微細電火花制備大長徑比微細電極的工藝研究術
2017-1-3 來源:哈爾濱工業大學機電工程學院 作者:孟潔,白基成,李強,曹剡
摘要:針對電火花塊電極磨削效率高和線電極磨削精度高的優點,采用塊電極磨削為微細電極的粗磨削、線電極磨削為微細電極的中、精磨削方式,對大長徑比微細電極的制作技術進行研究。通過分析微細電火花加工大長徑比微細電極的影響因素,對影響大長徑比微細電極制作的加工參數進行了大量的工藝試驗,得到各參數對微細電極制作的影響規律,優選得到相關的大長徑比微細電極的加工參數,并進行了實驗驗證。
關鍵詞:微細電火花;微細電極;塊電極磨削;線電極磨削;大長徑比
O. 引言
隨著微機電系統的發展,對微型結構的零部件需求量越來越大。目前,加工微型結構的方法很多,其中微細電火花銑削加工技術以其非接觸式加工、不受材料硬度限制等優勢成為加工微型結構的一種重要方法。采用微細電火花銑削技術加工具有微型腔、微小孑L以及階梯孔等微型結構的零部件,需要制備直徑很小的微細電極;另一方面,在微細電火花銑削加工中,微細電極的損耗非常嚴重,微細電極的長度在很大程度上影響了銑削的加工效率,而且微細電極的精度也會影響型腔或者孔的精度,因此需要制備大長徑比微細電極。
目前國內外很多學者對微細電極的制作有相關的研究。日本學者增澤隆久采用線電極磨削裝置加工出直徑為2.軋m的微細軸?。韓國首爾大學的Se HyunAhn等人利用微細電解方法加工出直徑為3mm,長度為4mm的微細電極舊J。美國學者Ra’a A,Said在cu.S04·5H:O溶液中用玻璃絕緣鉑電極的側壁加工出直徑為2軋m,長為6.5mm的銅微細電極‘3』,但是加工效率低,表面質量不理想。哈爾濱工業大學李剛通過采用塊電極粗加工,刃口電極精加工相結合的方法,加工出直徑3.5肛m,長度為60燦m的微細電極,但刃口電極的制作和安裝限制了其發展H J。S.H.Choi等人采用電火花光刻法通過光致抗蝕劑掩模成功加工電極直徑為軋m,長度為3mm,帶有O.2。錐度的大長徑比微細電極。
由于存在二次安裝誤差,采用電解或者光刻法等方法加工的微細電極,無法作為微細電火花銑削加工用的工具電極。因此,對于研究采用微細電火花技術在線制作高精度的大長徑比微細電極的技術具有重要意義。
1.微細電極的制作方法
目前微細電極的制作方法總體分為離線制作和在線制作兩種。離線制作方法有通過冷拔得到金屬細絲,或者通過切削、磨削等方法哺]。通過冷拔得到的金屬絲會出現直徑不一致等缺陷,而通過切削或磨削得到的電極精度會受到很明顯的切削力影響。另外,離線制作的電極再次安裝時會產生二次安裝誤差,重復定位誤差o¨等問題,使經過二次安裝的微細電極無法用于微細電火花銑削加工。在線制作微細電極的方法有電火花塊電極磨削(Block Electrical Discha略e Grind—ing,簡稱BEDG)、線電極磨削(wire Electrical Discha昭e Grinding,簡稱wEDG)、塊電極磨削和線電極磨削相結合的方式(BEDG-wEDG),刃口電極電火花磨削方法等。
