TC4 鈦合金深孔鉆削試驗研究與機理分析
2020-6-12 來源: 上海海交通大學 上海航天精密機械 作者:陳杰 胡蒙 郭國強 孫程成 明偉偉 等
摘要 :TC4 鈦合金深孔鉆削過程中鉆削溫度高、排屑路徑長,加劇刀具磨損,影響深孔加工質量和精度。為制定可用于實際生產的鈦合金深孔鉆削加工參數,開展 TC4 鈦合金深孔槍鉆加工試驗。試驗結果表明,鉆削溫度受鉆削速度影響較大,進給量的影響不顯著;孔徑和圓度隨著鉆削速度的增加而增大,同軸度隨著切削速度增加而先增大后減小;孔的表面粗糙度隨著鉆削參數的增加而增大,且大參數下深孔表面質量進一步惡化;各組試驗加工硬化層在30μm 左右,且隨著鉆削速度增加,切屑擠壓變形嚴重。綜合分析后制定的干切削條件下 TC4 鈦合金深孔槍鉆的鉆削速度為 20m/min,進給量為 0.08mm/r。
關鍵詞: 槍鉆;深孔;鉆削機理;加工質量;TC4 鈦合金
鈦合金比強度高、比剛度高、耐腐蝕、抗疲勞性能好,能在超低溫和超高溫、高應力、強腐蝕環境下穩定工作,廣泛應用于航空航天領域[1]。在航空、航天器中的儀器儀表、傳感器、舵骨架、航空發動機等部件制造過程中,常要求加工高精度和高質量的復雜深孔結構[2-3]。深孔長徑比大,加工時處于封閉或半封閉狀態,刀具切削情況無法直接觀察,難以準確監控刀具狀態;排屑路徑長且不易排出,易造成已加工表面劃傷及刀具崩刃;切削散熱困難,熱量累積產生高溫;加工工藝系統剛性差,易產生振動[4]。因此與普通孔相比,深孔加工難度大。目前國內外一些學者進行了相關研究。
Zhang 等[5]研究了鑄鐵深孔加工表面質量、亞表層變形與加工條件之間的關系,以及 BTA 深孔鉆削機理,提出鉆削參數和鉆削機理共同決定表面完整性。Zhang等[6]通過試驗和有限元仿真,提出了鉻鎳鐵合金槍鉆過程中槍鉆鉆尖偏移不一致對深孔直線度偏差影響的理論原因。Kuzu 等[7]利用有限元和反傳熱法建立了微量潤滑條件下的蠕墨鑄鐵深孔鉆削熱模型,并通過試驗驗
證了模型的可靠性。
槍鉆是一種單刃切削自導向外排屑深孔鉆頭[8]。深孔加工時高壓冷卻液通過鉆桿 V 形通道液體將熱量帶走,并利用冷卻液壓力排屑,且在鉆頭外徑安裝有導向條,從而保證刀具的正確導向[9]。槍鉆系統有效提高深孔鉆削的斷屑排屑性能、冷卻潤滑效果、制孔精度和質量,廣泛應用于小直徑孔加工[10-11]。由于 TC4 鈦合金彈性模量和熱導率較低,鉆削過程產生大量的熱[12],且深孔鉆削的封閉環境限制熱量散發,導致鉆削溫度隨鉆削深度的增加持續增大。過高的溫度會加速刀具磨損,降低孔加工精度,產生加工變質層,生成殘余應力。因此需要了解 TC4 鈦合金槍鉆過程中加工參數對鉆削溫度的影響規律和加工機理,為工藝參數制定提供可靠依據。
因此,為制定滿足精度和質量要求的 TC4 鈦合金深孔加工工藝,開展了 TC4 鈦合金深孔槍鉆試驗,研究鈦合金深孔鉆削成屑機理,分析鉆削速度和進給量對鉆削溫度、深孔尺寸精度和表面質量的影響規律,綜合分析之后給出一組應用于實際生產過程的加工參數。
