發動機深孔加工技術
2019-6-3 來源:轉載 作者:-
深孔加工向來是金屬切削加工難點,采用傳統工藝會造成槍鉆崩刃、折斷等問題。通過改進槍鉆結構形式——可轉位刀片+帶導條式高強度刀桿,采用帶斷屑槽刀片,使得排屑更順暢,徹底解決折斷及崩刃類異常,提升加工質量。
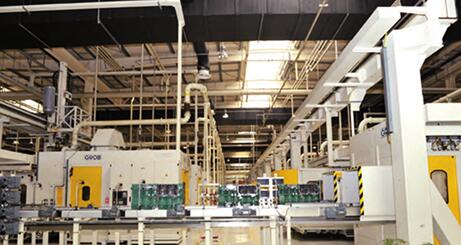
近年,我國東部某廠自主研發了一款油耗低、動力強、可靠性高的重型柴油機,深得用戶青睞,其氣缸體上有諸多用于冷卻水道或潤滑油道的深孔需要加工,其中底面φ26mm×275mm就是其中之一。為提升設備利用率,減少投資成本,在設計方案時放棄了傳統的專用機床方案,而采用德國進口GROB(格勞博)高速加工中心加工,但經常會出現可修磨槍鉆壽命低、斷刀率高等問題。
1. 加工條件
加工設備:德國GROB G700加工中心
槍鉆:單刃焊接槍鉆φ26mm×546mm
刀柄:GUHRING HSK100-A側固鎖緊
切削液:FUCHS水溶性乳化液ECOCOOL 68CF2W,乳化液濃度:8-10%
內冷流量壓力:75L/min,4MPa
切削參數:底面油孔,孔直徑26mm,孔深275mm,轉速1041r/min,線速度85m/min,進給量240mm/min,每齒進給量0.23mm
工藝要求如圖1所示。
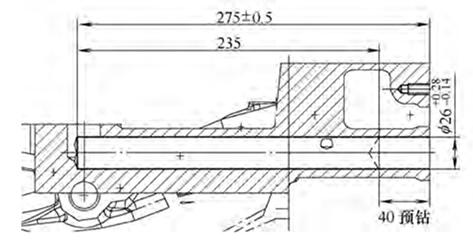
圖1 底面深油孔加工工藝要求
2. 實際使用中存在的問題
該生產線投入使用后,為保證此類深孔加工質量穩定性,槍鉆刀具為德國生產。但在實際使用中經常出現崩刃和斷刀(見圖2)等問題,造成刀具損耗和零件報廢。
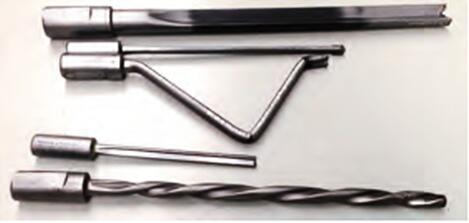
圖2 槍鉆斷刀
統計該工序近半年時間內刀具使用情況得知:累計使用該槍鉆230次,其中斷刀15次,斷刀率達到6.4%,刀具異常損耗達數萬元。此外,為了減少發動機自重,缸體采用精密薄壁鑄造工藝,實測該深油孔加工完后其厚度不足5mm,故在斷刀發生后,由于鐵屑和硬質合金刀頭擠壓,很容易造成孔壁破壞,從而造成整個氣缸體報廢,近半年造成工廢6件。
3. 原因分析
通過組織技術人員分析排查刀具壽命情況和異常斷刀狀態,同時通過機床自帶的主軸監控系統,分析其加工過程情況,進一步分析排查該深油孔加工斷刀原因,主要為:
(1)槍鉆刃口磨損嚴重。通過對換下的槍鉆進行觀察,發現槍鉆主切削刃、側刃和后刀面磨損情況比較嚴重,軸向磨損量超過2mm,增大了槍鉆鉆削過程中的切削阻力,增加斷刀風險。
槍鉆刀頭磨損嚴重,與槍鉆沒有涂層有很大關系,缺少涂層對刀頭硬質合金基體隔熱和潤滑保護,其磨損會急劇加快。而槍鉆由于刀頭和槍身需要焊接,加之兩種材料高溫變形量不同,決定了其無法在精磨后實施涂層工藝。
(2)排屑不暢。在對機床設備監控系統數據進行分析排查時發現,按照刀具布置圖要求機床內冷流量/壓力:75L/min、4MPa,但近半年出現多達20次以上的內冷高壓報警,伴隨該報警信息之后就會出現主軸負載報警以及斷刀的發生。
