鋼軌道岔軌面精磨機研究
2017-12-21 來源:- 作者:-
摘 要: 針對鋼軌道岔軌面打磨精密化的要求, 通過對各型鋼軌軌面形狀的分析, 提出鋼軌軌面打磨機的設計方案, 經過分析、 比較選擇采用可以升降、 橫移、 角度可調的精度機來進行鋼軌軌面的精密打磨, 精磨機設計及加工簡單, 操作簡便, 實用性強。
關鍵詞:鋼軌 道岔 軌面 精磨機
1 、引言
隨著鐵路事業的快速發展,高鐵新線建設大規模開展,既有線路的全面技術提升,對高鐵 (提速) 線路道岔平面、正線軌頂面的平整度要求越來越高,同時尖軌的非作用邊病害也需要整治。如果不及時處理,將直接影響提速道岔的使用壽命和線路設備的安全運行。
2 、國內外研究開發現狀
2.1 國內現狀
目前道岔平面、正線軌頂面及尖軌的非作用邊的打磨整修作業主要采用手提砂輪進行人工打磨。因作業效率較低,難以保證打磨質量,同時因需攜帶發電機組作業,易對人身和行車安全構成危險。
2.2 國外現狀
v據現有文獻,尚未發現國外打磨機能同時具有對道岔平面、正線軌頂面及尖軌的非作用邊進行打磨的多功能小型打磨維護設備。
3 、目前國內主要使用的各種鋼軌軌型
國內使用的鋼軌軌型主要有 38 kg/m、43 kg/m、50kg/m 、60 kg/m 、75 kg/m ,以下就線路上使用最為常見的60 kg/m 鋼軌軌頭進行分析。60 kg/m 高速鐵路用鋼軌的型式尺寸見圖 1,圖參照 TB/T3276。
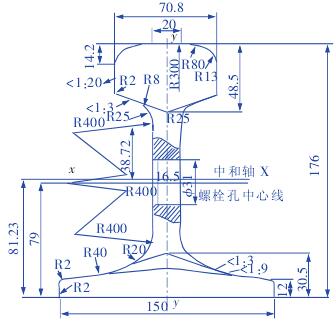
圖 1 高速鐵路用 60 kg/m 鋼軌斷面圖
60 kg/m 鐵路用熱軋鋼軌的型式尺寸見圖 2,圖參照GB2585。
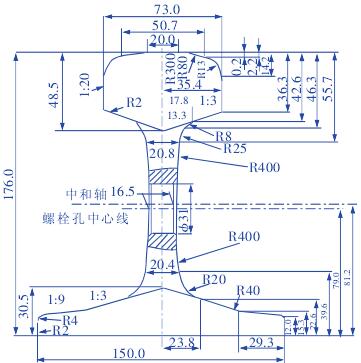
圖 2 60 kg/m 熱軋鋼軌斷面圖
從 2 種鋼軌截面圖可以看出,軌面圓弧半徑一致,均為 R300、R8、R13,只是寬度 70.8、73 及其余尺寸的微小差別。從打磨角度考慮,理想的結果是打磨后的軌面形狀與標準的軌型完美貼合。比較理想的是打磨頭在打磨時逐步仿形達到接近鋼軌軌面形狀的打磨效果。
4 、打磨效果分析及設計方案鋼
軌軌面的打磨要求為,用 1 m 直尺檢查平面誤差為0~ 0.2 m m ,作用邊誤差±0.3 m m ;對于鋼軌平面及肥邊的打磨要求為用 1 米直尺檢查平面誤差為 0.3 mm,軌距角角度 45°,軌距角成圓弧形,角磨機打磨無明顯凹坑。根據打磨效果測量要求制定設計方案。
4.1 第 1 種設計方案
根據鋼軌軌頭形狀的不同,制造不同形狀的打磨頭,打磨頭通過內燃汽油機動力驅動,完成鋼軌的打磨。
4.2 第 2 種設計方案
根據鋼軌軌頭形狀的不同,制造不同形狀的銑削刀盤,銑削刀盤為多個,刀盤通過內燃汽油機動力驅動,通過多個刀盤的逐次銑削使不符合要求的、不規整的鋼軌符合最
終的使用要求。
4.3 第 3 種設計方案
