典型車鉤體數控加工工藝研究
2022-4-2 來源: 常州中車鐵馬科技實業有限公司 作者:袁禮彬
摘要:針對動車組車鉤體加工過程中的工藝難點,從數控加工程序編制、專用成形刀具設計、深孔鉆技術應用等方面,提出了三個關鍵的工藝舉措,為提升實物質量和制造效率提供了完善的技術保證。
關鍵詞:數控程序 形成刀具 深孔鉆
引言
鉤緩裝置是動車組車輛中最基本的部件之一,其安裝于動車組車輛車體的兩端處,起到連接車輛、緩沖車輛的縱向力、提高列車舒適性的作用[1]。從制造工藝實踐角度來看,鉤體(如圖 1)加工的核心問題是如何確保鉤體凸錐、凹腔、連掛面、連掛組成鉤舌及主軸安裝部位、主風管組成安裝部位、電器連接器安裝部位、氣動解鉤組成安裝部位及鉤尾連接卡環處的尺寸精度、位置精度,以便使動車組可以長期穩定地完成連掛、通風制動、信號傳遞及解鉤等功能。
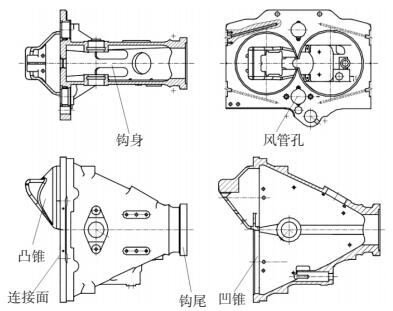
圖 1 典型車鉤體簡圖
本文作者在總結實踐的基礎上,對鉤體數控加工三個關鍵瓶頸工藝進行了探索,來實現鉤體加工過程的優化。
1、鉤舌盤圓柱銷安裝孔加工專用反刮刀及數控程序
為滿足臥加適應鉤體鉤舌盤圓柱銷孔兩內側面(如圖 2)的加工要求,設計并制作了專用反刮刀具[2]。反刮刀具體結構設計如圖 3 所示,該反刮刀主要由刀本體、刮刀片、鎖緊螺釘組成。其主要特性是刀本體的尾側是側壓直柄,刀本體中段為聯接軸,在聯接桿的頭部設置與其垂直的刀片座,刀柄、聯接軸、刀片座構成一體化聯接,反刮刀片由鎖緊螺釘裝配于刀片座。反刮刀片選擇住友公司制造的特制菱形刀片,此刀片具備優良的抗震效果,能連續承受切削過程中的抗崩性。聯接軸由不同軸圓形體組建,其外形與橢圓相似。該專用刀具前部直徑尺寸為 48 mm,聯接軸直徑為 45 mm,兩部分徑向尺寸都不大于所需通過的鉤舌盤圓柱銷孔直徑 Φ50 mm,從結構設計上保證了當該反刮刀具對鉤舌盤圓柱孔兩內側面切削時,刀具徑向尺寸大于所要切削部位的長度,而該反刮刀在進刀或退刀時避免與內孔表面干涉,同時最大限度地提升刀軸的剛性。
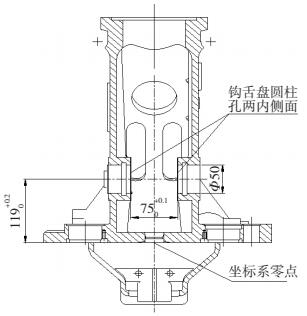
圖 2 鉤舌盤圓柱銷安裝孔簡圖
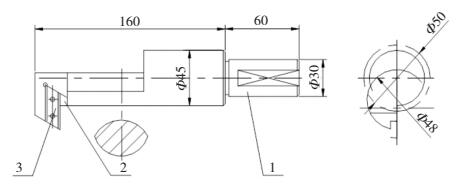
1—刀本體;2—聯接軸;3—反刮刀片;4—刀片座;5—鎖緊螺釘
圖 3 反刮刀具結構簡圖(單位:mm)
加工時,首先按制造規程要求鉆出通孔 Φ50mm,臥加按數控程序自動更換反刮刀具,機床主軸定向,反刮刀中心按照對應于 Φ50 mm 軸線坐標(-119,0)定位(如下頁圖 4-1),依事前準備的加工程序,在確保反刮刀各部位與通孔不發生干涉的條件下,以G00 設定速度通過 Φ50mm孔(見下頁圖 4-2),同時使反刮刀刀頭在同一水平方向偏移 25 mm,使反刮刀軸線與圓柱銷孔中心重合(如圖 4-3),反刮刀在按程序設定的加工條件以反方向工進的方式對內側面反刮切削(如圖 4-4)。反刮動作完成后,按與前面相反的方向路徑退出,到此,單側孔的內側面的切削循環動作完成。另一側圓柱銷通孔內側面的切削過程與此完全相同。
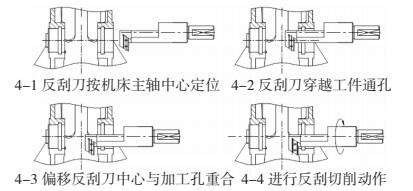
圖 4 專用反刮刀加工圓柱銷安裝孔
制定切削程序時,以鉤體圖上聯接面與鉤體中心軸線的交匯處為零點設定工作坐標系,使用絕對值方式設定程序,則圓柱孔兩內側面反刮程序如下:G91G30Y0Z0(回機床參考點,同時做好換刀準備);
