分層厚度對微細電火花銑削加工模具及熱壓制品表面粗糙度的影響
2017-1-6 來源: 大連理工大學機械工程學院 作者:項得勝,王會,李劍中,虞慧嵐,余祖元
摘要:分層厚度直接影響微細電火花銑削加工的加工效率及表面粗糙度。為了合理規劃微細電火花銑削加工的分層厚度,提高加工效率,研究了分層厚度對微細電火花加工的模具型腔及相應熱壓成形制品表面粗糙度的影響, 同時分析了熱壓成形制品表面與微模具型腔表面之間的關系,以及熱壓前、后微模具型腔表面輪廓的變化。結果表明:當電極軌跡重疊率一定時,模具型腔底面的表面粗糙度值隨著分層厚度的增加而增大; 分層厚度對型腔側壁表面粗糙度無明顯影響;熱壓制品表面輪廓算術平均偏差小于模具型腔表面輪廓算術平均偏差;熱壓后的模具表面輪廓發生了變化,表面粗糙度值Ra 和峰高Rpk 減小,峰谷Rvk 增大。
關鍵詞:微細電火花加工;微模具;熱壓成形;表面粗糙度
隨著微機械電子系統的發展,微小制件得到了廣泛的應用[1-2]。微注塑及微熱壓作為聚合物微塑成形技術,因其制品精度好,成形效率高,使其在電子、航空航天、生物科技及精密儀器等領域得到廣泛應用[3]。微熱壓成形因聚合物流動少,能有效地避免內部應力,被應用于成形更精巧的結構[4]。聚合物微熱壓成形是在合適的溫度、壓力下,模具的微小結構復制到聚合物基板的一種工藝。
微模具的加工成為微塑成形的關鍵,因模具結構微小,尺寸精度及表面質量要求高,傳統的制造方法已不能滿足要求。因此,LIGA 技術、微銑削加工技術、微細電化學加工技術、微細電火花加工技術等先進制造工藝被應用于微模具的加工領域[5]。由于電火花加工是非接觸式加工,工具與工件間無宏觀作用力,所以利用簡單截面的柱狀電極,采用微細電火花逐層銑削的加工方式,能在任何導體及半導體材料上加工出任意復雜的三維結構[6]。
分層厚度是微細電火花銑削加工中的重要參數,既影響加工過程中的工具損耗,也直接影響三維結構加工的效率,層厚越大,加工效率越高。微細電火花加工的模具型腔表面比光刻工藝加工的更粗糙;此外,聚合物材料的性質使熱壓制品表面輪廓與微細電火花加工的模具型腔表面并非完全復制的關系。因此,微細電火花銑削加工的模具型腔表面粗糙度與熱壓制品表面粗糙度之間的關系,以及分層厚度對兩者表面質量的影響值得研究,以達到合理規劃分層層厚、提高加工效率的目的。本文采用微細電火花銑削加工工藝,在放電參數、電極軌跡重疊率一定的情況下,加工不同分層層厚的模具型腔。實驗選取PMMA(聚甲基丙烯酸甲酯)作為熱壓成形材料,以Ra、Rpk、Rvk 作為表面質量的評定參數,研究了制品與模具表面輪廓的關系,以及分層厚度對模具側壁、底面及制品相應表面的影響。