根據軌頭形狀的不同,采用平行樹脂砂輪,在打磨時根據鋼軌形狀,調整升降、橫向移動機角度偏轉,依次對鋼軌斷面進行打磨,打磨出符合要求的鋼軌。
4.4 方案比較
方案 1 根據鋼軌軌頭形狀的不同,制造不同形狀的打磨頭。此方案的好處是鋼軌形狀根據打磨頭的形狀而變,看似好像可以做到一步到位的打磨效果,實際上存在有打磨頭耐用度的問題。如果做成普通的樹脂砂輪,砂輪更換頻繁,無實際使用意義,如果做成硬質合金砂輪,雖較樹脂砂輪耐用,但造價較高。
方案 2 根據鋼軌軌頭形狀的不同,制造不同形狀的刀盤。此種方案的優點是鋼軌的形狀可一次銑削完成,缺點是同一臺機器上需根據鋼軌形狀制造多種切削深度的刀具,制造難度較大,不適用于生產現場,不適合于批量生產。
方案 3 針對不同形狀的鋼軌,采用普通的樹脂砂輪,通過調整升降、橫向移動、角度偏轉機構即可完成對鋼軌的打磨。方案 3 比較合適,制造簡單,操作簡便,所以選擇方案 3
作為內燃道岔軌面精磨機的設計方案。
5 、磨削原理
v方案 3 的磨削原理,見圖 3。采用樹脂砂輪進行磨削,砂輪的中心線或中心線的平行線過鋼軌斷面圓弧的中心,且與圓弧相切,通過調整,調整角度 α,逐次完成鋼軌軌面圓弧面的打磨。按照方案 3 的磨削原理,樹脂砂輪中心線或中心線的平行線過鋼軌斷面圓弧中心且與圓弧相切,需要設計一系列機構配合完成鋼軌軌面的打磨,需設計砂輪在鋼軌上的走行機構,砂輪逐漸接近鋼軌的升降機構,橫移機構,為了實現相切的角度擺動機構,驅動砂輪運轉的傳動機構,由這一系列機構共同來實現對鋼軌軌面的打磨。
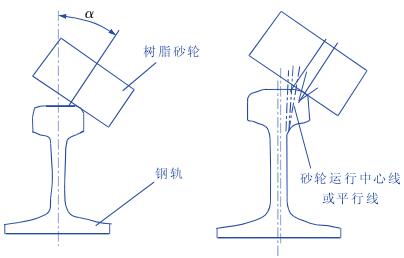
圖 3 樹脂砂輪磨削
6 、內燃道岔軌面精磨機的總體機構
內燃道岔軌面精磨機的總體機構,詳見圖 4。
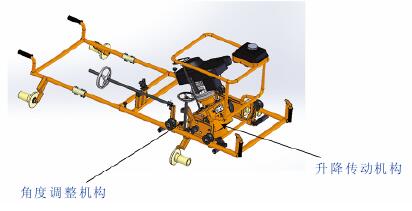
圖 4 道岔軌面精磨機的總體機構圖
7 、機構設計
7.1 走行機構的設計
對于走行機構的設計主要考慮以下幾點:打磨頭的縱向移動,打磨頭的橫向移動,走行機構與鋼軌的絕緣問題,走行機構自身的絕緣問題,方便運輸的問題,與其他機構的結合問題等。考慮打磨頭需縱向移動及由于運動于鋼軌之上,設計走行機架并安裝 4 個尼龍絕緣輪分別跨騎于鋼軌之上;考慮打磨頭在打磨道岔部位軌頂面時需橫向移動,走行機架需有足夠的長度,根據目前道岔的使用情況,打磨頭的橫向移動范圍初定 400 mm,即工作于走行機架的其余機構在走行機架上的移動范圍 0~400 mm;考慮走行機架的自身絕緣問題,在走行機架右端設計絕緣棒,將走行機架左右兩部分絕緣;考慮到機架便于運輸的問題,將走行機架設計成可左右快速拆解的機構。詳見圖 5。
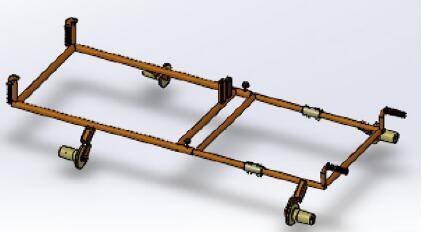
圖 5 走行機架簡圖
7.2 橫移機構的設計
