淺談槍鉆在不銹鋼材料深孔加工中的應用
2020-1-17 來源: 中國航發沈陽黎明航空發動機有限責任公司 作者:馬 瑛,孫長友,楊文輝,張懿霏,趙鳳來
摘 要:在我國的機械加工行業中,深孔的加工問題一直是一個非常嚴重的問題,鉆孔的質量好壞直接的影響了我國機械加工行業的工作質量以及工作效率,因此在我國的機械加工行業中,對于深孔的加工一直都非常的重視,同時深孔加工的質量也是我國機械加工行業的一項非常嚴峻的挑戰和難題。按照我國傳統形式上的鉆孔尤其是深孔的加工工藝來講,需要非常復雜并且費時的工藝流程和加工流程。例如在深孔加工的過程中鉆孔,擴孔以及鉸孔等多道加工工序在目前的深孔加工過程中非常的復雜,同時伴隨著加工質量低下并且不穩定以及生產效率低。通過使用槍鉆進行不銹鋼鉆削試驗,解決不銹鋼加工中存在的問題,同時對加工不銹鋼時的切削性能進行研究。針對深孔加工的過程文章進行詳細的論述以及分析,希望通過文章的闡述以及分析能夠有效的提升我國深孔加工的加工質量以及加工穩定性,同時也為我國機械行業的進一步提升以及發展貢獻一份微薄的力量。
關鍵詞:槍鉆;不銹鋼;切削性能
引言
不銹鋼材料在我國的機械加工行業中占有非常重要的位置,最主要的原因在于不銹鋼材料在機械加工過程中具有以下五個優點,首先是不銹鋼材料具有非常高的機械性能;其次是不銹鋼材料具有非常好的韌性;第三是不銹鋼材料具有非常好的塑性;再次是不銹鋼材料具有較高的耐腐蝕性能;最后是不銹鋼材料的綜合機械加工力學性能非常的好。
正是由于上述的優點,不銹鋼材料在我國的很多領域都有著非常廣泛的應用,并且取得了非常好的應用效果。在我國的機械行業,建筑行業,汽車行業,醫療行業以及航空航天行業中都有非常廣泛的應用。
雖然不銹鋼材料在應用的過程中非常的廣泛,但是由于不銹鋼材料的一些自身特殊性能導致了在材料加工制造的過程中會遇到非常多的難題,最顯著的一個問題就是在我國機械行業的深孔加工的過程中,不銹鋼材料會出現大量的纏刀,黏刀以及加工廢屑排出困難等種種加工問題。
正是由于這一點問題導致了我國目前的科研重點以及在加工過程中要重點關注不銹鋼材料的深孔加工問題,要盡量的避免不銹鋼材料在深孔加工的過程中出現上述的問題。因此我國逐漸的使用槍鉆來對不銹鋼材料進行深孔加工,槍鉆進行深孔加工是一種非常專業的加工工藝技術。
作為深孔加工中非常有效的加工工具,槍鉆的加工范圍非常的廣泛,能夠將塑性非常高的加工材料進行有效的深孔加工,玻璃纖維這種塑性非常高的材料在深孔加工的過程中使用的就是槍鉆的方式進行深孔加工,其次高強合金的深孔加工通常情況下也是用槍鉆的加工工藝進行加工。
槍鉆在深孔加工的過程中能夠加工的孔徑非常的廣泛,能夠從直徑 1.5 毫米的深孔加工到直徑 76.2毫米的深孔。不僅僅是深孔加工的直徑范圍較廣,深孔加工的深度也能夠達到深孔 直徑的一百倍左右,加工效果非常的顯著。
槍鉆加工深孔的過程中主要的優點有四個,首先是槍鉆進行深孔加工能夠進行有效的一次成孔加工,其次是槍鉆進行深孔加工具有非常好的加工精度;再次是槍鉆進行的深孔加工在加工后的孔壁較為光滑,最后是槍鉆深孔加工在加工過程中沒有加工毛刺的產生。需要注意的是在深孔加工的過程中,不同形式的鉆具在加工同一種加工材料的時候會出現不同形式的切削加工性能。
正是由于這樣的原因存在,我國的加工制造行業才會對槍鉆對加工深孔的切削性能進行深入的調查和研究,要對切削性能的變化有著非常好的研究混合分析。在分析研究槍鉆在進行不銹鋼材料的深孔加工的過程中我們主要是通過實驗的方式來進行研究分析。我們能夠通過實驗的方式針對不同形式的鉆具在不銹鋼材料深孔 加工過程中出現的不同的切削性能進行對比,找出性能最優良的槍鉆鉆具,找出最適合不銹鋼材料深孔加工的鉆具,通過這種形式來對實際的機械加工中的深孔加工進行指導和管理。
下面進行詳細的論述以及分析。
1 、槍鉆在深孔加工過程中的實驗研究分析
1.1 槍鉆在深孔加工中的優點分析
首先槍鉆在深孔加工過程中具有非常高的加工精度以及加工效率。由于槍鉆在深孔加工的過程中使用的一次性深孔成型的加工能夠一次性的達到預定深孔深度,這樣就能夠有
效的避免由于琢鉆導致的深孔表面的過差粗糙度,有效的保障了深孔加工的加工深度,加工光潔度以及加工直線度,最重要的是能夠有效的提升深孔加工的生產效率。其次是槍鉆在深孔加工過程中具有非常小的加工成本投入。