1.實驗裝置
微模具型腔加工設備為自制立式微細電火花加工機床(圖1),其X、Y、Z 3 個移動平臺的最小分辨率均為0.1 μm,單向重復定位精度為1 μm,最大行程為204 mm。旋轉主軸徑向跳動在1 μm 以內,最大轉速為40 000 r/min。
本文所涉及的熱壓成形試驗均在圖2 所示的熱壓成形機上完成,該熱壓成形機是大連理工大學微系統研究中心自行研制而成。其上下熱壓采用獨立的溫度控制,控制精度為±1 ℃;壓力通過傳感器進行反饋控制,控制精度為±40 N;控制系統的軟件采用面向對象的程序設計方法設計,可實現手動操作及全自動運行,均滿足實驗要求。
2.實驗方法及過程
2.1 模具型腔的設計
本試驗設計的模具結構見圖3。三維型腔的設計尺寸為600 μm×600 μm×102 μm,其側壁分別有60°、45°的傾角。具有傾角的側壁結構一方面有利于熱壓制品的脫模,降低制品次品率;另一方面,可得到不同分層厚度條件下,側壁臺階形誤差的大小及對側壁表面質量的影響。
2.2 模具型腔的加工
微細電火花銑削加工中, 選取的層厚不同,模具型腔的表面形貌也會不同,其對熱壓制品表面輪
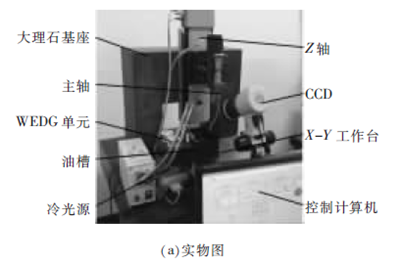
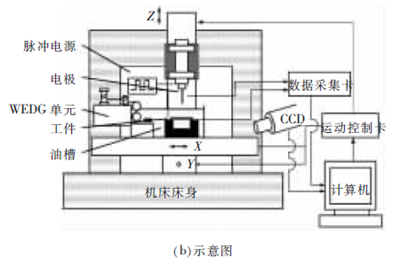
圖1 微細電火花加工裝置
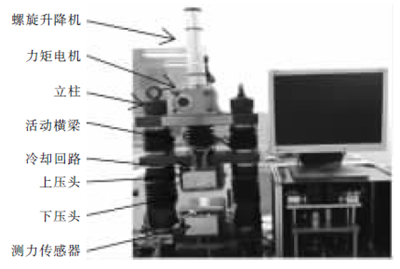
圖2 熱壓成形機
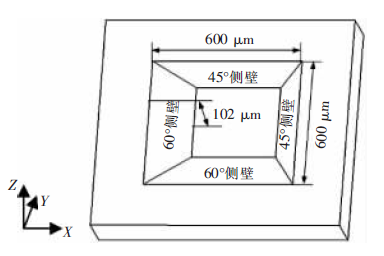
圖3 模具三維模型
廓特征的影響值得研究。因此,在相同的工藝參數下,選擇了不同層厚來加工模具型腔,分層厚度分別為0.5、1、1.5、2、3、4 μm。微細電火花銑削加工時的工藝參數(如開路時的掃描速度、短路的后退速度、短路電壓、開路電壓及插補步長等)見表1。
表1 微細電火花銑削加工條件
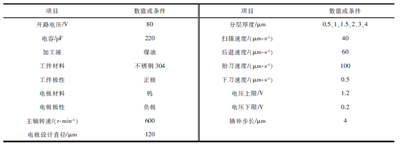
2.3 熱壓成形
熱壓成形的主要工藝參數有:保壓壓力、保壓時間、保壓溫度、脫模溫度,這些參數直接影響熱壓制品的成形質量。本試驗的熱壓成形參數見表2。
表2 熱壓成形參數
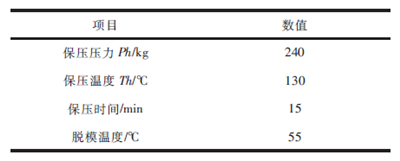
熱壓過程中溫度、壓力隨時間的變化曲線見圖4。熱壓成形法制作聚合物微器件的工藝過程為:
(1)將模具及聚合物板材加熱到玻璃化轉變溫度Tg 以上。