塊電極磨削電極時,塊電極與微細電極之間的放電面積大,加工效率比較高。但是塊電極的工作面與工作臺臺面存在垂直度誤差和塊電極本身存在平面度誤差,導致加工的電極產生錐度,尺寸不易控制,所以僅采用塊電極磨削電極很難達到大長徑比的目的。線電極制作微細電極時,待制作電極與線電極之間是點放電,每次放電點比較集中,且脈沖能量小,蝕除的工
件材料很少,使加工效率比較低,但加工精度高。因此將BEDG和wEDG相結合作為大長徑比微細電極的制作方法。
另外,影響大長徑比微細電極在線制作的因素有很多,主要包括:
(1)電極材料
采用電火花加工技術在線制作微細電極時,待制作的微細電極材料應該具有導電性、自身較小的損耗、不易加工成形以及高熔點等特征。鎢熔點很高,且化學性質較穩定,目前微細電極的材料趨向于鎢材料,有利于大長徑比微細電極的制作。
(2)工作液
工作液主要起冷卻、排屑、形成放電通道以及壓縮放電通道等作用。煤油的絕緣性比去離子水好,有利于提高加工精度,但煤油中分解的含碳化合物會產生二次放電,使加工狀態不穩定,且煤油的傳熱性能以及排屑功能差。相比于煤油,去離子水流動性和傳熱性好,有利于排屑和散熱一1;且去離子水可使加工效率高,加工工件的表面形貌好,所以去離子水更有利于大長徑比微細電極的制作。
(3)加工極性
由于待加工微細電極直徑較小,所需脈沖能量小,脈寬很窄,頻率很高。當加工工件接正極時,加工工件的蝕除量遠遠大于工具電極的蝕除量,有利于提高加工效率和降低工具電極的損耗。
(4)脈沖電源
制作大長徑比微細電極時,因為電極尺寸微小,磨削量較大,同時需要保證磨削的加工效率,因此作為微細電火花加工重要部分的脈沖電源,需要能夠同時實現具有微小能量和大能量相結合的多功能脈沖電源,同時脈沖電源的不同參數對微細電火花銑削加工具有較大的影響。
常用的微能脈沖電源的電源模式主要有可控電容電源模式(簡稱TC電源模式),RC電源模式以及可控電阻電源模式(簡稱TR電源模式)。TR電源模式能夠提供很高的脈沖頻率,加工效率較高;Rc電源模式工作可靠,結構簡單,且加工效率比TR的高;而TC電源模式下電流波動較大,材料蝕除不均勻,使電極表面質量和直徑一致性比較差,但是加工效率比前兩者都高。所以在塊電極粗磨削時采用Tc電源模式,線電極中磨削時采用RC電源模式,精磨削時采用TR電源模式。
(5)加工參數
影響電極制作的加工參數很多,如伺服進給速度、進給方式、加工方法等,也會在很大程度上影響電極加工的效率和質量。一般情況下,所選的加工參數需使加工效率高、電極表面形貌好、加工狀態穩定。下面主要針對電火花加工技術在線制作大長徑比微細電極的電參數進行試驗研究,以優選出適合制作大長徑比微細電極的參數。
2.試驗方案及試驗條件