1、槍鉆深孔鉆削試驗
1.1 工件材料與刀具
試驗采用鍛 TC4 鈦合金,工件尺寸為500mm×200mm×30mm,材 料 常 溫 下 的 抗 拉 強 度為 1000MPa,400℃下的抗拉強度為 550MPa,硬度為360HV,彈性模量為 120GPa。圖 1 所示為 TC4 鈦合金的金相組織和元素成分。其中白色的為密排六方結構的 α 相,黑色的為體心立方結構的 β 相。
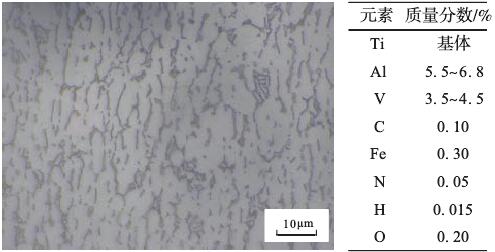
圖1 TC4鈦合金的金相組織和元素成分
使用德國鈷領公司的 EB80-5641 型槍鉆。槍鉆的刀尖材料為硬質合金,涂層為 CVD-TiCN,刀桿材料為高速鋼,刀桿和刀尖之間采用焊接連接。槍鉆直徑為7mm,鉆尖長度為 48mm,鉆尖加刀桿長度為 370mm,最深可加工長徑比為 40 的深孔。鉆尖幾何參數如表 1 所示。為了減小深孔鉆削時的軸向跳動,提高加工系統的剛度,在加工深孔之前先加工引導孔。使用山特維克可樂滿公司的 R846-0700-30-A1A 1220 型硬質合金麻花鉆加工引導孔,涂層為 PVD-(Ti, Al)N,直徑為 7mm,頂尖角為 140°。
1.2 試驗設備
試驗在 HAAS 公司的 EC-1600 臥式加工中心上進行。該機床工作臺范圍為 1626mm×1270mm×813mm;最大轉速為 6000r/min;定位精度為 0.01mm。深孔加工過程中溫度對刀具的影響至關重要。
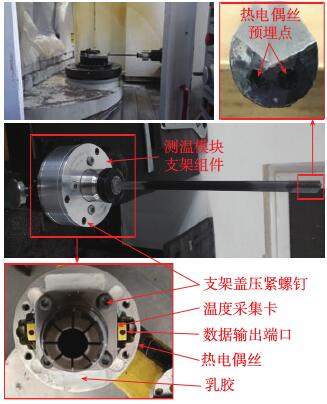
圖2 槍鉆試驗裝置及在線測溫系統
表1 鉆尖幾何參數
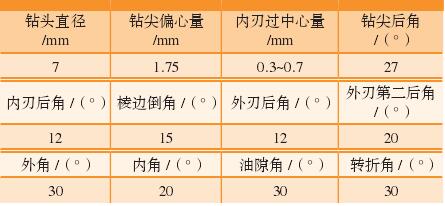
本次試驗采用槍鉆內冷孔埋熱電偶絲的方式在線測量深孔鉆削過程中的溫度。在線測溫系統如圖 2 所示,包括測溫模塊支架組件和溫度監測系統。測溫模塊支架組件設置于鉆削刀柄上,溫度監測系統 ( 包含溫度采集卡 ) 安裝在該測溫模塊支架組件之中。熱電偶絲線連接到測溫模塊支架組件中的采集系統,溫度采集卡對溫度進行實時監測,試驗結束后,打開支架組件,通過數據線將采集系統中的數據傳輸到計算機中完成數據的輸出與可視化。深孔鉆削過程中共有兩個熱電偶絲同時采集溫度信號,保證結果的準確性和可重復性。測溫模塊支架組件的結構 ( 包括溫度采集卡、支架蓋壓緊螺釘等 ) 呈對稱分布,且整體采用高強度鋁合金材料制作,以盡可能減小偏心質量。在線測量系統搭建完成后,進行動平衡測試,根據試驗結果通過增減某一位置的乳膠來平衡微小的偏心,以保證鉆頭高速旋轉時的動平衡。
1.3 試驗方案
在加工深孔之前先加工引導孔,引導孔直徑為7mm,鉆削深度為 10mm,轉速為 1800r/min,進給量為0.08mm/r。
表2 槍鉆試驗參數
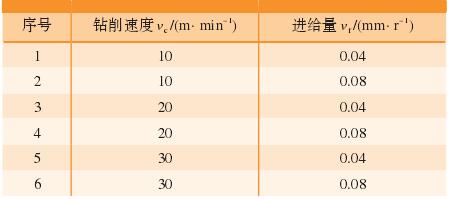