(2)在保壓溫度Th 下,加壓Ph 并保持一定的時間,使聚合物充滿模具型腔。
(3)在加壓的條件下,將模具和聚合物制品冷卻到脫模溫度(玻璃化轉變溫度Tg 之下)脫模。壓印力一直保持到脫模時釋放,是為了避免過早地釋放熱壓壓力造成熱壓制品的回彈及變形。
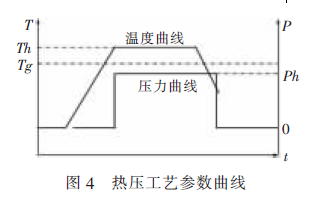
3 實驗結果
3.1 模具型腔的加工結果
加工后的模具型腔SEM 掃描電鏡照片見圖5。由于采用分層銑削的原因,在加工側壁輪廓表面不可避免地存在微小的臺階形誤差, 分層層厚越大,臺階形誤差越大(圖6)。
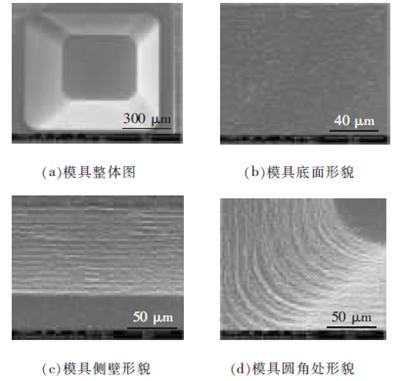
圖5 模具型腔的SEM 圖
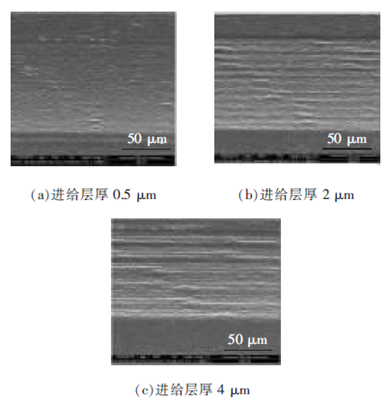
圖6 不同分層厚度下的模具側壁形貌
加工模具型腔后的工具電極見圖7??煽闯觯谖⒓氹娀鸹▽訉鱼娤髟砑庸ず蟮碾姌O端部保持不變,無明顯損耗圓角。
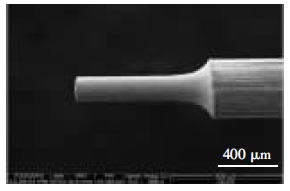
圖7 微模具加工所用刀具
利用精密測量顯微鏡對模具進行測量,模具型腔的尺寸見表3。可見,隨著分層厚度的增大,加工時間減少,效率提高。
3.2 制品成形結果
在表2 所示的熱壓參數下進行了5 組熱壓成形試驗,選取其中一組表面質量較好、無明顯缺陷的熱壓制品進行三維輪廓的測量。利用測量軟件輸出模具及制品對應區域的輪廓曲線,并在同一坐標下繪制兩者的輪廓線。模具型腔側壁與制品側壁的擬合圖見圖8, 可見制品輪廓線與模具輪廓線基本重合,很好地復制了模具尺寸形貌。
表3 模具尺寸數據
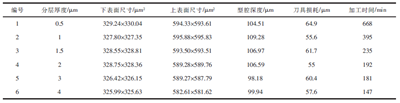
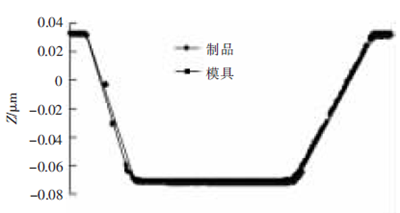
圖8 模具與熱壓制品輪廓擬合圖
熱壓制品的SEM 圖片見圖9??梢宰C明,在表2所示的熱壓參數下,制品表面輪廓復制良好。此外,從圖9 還可發現,制品底面微觀輪廓復制了電火花加工產生的放電凹坑,其側壁輪廓也清晰地復制了微細電火花銑削產生的臺階形誤差。
每個模具的熱壓制品各選3 個進行尺寸測量,并統計X、Y、Z 所有尺寸上的收縮率,求得各向收縮率的均值及上下偏差,結果見表4??梢?,X、Y、Z 向的收縮率均值分別為0.380 %、0.372 %、0.373 %,由此可得熱壓制品各向收縮率一致,這與注塑成形塑料制品的收縮率存在各向異性[7-8]有明顯區別。
3.3 熱壓制品與模具型腔表面關系分析