本文研究所采用的試驗設備是哈爾濱工業大學特種加工及機電控制研究所自行研制的微細電火花機床,該機床集在線制作電極、電極在線測量、微細陣列型腔銑削加工于一體。
(1)試驗方案
本文采用塊電極磨削裝置進行電極的粗磨削,旨在提高加工效率;用線電極磨削裝置進行中磨削和精磨削,中磨削的目的是進一步減小電極徑向尺寸,并為精磨削作準備,精磨削主要是提高電極表面質量,保證加工精度。另外因塊電極加工時會產生損耗,為了減小塊電極損耗對加工電極的影響,一般采用塊電極進行兩次粗磨削;為了便于根據加工后的電極直徑、表面質量以及加工需求確定下一工序的具體加工參數,對應的線電極在中磨削和精磨削時也進行兩次磨削。
(2)試驗條件
本文針對影響塊電極粗磨削和線電極中、精磨削大長徑比電極的電參數進行多次工藝試驗,選擇出適合大長徑比微細電極制作的最佳參數,并通過實驗驗證所選的加工參數,試驗過程中所使用的試驗條件如表1所示。
表1制作微細電極的試驗條件
biao 1
3.大長徑比微細電極制作的工藝試驗研究
塊電極粗磨削電極時采用TC電源模式,影響電極磨削的電參數有開路電壓、脈沖寬度、占空比以及電容等,因為塊電極磨削旨在提高加工效率,其加工參數以表2為準,該參數是已經通過大量實驗驗證過,此處沒有必要研究。下面主要對線電極磨削電極進行研究。
3.1線電極中磨削時的工藝試驗
線電極中磨削微細電極主要為了進一步減小電極直徑,并具備一定的表面質量,為精磨削做準備。此時采用RC電源模式。通過對開路電壓、電容、電阻進行單因素試驗研究,分析各個因素對微細電極直徑以及表面形貌的影響規律,進而確定制作大長徑比微細電極的最佳參數。
(1)開路電壓對加工電極的影響
以線電極第一次中磨削為例,加工所需的脈沖能量應比粗磨削時小。加工前的電極直徑為10咄m,電阻、電容分別取100Q、1000pF,電極徑向進給量為10燦m,而其他加工參數不變的情況下只改變開路電壓。在對應的每個開路電壓下,磨削長度為10毗m,結果如圖l所示。
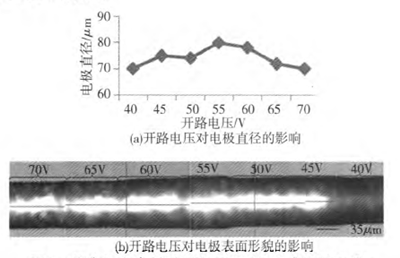
圖1線電極中磨削時開路電壓對加工電極的影響
從圖la可明顯地看出,在所選試驗條件范圍內,線電極中磨削時,當開路電壓小于55V時,脈沖能量比較小,加工時易出現短路,導致電極直徑減小;當開路電壓大于55V時,微細電極的直徑隨著開路電壓的增大而減小。但脈沖能量增大,蝕除凹坑變大,表面質量變差,如圖1b所示。綜合加工效率和表面質量,優選60V作為中磨削的開路電壓。
(2)電阻對加工電極的影響
以線電極第一次中磨削為例,加工前的電極直徑為8毗m,在開路電壓為60V,電容為1000pF,電極徑向進給軋m而其他加工參數不變的情況下只改變電阻。在對應的每個電阻下,磨削長度為15毗m,結果如圖2所示。
從圖2可以看出,在所選的電阻條件范圍內,電阻值大時,電流小,蝕除的工件材料較少,電極直徑變化小,但蝕除凹坑小,電極表面質量好。當電阻為100Q時,加工狀態不穩定,易發生短路現象。所以選擇510n為中磨削的電阻值。
