵消電極絲的損耗,從而使電極絲的損耗在整個切割過程中可通過電極絲的漸進補充而抵消,保障在切割過程中,切縫中的電極絲直徑基本不變。在一定程度上保障了加工精度不會因為電極絲的損耗而降低,此外當斷絲情況發生時電極絲可沿寬度一致的切縫快速空切到斷絲點或在斷絲點原地穿絲。該雙絲筒結構同時保障了加工區域電極絲的張力處于恒定狀態。電火花線切割電極絲往復漸進式走絲方式原理見圖7。
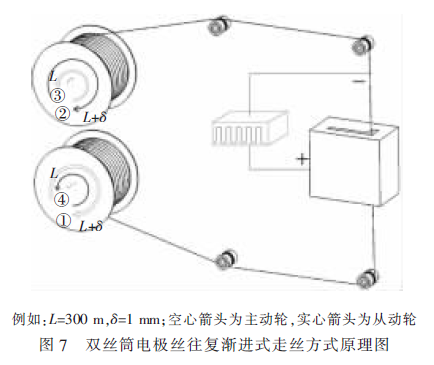
利用單片機控制貯絲筒的轉動,實現電極絲的往復漸進式送絲運動,例如:正向走絲300.001 m 后反向收絲300 m, 再正向走絲300.001 m 后反向收絲300 m……如此往復運動, 每次循環總有1 mm的新絲補充進入加工區域,因而電極絲的損耗可依靠每次多進入加工區域的1 mm 電極絲來補償,以減少加工過程中的電極絲損耗,尤其對于切割高厚度和大切割面積的工件效果更為明顯,從而提高加工精度。且當斷絲現象發生時,電極絲可沿寬度基本一致的切縫快速空切到斷絲點或在斷絲點原地穿絲,大大提高了加工效率。采用這種走絲方式后,由于電極絲損耗可依靠漸進進入加工區域的電極絲進行補償,故損耗對加工的影響程度大大降低甚至可以忽略,因此諸如在單向走絲上適用的技術也可考慮在往復走絲上采用,如抗電解電源技術等。采用這種走絲方式,能基本消除以往電極絲損耗對加工的影響,當然目前這只是一個構想,具體結構及控制的實現還需進一步細化。
4.導絲方式問題
對于往復走絲線切割加工而言,往復走絲導致的對電極絲空間位置的影響是較大的,因此采用導絲器對電極絲進行定位和導向是目前“中走絲機床”普遍采用的方法。但導絲的方式決定了導絲器的精度和壽命。由于電極絲的反復使用及鉬絲的硬度大大高于單向走絲線切割加工黃銅絲的硬度,因此在導絲器材料相同時,往復走絲線切割加工導絲器的使用壽命將大大低于單向走絲線切割加工,其對比情況見表1。
表1 往復走絲與單向走絲線切割加工導絲器壽命比較

由表1 可知,往復走絲線切割加工會大大降低導絲器的壽命, 因此其導絲方式只能以“減少電極絲抖動”為主要手段,如果硬要靠導絲器強制性牽拉電極絲以達到限位的作用是不現實的,這也就是為什么目前“中走絲”導絲器只能用在直體及隨動導絲大錐度機床上的根本原因,至于在沒有隨動導絲的小錐度機床上使用導絲器并進行小錐度切割的加工方式,其導絲器的使用壽命將很短。
本課題組設計了一種六連桿大錐度隨動導絲及噴水機構[11],其原理見圖8。由于電極絲方向始終與導絲器中的V 型槽重合(圖9),設計于導絲器上的噴水嘴噴出的工作液始終能包裹住電極絲并隨電極絲進入加工區,因此能起到很好的洗滌、冷卻和消電離作用,這對于加工精度、切割效率和表面質量的提高均起到積極作用[12]。隨動導絲及噴水機構見圖10a,切割現場見圖10b。
5.結束語
本文分析了往復走絲線切割加工在高效切割、降低絲耗、導絲定位等方面遇到的技術瓶頸,并從放電加工機理方面著手分析,為研究人員提供一個解決問題的參考思路,望能進一步促進往復走絲線切割加工技術的發展。
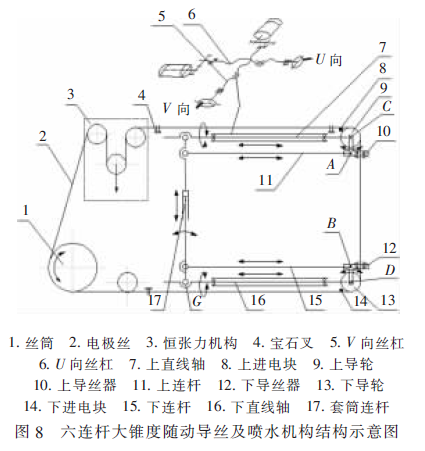
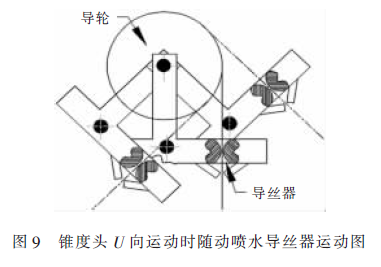
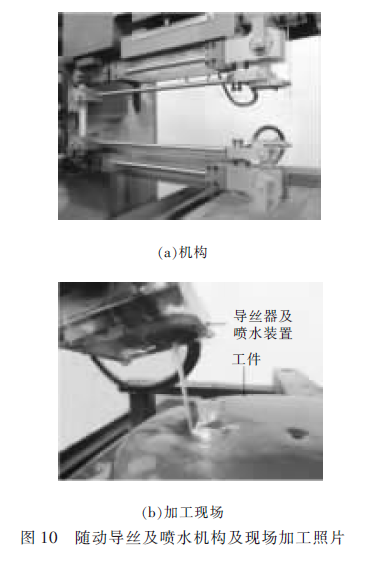
投稿箱:
如果您有機床行業、企業相關新聞稿件發表,或進行資訊合作,歡迎聯系本網編輯部, 郵箱:skjcsc@vip.sina.com
如果您有機床行業、企業相關新聞稿件發表,或進行資訊合作,歡迎聯系本網編輯部, 郵箱:skjcsc@vip.sina.com
更多相關信息