3.3.1 表面粗糙度評定參數選取
通常評價表面質量的標準大都采用輪廓算術平均偏差Ra,但其對表面微觀幾何形狀的描述是不夠完善的, 表面微觀輪廓的很多信息會被平均掉。
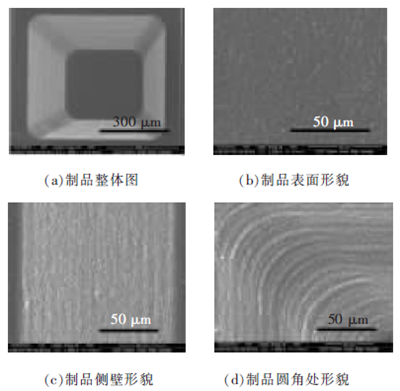
圖9 制品SEM 圖
因此,為了盡可能準確地表征模具及制品表面輪廓的信息,本文引入表面粗糙度參數Ra、Rpk、Rvk[9]來表征熱壓前、后模具及制品的表面輪廓信息。
3.3.2 制品與模具底面表面輪廓分析
利用白光干涉儀對模具熱壓前、后及熱壓制品進行三維輪廓掃描,得到其三維點云數據。由圖10可知,制品表面微觀輪廓與模具表面微觀輪廓存在共軛關系。利用專業軟件對得到的點云數據進行分析,測得模具及制品表面粗糙度數據,并進行對比分析。
表4 制品尺寸及各向收縮率
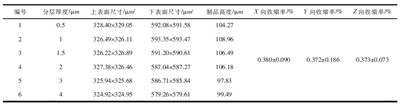
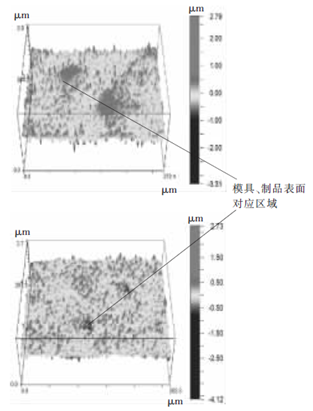
圖10 模具及熱壓制品表面測量結果
從熱壓制品中選出表面完整、無明顯缺陷的一組進行底面表面輪廓對比分析。利用專業測量軟件對白光干涉儀獲取的熱壓前、后模具及熱壓制品表面輪廓三維點云數據進行測量, 每個面各測量5次, 得到各個表面粗糙度參數Ra、Rpk、Rvk 的均值及上、下偏差。采用折線圖的形式直觀地將熱壓前、后模具表面微觀輪廓與熱壓制品表面輪廓進行對比(圖11~圖13),其中,橫坐標編號1~6 分別對應表3、表4 所示的編號1~6。
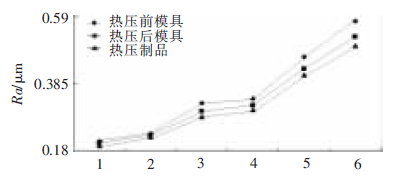
圖11 輪廓算術平均偏差Ra 對比
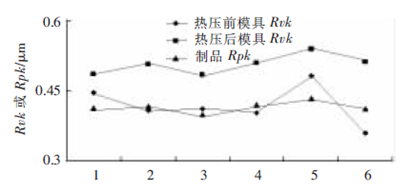
圖12 表面輪廓Rvk、Rpk 對比
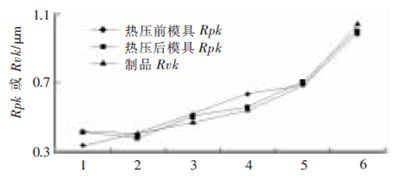
圖13 表面輪廓Rpk、Rvk 對比
3.3.3 模具及制品側壁表面輪廓分析
對模具60°的側壁及熱壓制品相應表面進行了表面輪廓的測量。圖14 是采用三維輪廓測量儀得到的結果,圖15 是模具及制品對應側壁的SEM 圖。可得制品側壁表面輪廓與模具側壁表面輪廓也存在著共軛的關系。
由于制品側壁表面質量受脫模影響較大,因此每個模具的熱壓制品各選3 件進行60°側壁表面輪廓的測量。采用專業測量軟件對每個制品的數據分別進行5 次測量,獲得每個制品表面粗糙度參數的均值。然后,對每個模具的3 件制品的表面粗糙度參數均值進行數據處理,得到各個模具對應制品側壁粗糙度參數的均值及上、下偏差。