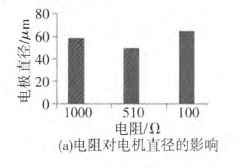
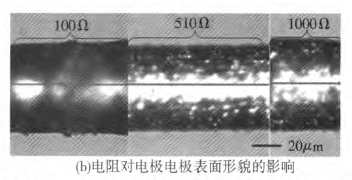
圖2線電極中磨削時電阻對加工電極的影響
(3)電容對加工的影響
以線電極第二次中磨削為例,加工前的電極直徑為3軋m,當開路電壓取60V,電阻取510Q,電極徑向進給靴m而在其他加工參數不變的情況下只改變電容。在對應的每個電容檔下,磨削長度為12毗m,結果如圖3昕示。
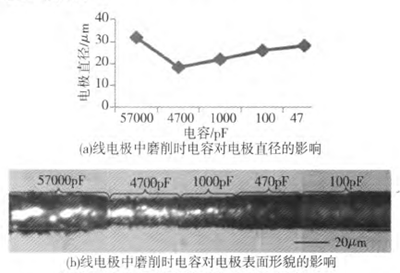
圖3線電極中磨削時電容對電極的影響
從圖3可以看出,在所選電容條件范圍內,除了57000pF點,電極直徑隨電容數值的減小而增大,其主要因為電容減小,脈沖能量減小,單位時間內蝕除的材料減少,且放電間隙減小,廢屑不能及時排出,使電極直徑增大,而電容在57000pF和4700pF下加工的電極表面形貌差。所以在中磨削時優選1000pF為電容參數。
3.2線電極精磨削時的工藝試驗
經過線電極第一次精磨削后,電極尺寸已經很接近目標尺寸,為了進一步提高電極表面質量,提高加工精度,進行線電極第二次精磨削。此時采用加工電極徑向“零進給”¨0|,線電極“零運絲速度”以及主軸“非伺服運動”等加工策略。在線電極精磨削電極時采用的是TR電源模式,主要是精修電極的表面質量,所以所需能量很小。以下主要對開路電壓、電阻以及脈寬和占空比進行工藝實驗,分別研究它們對電極直徑和電極表面形貌的影響。
(1)電阻對加工的影響
以線電極第一次精磨削為例,所需的脈沖能量很小,且加工時徑向進給量很小,重在提高表面質量。當加工前的電極直徑為4軋m,開路電壓為28V,脈寬為3200 ns,占空比為1:3,電極徑向進給釓m而其他加工參數不變的情況下只改變電阻,在對應的每個電阻下磨削長度為12毗m,結果如圖4所示。從圖4可以看出,在試驗所選數據范圍內,電極直徑隨電阻值的減小而減小,因電阻減小,電流增大,單位時間內蝕除的工件材料就增加,電極直徑變小,但蝕除凹坑會變大,導致加工質量變差。所以優選1000Q為精磨削的電阻參數。
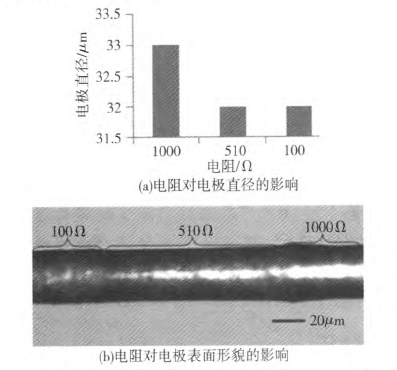
圖4線電極精磨削電極時電阻對加工電極的影響
(2)開路電壓對加工的影響
以線電極第二次精磨削電極為例,經過線電極第一次精磨削的修整,電極表面有很大的改善。為進一步提高表面質量和直徑一致性,進行線電極最終精磨削。為了避免線電極振動對電極直徑一致性的影響,將運絲速度設為零,而且在檢測到有放電現象時,電極徑向不進給,即徑向零進給,其余加工參數和第一次精磨削時的相同。如圖5所示上下分別為采用28V和24V電壓精磨削加工的電極表面形貌,可以明顯地看出在24V時加工的電極表面形貌比28V要好。所以在線電極第一次精磨削時選用28V的開路電壓,在提高加工效率的情況下,保證加工精度;在第二次精磨削電極時選取24V的開路電壓,以進一步提高電極表面質量。