在我國機械行業中,傳統形式上的深孔加工我們第一個考慮的是鉆床的形式來進行深孔加工,在實際的深孔加工中也是應用深孔鉆床較多,這樣的深孔加工工藝不僅僅需要專業的深孔鉆床,還需要有專業并且有經驗的現場操作人員進行專業的操作。使用加工中心+槍鉆工藝,不但減少了資金投入且減少了操作人員數量,加工成本明顯降低。
1.2 槍鉆在深孔加工過程中的工藝試驗分析
首先在使用槍鉆進行深孔加工的過程中,由于加工的批量不是非常的大,因此在加工的過程中不需要進行針對性的進行導向套的設計,取而代之的是進行預鉆孔進行導向孔的加工,這樣也能夠有效的起到導向套的鉆孔輔助效果。在深孔加工的過程中,導向孔的直徑要比槍鉆的直徑大一點,一般是公差 0.01 到 0.02 之間。通常情況下加工的公差等級能夠達到H7,鉆孔的深度能夠達到鉆孔直徑的約 2.5 倍作用。
在深孔加工的過程中,導向孔的加工精度非常的關鍵和重要,只有導向孔的加工精度達到了加工要求,才能夠有效的實現后續深孔加工的加工精度。導向孔在深孔加工的過程中主要起到的作用是定心,如果在加工的過程中沒有定心鉆,我們就需要進行傳統形式的導向孔加工。
需要注意的是在實際的加工過程中由于導向孔不達標導致 的導向孔失去定心作用,鉆具折斷的情況經常出現,因此要格外的注意。其次是 將槍鉆放入導向孔內時,槍鉆不能夠在導向孔外部進行選裝槍鉆。鉆孔操作完成后,要實現快速退鉆。
最后是在進行槍鉆深孔加工的時候孔深度前進 5 毫米,槍鉆的主軸旋轉速度要下降一半的速度,同時給進速度也要下降一半。主軸停止旋轉的時候,冷卻液也要停止供給
。
下表為槍鉆深孔加工試驗的具體試驗結果。
深孔孔徑為 4mm,孔深為 110mm。
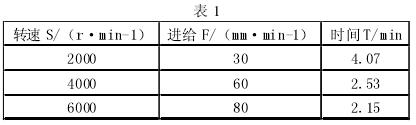
根據上述表格中的實驗數據我們可以得出,實驗過程中得出的鉆孔相關數據同專業刀具生產公司提供的技術資料相比較明顯的顯小,這樣的數據結果主要是由于在實際的生產加工中出于保障深孔加工質量以及保障加工刀具的安全造成的,因此實驗 得出的鉆孔數據相較于理想的數據相對來講較為保守。不同型號規格在鉆孔加工過程中得出的較為可靠的鉆孔加工數據。僅供參考。
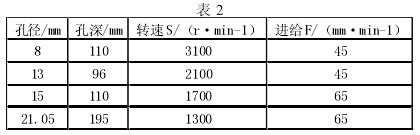
2 、槍鉆在進行深孔加工的時候需要注意的主要事項
首先,槍鉆進入引導孔前必須低速運轉。因所用槍鉆是焊接硬質合金頭形式,在槍鉆進入引導孔前,若全速運轉,會導致槍鉆甩彎或折斷。其次,在冷卻壓力和流量不足時,應適當降低切削參數,以防止由于切削液不足,造成擠屑或冷卻不好,影響加工質量,甚至槍鉆折斷。再次,加工通孔出口為斜面或有交叉孔時,鉆通前或相貫前 1mm 時,降低進給率至原來的 40%。最后,槍鉆切削工件時一定要打開切削液,避免因無切削液而使槍鉆排屑不暢或切削溫度升高過快,導致槍鉆擠塞,甚至折斷。
3 、在深孔加工的過程中槍鉆受到的切削刃損傷分析
3.1 在深孔加工的過程中由于不充分的冷卻液供給容易出現槍鉆切削刃的損傷
槍鉆屬于高速切削刀具,雖然由于刃少每轉進給量較低,但其轉速很高。由于切屑能從被加工孔中排出,無需在鉆削過程中定期退刀來排出切屑,所以加工效率得到極大的提高。但是,如果工作時冷卻液供應不充分,會使切屑堆積在排屑槽中無法排出,這些受擠壓的切屑將對槍鉆旋轉形成阻礙,當槍鉆承受的扭矩過大時,將導致刀頭與刀桿分離,槍鉆整體報廢。
3.2 在深孔加工的過程中不配套的鉆套配置容易出現槍
鉆切削刃的損傷鉆套在槍鉆進行孔加工時具有導向作用。當鉆套和鉆頭的旋轉軸線之間的不同軸度過大時,槍鉆鉆尖會因無法固定而造成撞擊,脆弱的硬質合金刀尖不能承受由不同心引起的彎曲應力而造成刀片碎裂。雖然適當增加刀具長度可以改善這種情況,但長度過長會造成刀桿顫動,而導致疲勞失效。
投稿箱:
如果您有機床行業、企業相關新聞稿件發表,或進行資訊合作,歡迎聯系本網編輯部, 郵箱:skjcsc@vip.sina.com
如果您有機床行業、企業相關新聞稿件發表,或進行資訊合作,歡迎聯系本網編輯部, 郵箱:skjcsc@vip.sina.com