槍鉆深孔鉆削試驗采用全因素試驗,鉆削參數如表 2 所示。鉆削深度為 94mm,為 12 倍徑。由于槍鉆內冷孔預埋熱電偶絲,無法進行內冷,因此采用壓力為20bar 的外冷。試驗過程中,對槍鉆鉆尖的鉆削溫度進行實時測量。試驗結束后,采用航天精密機械研究所的C10TA0101DH/TP 型三坐標儀檢測孔的加工精度。之后將深孔剖開,在距孔口 30mm、60mm 和 90mm 3 處進行制樣,對孔的表面加工質量進行分析。并對已加工表面和切屑進行金相分析和掃描電鏡分析。
2 、試驗結果分析
2.1 槍鉆深孔鉆削溫度
如圖 3 所示,在各組參數下,鉆尖溫度隨著鉆孔深度的增加都逐漸上升。隨著鉆削速度增加,鉆尖溫度顯著上升。鉆削速度的提高導致材料的去除率提高,而鉆削速度的提高又使鉆削力減少,鉆削過程中產生的能量大量轉移到鉆削熱上,從而使鉆尖溫度顯著上升。鈦合金加工過程中,刀具溫度過高會降低刀具的強度,加快刀具的磨損,特別是在深孔加工中,過高的溫度很容易導致刀具的失效。為保證硬質合金刀具的耐用度,應當將鉆削速度控制在 20m/min 以下。同時,隨著進給量的增加,鉆尖溫度略有上升,但不顯著。因此,在實際鉆削過程中,可以采取低鉆削速度,高進給量的方式提高鉆削效率。
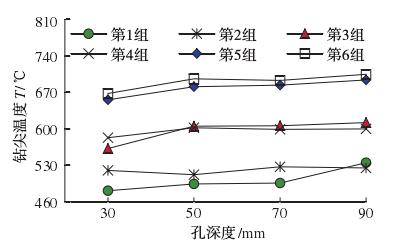
圖3 鉆尖溫度變化圖
2.2 深孔加工精度
深孔直徑是工藝過程最需要控制的指標,影響到軸孔之間的配合。使用三坐標測量儀分別測量距孔口30mm、50mm、70mm 和 90mm 位置處的直徑。如圖 4所示,所有孔徑都偏大,這是由于深孔加工剛性較弱,槍鉆徑向跳動引起的。在同一個孔內,深孔直徑呈現出先增大后減小的趨勢,深孔加工過程中的整體剛性隨著鉆削深度加深而逐漸增大,因此孔徑有一定的減少,但區別不大。從圖 4 中數據可以看出,隨著鉆削速度的增大,孔徑有明顯的增大的趨勢,這與加工溫度有關,溫度的升高導致鉆尖強度降低,跳動增大。而進給量的變化對孔徑的影響不大。圖 4 還給出了各組參數下的深孔圓度變化規律。孔的圓度隨孔深度的增加而增加。隨著鉆削速度的增加,孔的圓度相應增加,進給量對圓度影響不大,但在 20m/min 的鉆削速度下,0.08mm/r 的進給比 0.04mm/r 產生的圓度更大。
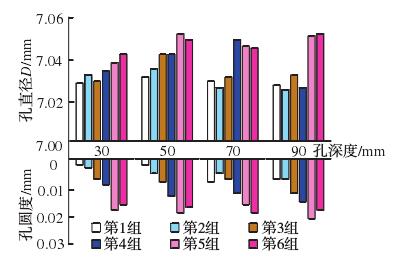
圖4 深孔直徑和圓度變化規律圖
圖 5 為各組參數下深孔同軸度 ( 以引導孔為基準 )的變化規律。各組試驗的同軸度均處于 0.01~0.02mm之間。加工參數對同軸度的影響并不明顯,但參數增大,同軸度還是有一定程度的升高。第 3 組試驗的同軸度結果最為理想。因此,從加工精度分析,鉆削速度為20m/min 下的試驗結果較為理想。
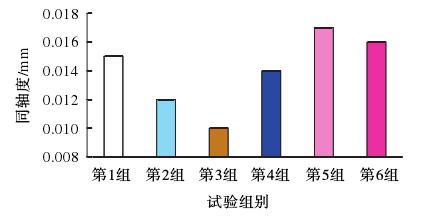
圖5 深孔同軸度變化規律圖
2.3 深孔加工表面質量