橫移機構的設計主要考慮了橫移距離、快速移動、精確移動等問題。由于橫移距離與走行機架配合工作,在設計橫向移動時設計加長絲桿配合螺母解決了橫向移動的問題,并設計有快速螺母及快速夾緊機構,既解決了快速移動的問題,又具有精確移動的功能。
7 .3 角度調整機構的設計
角度調整機構的設計主要考慮了角度調整范圍問題、角度調整精度問題等。根據打磨質量效果分析,打磨的角度范圍定在 10°~50°之間,此種范圍的調整可通過連桿活節螺母調整機構完成,活節螺母設計成小螺距梯形螺紋,同時與活節螺母連接的角度調整絲桿設計成小間隙配合絲桿,絲桿轉動設計離合分度裝置完成角度的高精度調整。詳見圖 6、圖 7、圖 8、圖 9。
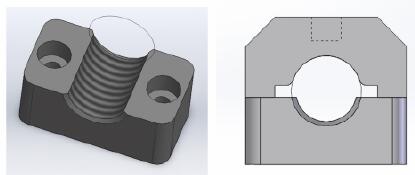
圖6 橫移快速螺母夾緊機構簡圖
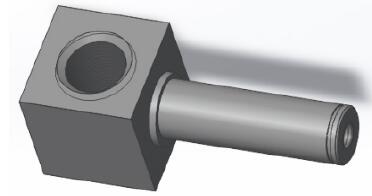
圖7 活節螺母簡圖

圖8 離合分度裝置筒
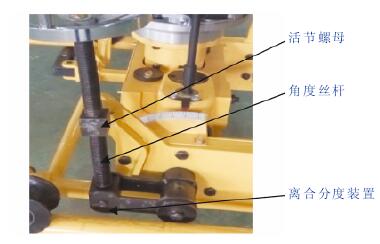
圖9 轉動絲桿筒圖
7.4 升降、傳動機構設計
升降機構的設計主要考慮了砂輪的利用率及砂輪角度擺動范圍。砂輪的有效使用高度≤55 mm,所以在設計升降機構時移動機構即移動箱體的移動距離確定為≤55 mm。設計升降絲桿升降螺母配合機構,升降螺母固定在移動箱體之上,通過轉動轉桿,帶動升降絲桿轉動,從而帶動與升降螺母配合的移動箱體的升降運動。由于砂輪、主軸、移動箱體、彈性離合器相對固定,所以升降絲桿的轉動就帶動了砂輪的轉動。
傳動機構的設計主要考慮以下幾點,傳動級別盡量少,功率損耗少等。將傳動機構設計成發動機主軸通過彈性離合器連接,帶動彈性離合器轉動,彈性離合器的轉動帶動主軸轉動,主軸帶動砂輪轉動,這樣的的直連方式滿足了傳動級別盡量少的原則,功率損耗少,工作扭矩損失小。
升降傳動機構如圖 10 所示的設計方式,減少了外形占用空間,機構配比緊湊,不易造成裝配及攜帶不便的結果,此種方式可取。
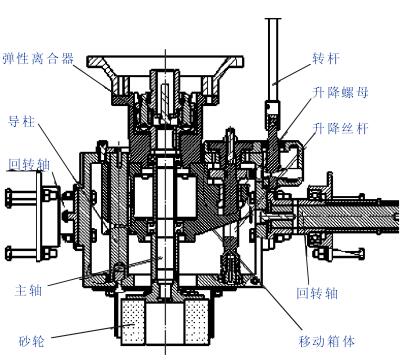
圖 10 升降、 傳動機構簡圖
8 、結束語
以上主要概述了鋼軌打磨機械國內外現狀,通過對國內現用鋼軌軌型的研究,提出了內燃道岔軌面精磨機的設計方案,通過對比分析,確定了設計原理,通過對走行機構、橫移機構、角度調整機構、升降傳動機構的設計分析,完成了內燃道岔軌面精磨機的研究。內燃道岔軌面精磨機解決了目前高鐵 (提速) 鐵路線路道岔軌頂面、正線軌頂面、尖軌非作用邊的打磨無打磨工具的問題,實用性強,操作便捷,是一款理想的精密打磨工具。
投稿箱:
如果您有機床行業、企業相關新聞稿件發表,或進行資訊合作,歡迎聯系本網編輯部, 郵箱:skjcsc@vip.sina.com
如果您有機床行業、企業相關新聞稿件發表,或進行資訊合作,歡迎聯系本網編輯部, 郵箱:skjcsc@vip.sina.com
更多相關信息