熱壓前、后模具60°側壁及制品相應表面輪廓算術平均偏差Ra 對比見圖16。熱壓前、后模具60°側壁表面Rpk 值及制品相應表面Rvk 值對比見圖17。熱壓前、后模具60°側壁表面Rvk 值及制品相應表面Rpk 值對比見圖18。圖16~圖18 中的橫坐標編號1~6 分別對應表3、表4 所示的編號1~6。
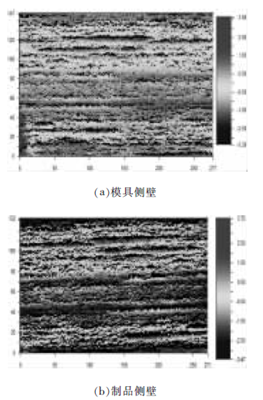
圖14 模具與制品側壁輪廓測量
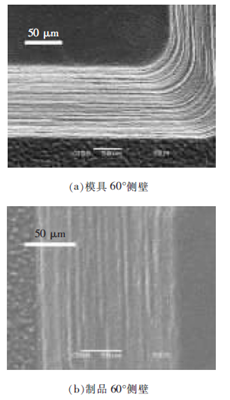
圖15 型腔與制品側壁SEM 圖
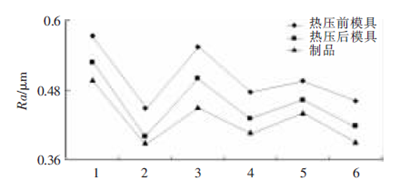
圖16 側壁表面輪廓算術平均偏差Ra 對比
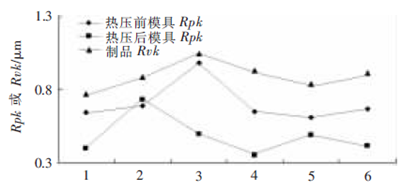
圖17 熱壓前后模具側壁表面輪廓Rpk 對比
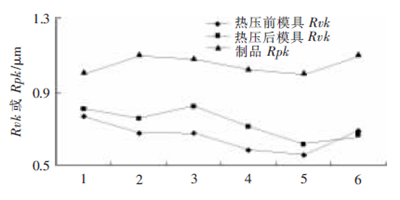
圖18 熱壓前后模具側壁表面輪廓Rvk 對比
4 結果分析
4.1 分層厚度對模具底面及制品相應表面輪廓的影響
由模具與熱壓制品的底面輪廓算術平均偏差Ra 對比(圖11)可知,隨著微細電火花銑削中分層厚度的增大,模具表面粗糙度Ra 值也增大。這是因為在分層去除微細電火花銑削加工中,兩條相鄰的電極運動軌跡之間存在切削痕跡(即刀痕,在Z 軸方向),當電極軌跡重疊率一定時,隨著分層厚度的增加,刀痕殘留高度也隨之增加。在微細電火花銑削加工中,分層厚度的增加使加工中短路、拉弧的現象增多,加工不穩定;分層厚度減小后,表面的掃描更均勻, 放電凹坑的相互重疊使表面粗糙度Ra值減小。
在熱壓過程中,模具表面和熱壓制品間存在著接觸。一方面,模具表面輪廓會復制到熱壓制品表面;另一方面,會使模具表面輪廓形貌改變。熱壓后模具底面的峰谷參數Rvk 較熱壓前增大,這是因為電火花加工表面由于受到瞬時高溫作用并迅速冷卻而產生殘余拉應力,往往出現顯微裂紋,其耐疲勞性能較低。由于在熱壓中PMMA 與模具表面存在力的作用及摩擦[10-11],而使模具表面顯微裂紋擴展,表現為Rvk 增大。熱壓后模具底面表面輪廓算術平均偏差Ra 及峰高參數Rpk 有減小的趨勢, 這與熱壓過程中PMMA 與模具表面的摩擦及相互作用力有關。