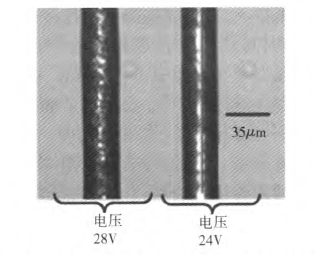
圖5不同電壓下精磨削的電極表面形貌
(3)脈寬及占空比對加工的影響
用線電極精磨削電極時,脈寬以及占空比也是影響微細電極制作的影響因素,以第一次精磨削為例,加工前電極直徑為10釓m,在開路電壓為28V,電阻為1000Q,電極徑向進給量為軋m,以不同的脈寬和占空比做實驗,結果如圖6所示。從圖6可以看出,在試驗所選條件范圍內,占空比不變時,電極直徑隨脈寬的增大反而增大,原因是在脈寬為3200ns時,加工能量較小,加工時出現輕微短路現象,使電極直徑更小;當脈寬不變時,電極直徑隨著占空比的減小基本呈增大趨勢。因精磨削時重在提高微細電極表面質量,在保證無明顯短路的前提下,盡量使加工能量小,蝕除凹坑小,達到表面質量好的目的。所以選擇脈寬為3200ns,占空比為l:3作為精磨削電極的參數。
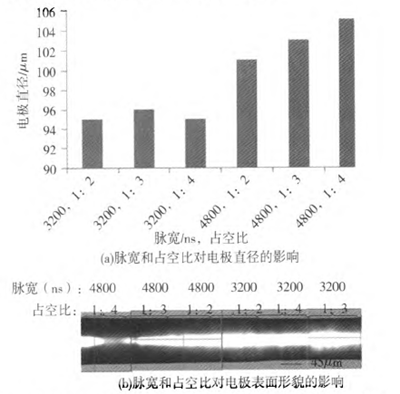
圖6線電極精磨削電極時脈寬和占空比對加工電極的影響
經過多次試驗研究,總結出制作單根大長徑比微細電極的具體加工工藝規劃,如表2所示。經過試驗,驗證,依據表2的加工參數,穩定地加工出直徑為4μm,長度120μm以及直徑為7μm,長度為440μm的大長徑比微細電極,其長徑比高達60以上,且直徑偏差小于1μm,如圖7和圖8所示。
表2微細電極的加工工藝規劃及參數
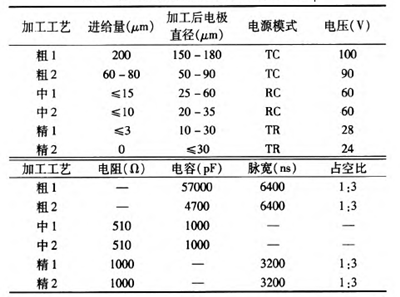
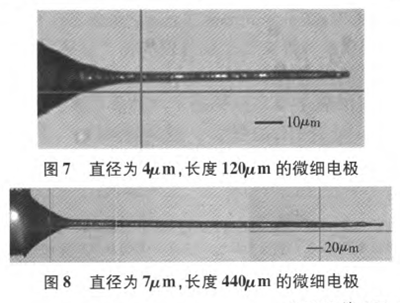
4.結論
本文主要研究了采用微細電火花技術制作大長徑比微細電極的方法,通過理論分析和試驗研究,得出了以下結論:
(1)根據塊電極電火花磨削和線電極電火花磨削的特點,利用多模式微能脈沖電源,采用塊電極磨削裝置進行電極的粗磨削,線電極磨削裝置進行中磨削和精磨削的大長徑比微細電極加工方法,并分析、總結了相應的的加工方案和加工條件;
(2)通過大量試驗研究了在線電極磨削電極時開路電壓、電阻、電容、脈寬以及占空比等對電極直徑和電極形貌的影響規律,獲得了適合大長徑比微細電極制作的優選參數;
(3)通過實驗驗證,使用該優選參數穩定地加出了電極直徑為7μm,長度440μm以及直徑為4μm,長度為120μm的大長徑比微細電極,長徑比高達60以上,且直徑偏差小于1盧m,達到了直徑小、長徑比大的預期效果。
投稿箱:
如果您有機床行業、企業相關新聞稿件發表,或進行資訊合作,歡迎聯系本網編輯部, 郵箱:skjcsc@vip.sina.com
如果您有機床行業、企業相關新聞稿件發表,或進行資訊合作,歡迎聯系本網編輯部, 郵箱:skjcsc@vip.sina.com
更多相關信息