圖 6 所示為各組試驗的粗糙度變化規律圖。前 3組試驗粗糙度都比較小,處于 0.4~0.5μm 之間。后 3 組試驗由于加工參數的增大,粗糙度明顯增加,這與加工過程中刀具的狀態有著密切的聯系。從圖 3 中可以看出,后 3 組數據刀尖溫度較高,較高的溫度影響刀具的韌性,加劇刀具的磨損,因此加工后的粗糙度越來越大。同一個孔內,粗糙度也越來越大,這是由于槍鉆深孔加工時排屑不暢,切屑沒有及時排出,會對加工表面有劃傷和破壞,從而導致粗糙度的增大。
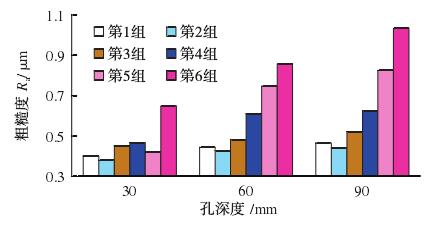
圖6 深孔粗糙度變化規律
圖 7 是第 2 組試驗在孔深 30mm 和 90mm 處的掃描電鏡(放大 200 倍)和能譜分析圖。孔深 30mm 處,加工表面較為平整,無明顯的缺陷。孔深 90mm 處,加工表面存在一些粘結物和切屑的劃痕。對黏結物 A 點進行能譜分析,檢測出 Ti、Al、V 元素和少量的 O 元素。從能譜分析可以看出切削過程中有少量的鈦合金黏結在已加工表面,并有一定程度的氧化,這說明在加工到90mm 處時,刀尖的溫度已經非常高,達到鈦合金氧化的條件。加工表面幾處切屑的劃痕也說明,當加工深度較大時,槍鉆的排屑不夠流暢,未能及時排出的切屑對已加工表面形成了一定的劃傷。可見,隨著深孔加工深度的增加,切削溫度升高,加工難度增加,加工表面質量也逐漸惡化。
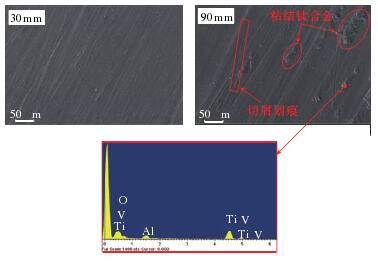
圖7 第2組試驗已加工表面形貌及能譜分析
2.4 深孔加工表面硬化
圖 8 所示為第 1 組和第 6 組試驗在孔深 90mm 處的金相圖。兩組加工表面的晶粒都發生沿鉆削進給方向的扭曲延伸,造成加工硬化。表明鈦合金深孔鉆削表面塑性變形非常明顯。第 6 組的孔加工表面還有 1 層厚度為 5μm 左右的白色相變層。說明該組鉆削參數下的鉆削溫度達到了鈦合金的相變溫度,α 相已經轉變為 β 相。
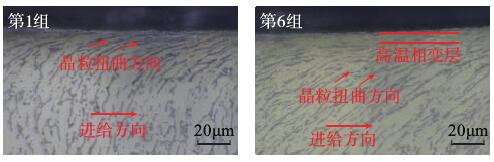
圖8 孔深90mm處金相組織
在孔深 90mm 處,距離已加工表面 5μm、15μm、25μm、35μm、50μm、70μm 處檢測硬度。圖 9 為各組試驗距離已加工表面不同距離的硬度變化曲線。其中未加工工件硬度為 360HV。可以看出每組試驗條件下的深孔表面都有不同程度的加工硬化。隨著鉆削速度的提高,加工硬化更明顯。由于第 5 組和第 6 組的試驗參數大,鉆削溫度高,深孔已加工表面的晶粒扭曲延伸最顯著,所以加工硬化最嚴重。從圖 8 第 6 組孔深90mm 處的金相組織可以看出,第 6 組試驗參數下的深孔已加工表面發生相變,產生的 β 相的硬度比 α 相小,所以在距離加工表面 5μm 處,第 6 組試驗參數下的表面硬度反而略低。曲線圖表明,各組試驗在孔深 90mm處的表面硬化層厚度為 30μm 左右,超過 30μm 后硬度趨于工件材料原本的硬度值。

圖9 各組試驗加工硬化曲線
2.5 深孔加工切屑形態