熱壓制品與模具表面輪廓存在共軛關系,熱壓制品的表面粗糙度Rpk 與模具表面粗糙度Rvk 對應,熱壓制品的表面粗糙度Rvk 與模具表面粗糙度Rpk 對應(圖12、圖13)。由于PMMA 的收縮及回彈特性, 熱壓制品的表面Ra 值較熱壓前后模具表面都減小;熱壓制品表面Rpk 比熱壓后模具表面Rvk小,兩者變化的走勢相同;制品表面Rvk 的變化趨勢也與熱壓后模具表面Rpk 的變化趨勢相同。
4.2 分層厚度對模具及制品側壁表面輪廓的影響
由圖16~圖18 可看出,分層厚度的大小對模具側壁表面粗糙度Ra、Rpk、Rvk 無明顯影響。熱壓后模具側壁表面輪廓發生變化,其中,Ra、Rpk 有減小的趨勢,Rvk 有增大的趨勢。這是因為在熱壓成形過程中,PMMA 與模具側壁表面作相對運動時, 由摩擦導致模具表面微凸峰磨損,表面輪廓發生變化。熱壓制品側壁表面與模具側壁表面存在著復制的關系, 且兩者側壁表面粗糙度的變化趨勢相同。由于PMMA 的收縮、回彈特性及脫模過程中存在的摩擦力, 導致熱壓制品側壁表面粗糙度Ra 值較模具側壁小。在制品脫模的過程中,制品側壁與模具側壁的摩擦力大,作用時間長;此外,脫模方向輕微的偏斜會導致摩擦力迅速增大,使制品側壁局部出現破裂。因此,熱壓制品側壁峰高參數Rpk、峰谷參數Rvk 較熱壓后模具側壁Rvk、Rpk 要大。
5 結論
本文通過實驗研究了微細電火花三維銑削加工中,分層厚度對模具型腔側壁、底面的表面質量的影響,并分析了熱壓成形中,模具表面輪廓的變化及制品與模具型腔的復制關系,得到以下結論:
(1)在放電參數與電極軌跡重疊率一定時,隨著分層厚度的增加,模具型腔底面表面粗糙度值也增大。在分層厚度較大時,應當增加刀具軌跡重疊率,以使底面輪廓掃描得更均勻。
(2)分層厚度對模具側壁表面粗糙度Ra、Rpk、Rvk 沒有明顯影響。在對側壁臺階形誤差無嚴格要求的情況下, 適當地增大分層厚度可提高加工效率,且不會改變制品側壁表面粗糙度大小。
(3)熱壓前、后,模具底面及側壁表面輪廓發生變化, 表現在表面粗糙度參數值Ra、Rpk 減小及Rvk 增大。
(4)熱壓制品的表面輪廓與模具表面輪廓存在著復制的關系,但又有不同。熱壓制品底面表面粗糙度值Ra、Rpk、Rvk 較熱壓后模具底面粗糙度值Ra、Rvk、Rpk ?。恢破穫缺诒砻娲植诙戎礡a 較模具側壁粗糙度值Ra 小, 而制品側壁表面粗糙度值Rpk、Rvk 則大于模具側壁粗糙度值Rvk、Rpk。
投稿箱:
如果您有機床行業、企業相關新聞稿件發表,或進行資訊合作,歡迎聯系本網編輯部, 郵箱:skjcsc@vip.sina.com
如果您有機床行業、企業相關新聞稿件發表,或進行資訊合作,歡迎聯系本網編輯部, 郵箱:skjcsc@vip.sina.com
更多相關信息