之后,進一步對機床主軸負載曲線分析,并比較正常加工和斷刀件的負載監控曲線后發現(見圖3),正常加工的工作主軸負載新刀的上下波動范圍35-55%,整個加工過程是一個線性均勻變化曲線,前后兩個工件間的波動幅度小于5%;而斷刀件負載監控圖形,則會在內冷堵塞的時候不斷升高,一般達到70%時,槍鉆刀頭焊接部位會扭斷,該過程中其負載上下波動范圍在45-70%,幅度達到25%;斷刀工件孔內的大量鐵屑也證實,排屑不暢,存在鐵屑堵塞現象是該槍鉆斷刀的主要原因之一。
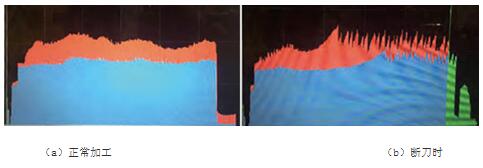
圖3 主軸負載監控圖形
4.優化改進方案
針對上述排查,刃口沒有涂層保護、加工過程中存在堵屑問題是兩個主要原因,確定后續改進優化方向和措施:
(1)提升排屑性能。通過增大內冷壓力或流量方式,提升排屑性能。
(2)增加刀具耐磨性。在刀具材質不能改善的情況下,實施涂層工藝。
(3)加強刀桿強度。采用強度等級更高的刀桿,提高槍鉆剛性,防止加工時刀桿斷裂。
(4)改善斷屑效果。優化切削刃口形式,改變鐵屑形狀,使其更利于排屑。
其中提升排屑性能方案,若提升內冷壓力至6MPa,需要更換螺桿泵,成本較高,故考慮通過改善刀具結構來提升排屑效果。
在和德國技術專家討論后,結合其實際應用案例,決定采用可轉位刀片+帶導條機夾式刀桿的刀具方案來進行刀具優化,具體結構如圖4所示。
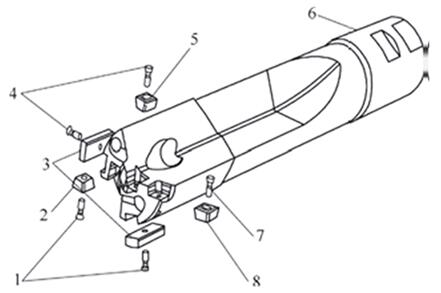
圖4 1、4、7-螺釘 2、5、8-轉位刀片 3-導條 6-刀桿
5.刀具試驗過程
在試驗刀具完成到位后,立即組織刀具試驗,在第一次按照原參數和壽命試驗,正常達到原強制換刀壽命后,為進一步挖掘刀具潛力,嘗試開展極限壽命試驗,從試驗結果來看,刀具壽命有一定程度提升。
新轉位刀具特點如下:
(1)刀桿采用高強度合金鋼代替普通鋼管精制而成,強度提升50%,刀桿成為可反復使用的耐用品。
(2)采用兩段30mm磨制高精度硬質合金導條,保持加工過程中刀具支撐和平衡,利用導條自導向后續加工,保證深孔具有較好的孔徑和直線度。
(3)采用3片帶有復合TiAlN涂層、斷屑槽可轉位刀片組成主切削刃,耐磨性更好,錯齒式布置,將26mm內鐵屑分為6段,相比原槍鉆的4段,鐵屑更短,加之刀片前有壓制斷屑槽,更有利于排屑。
具體刀具及切削部位如圖5所示。
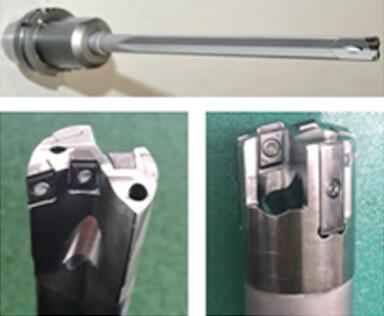
圖5 優化后轉位刀具及切削部位
6.持續改進
在試驗取得初步成功后,繼續對刀片存在微崩的異常情況進行分析、排查發現,該深孔在中間部位有一個φ10mm相貫孔和底部貫穿孔,加工至該部位時存在破孔和單邊切削沖擊,通過對NC程序優化,采取分段式進給。通過對使用后刀片觀察發現,刀片失效形式正常。
結語
新可轉位刀片式槍鉆,經過半年時間合計201次的換刀驗證,平均可加工孔數達到118,未出現過斷刀,杜絕了因斷刀問題造成的工件報廢。同時,可轉位刀片裝調方便快捷,省去修磨環節;加工節拍也由之前的69.5s降至59.5s,單臺刀具消耗成本節省約1.05元,提效降本明顯。
來源:《世界制造技術與裝備市場(WMEM)》
投稿箱:
如果您有機床行業、企業相關新聞稿件發表,或進行資訊合作,歡迎聯系本網編輯部, 郵箱:skjcsc@vip.sina.com
如果您有機床行業、企業相關新聞稿件發表,或進行資訊合作,歡迎聯系本網編輯部, 郵箱:skjcsc@vip.sina.com
更多相關信息