圖 10 為進給量 0.04mm/r 時不同鉆削速度下的切屑形態。隨著鉆削速度增加,切屑由長螺旋卷曲狀變化為短帶狀,且切屑中擠壓部分越來越多,材料的去除由剪切轉換為擠壓,并且在 30m/min 下,切屑由崩碎狀排出。在鉆削速度較低時,容易形成螺旋卷曲狀切屑,屑系數大,隨著鉆削速度提高,切屑轉變為短帶狀和錐狀切屑,當速度進一步提高時,切屑斷裂容易,形成崩碎狀切屑,同時也說明在加工過程中刀具沖擊頻率高,刀尖發生嚴重的磨損,影響加工過程的穩定性。
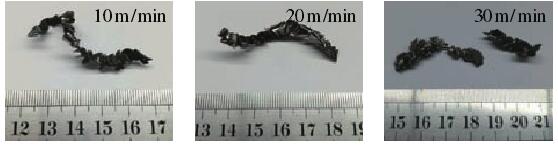
圖10 不同切削速度下的切屑形態(進給量為0.04mm/r)
圖 11 為第 6 組試驗沿厚度方向的切屑金相圖。由于熱軟化作用超過應變硬化,形成絕熱剪切帶,進而形成鋸齒狀切屑。圖中絕熱剪切帶從鋸齒的齒谷一直延伸到切屑和刀具接觸面。在與刀具接觸面表層,可以看到晶粒有一定程度的扭曲,圖中標出了扭曲方向,即切屑流動方向,說明切削區溫度較高,導致晶粒扭曲,發生塑性流動滑移,最終形成了加工硬化。
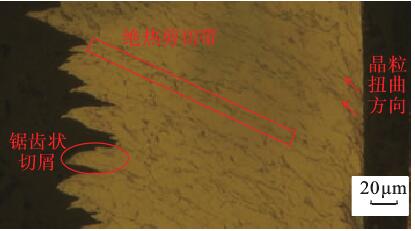
圖11 第6組試驗切屑金相
圖 12 所示為第 6 組試驗切屑的微觀形貌圖。因為高溫、高應變率下切屑受到刀具和工件的嚴重擠壓,所以切屑沒有卷曲規律,擠壓嚴重,卷曲半徑極小。將局部區域放大 200 倍后,能清楚看到在切屑的自由面有溝壑狀的鋸齒,這也與圖 11 相對應。
圖12 第6組試驗切屑微觀形貌圖
通過 TC4 深孔鉆削機理分析,當鉆削速度為 20m/min 時,加工表面硬化在可接受范圍,切屑擠壓變形程度適中,在排屑過程中對已加工表面損傷小,適合深孔鉆削加工。進給量對鉆削溫度的影響較小,比較不同進給量對應的深孔加工精度,兼顧加工效率,在滿足設計要求的前提下,選擇進給量為 0.08mm/r。
3 、 結論
本文通過 TC4 鈦合金深孔槍鉆全因素試驗,研究了鈦合金深孔鉆削成屑機理,分析鉆削速度和進給量對鉆削溫度和深孔質量的影響規律。試驗結果表明:
(1)鉆削速度對 TC4 鈦合金深孔鉆削溫度影響較大,對進給量的影響不明顯。
(2)孔直徑隨著鉆削深度的增加而先增大后減小,隨著鉆削速度的增加而增大。
(3)孔的表面粗糙度隨著鉆削速度和進給量的增加而增大,在大鉆削參數條件下,深孔已加工表面有鈦合金黏結物且有切屑劃傷痕跡。
(4)每組試驗都存在不同程度的加工硬化,加工硬化層厚度在 30μm 左右。
(5)隨著鉆削參數的增加,切屑擠壓變形趨于嚴重。
綜合分析試驗結果,在干切削條件下,鉆削速度為20m/min、進給量為 0.08mm/r 的深孔質量最優,滿足實際加工需求。
投稿箱:
如果您有機床行業、企業相關新聞稿件發表,或進行資訊合作,歡迎聯系本網編輯部, 郵箱:skjcsc@vip.sina.com
如果您有機床行業、企業相關新聞稿件發表,或進行資訊合作,歡迎聯系本網編輯部, 郵箱:skjcsc@vip.sina.com