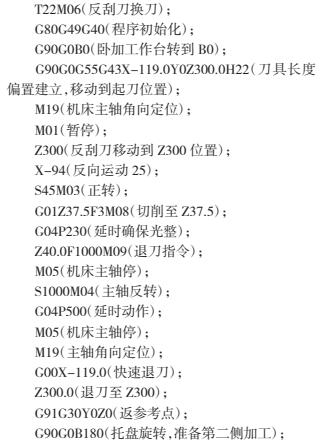
反刮刀的成功設計,較好地攻克了數控機床通用刀具難以解決的反刮難題,實現了在臥加上車鉤體通孔內側面反刮切削數控加工。實際表明,這種反刮刀較好地適應內端面加工,相比于數控機床常規的反刮工藝,明顯地提升了制造質量和切削效率,有著較強的可靠性和使用性。
2、鉤體鉤尾內凹槽成形面銑削加工
鉤體鉤尾的作用是用于連接牽引桿或壓潰管,是車鉤模塊化結構設計的重要特征。鑒于鉤尾外表面內凹槽的結構特征(如圖 5),傳統的加工方法是采用立式數控車床車削加工,但考慮到公司缺少相應的加工設備,采用發外加工手段,一則加長工藝流程,二則影響影響生產效率。經過對比分析,考慮在臥式加工中心上采用成形刀具進行加工。
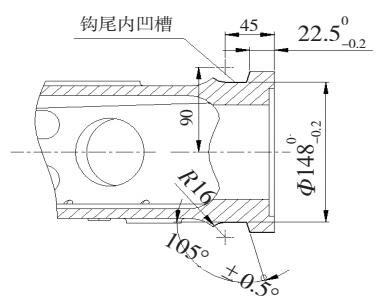
圖 5 鉤體鉤尾內凹槽外形(單位:mm)
針對鉤尾內凹槽的結構特征,技術人員設計了相應的專用焊接式成形銑刀,一方面考慮凹槽尺寸較大,粗加工采用一種成形銑刀,會增加切削阻力,引起刀具振動,減少銑刀使用壽命,因此把凹槽的粗加工分成兩個部位,并設計二種形狀的成形銑刀(如圖 6 和圖 7)。凹槽的精銑則采用一把整體形成銑刀(如圖 8)粗銑后留有合適的加工余量,一次成形銑削,加工效率,表面質量高。
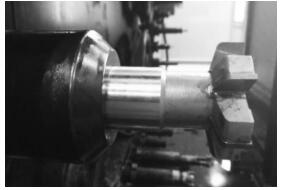
圖 6 加工凹槽右段粗銑刀

圖 7 加工凹槽左端粗銑刀
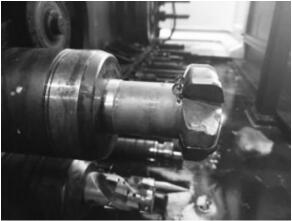
圖 8 加工凹槽精銑刀
采用成形銑刀進行凹槽機加工,有兩個優點,即實用性強,和鉤體連接面在一次安裝中加工,無需再設計專用立車夾具,在臥式加工中心上采用銑削加工,簡化夾具,加工成本低;能確保鉤體的切削精度和表面粗糙度,使用該切削方法,在銑削加工過程中切削量在刀具中部處最大,刀具兩端處最小,這種切削量分布特性使得切削力主要匯集在刀具切削刃中間部位,刀具所承受切削扭矩會相對減弱,因此銑削過程會相對平穩。整個銑切過程最后采用整硬刀具,也有效地減少因零件二次粗切削部位之間對接誤差,提升零件切削精度和表面粗糙度。
3、鉤體加熱帶深孔加工
鉤體加熱帶孔孔徑 Φ6.5 mm,孔深 173 mm,長徑比為 26,屬于典型的深孔特征(如圖 9),必須研究如何解決并滿足圖樣設計的質量要求和提升制造效率。按照傳統的工藝方法一般選擇深孔鉆機床進行加工,考慮到公司內部缺少深孔機床,因此考慮探索在臥式加工中心進行深孔加工[3]。這就要求技術人員研究如何從刀具著手解決該深孔加工技術難題。經過調研對比,多次驗證,選擇德國鈷領公司生產的槍鉆(如圖 10)。
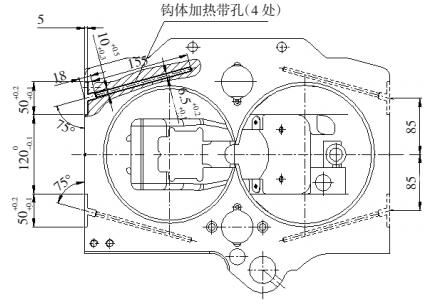
圖 9 鉤體前端面深孔尺寸分布
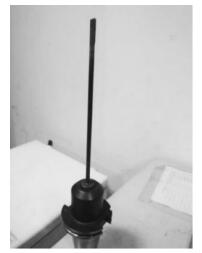
圖 10 槍鉆實物
本公司臥加的是日本森精機公司制造,型號為FH8000,因深孔加工的考慮,特地增大中心出水水泵,以保證加工壓力,借助于臥式加工中心的回轉工作臺的分度功能,一次裝夾,能加工 4 個方向的深孔。具體加工過程如下:
1)深孔引導孔的加工:鉆頭選擇頂角 140°的精密鉆頭,以保證引導孔頂角比槍鉆頂角大。引導孔加工深度設定為 20 mm,其鉆頭直徑比槍鉆大0.02~0.05 mm。
2) 槍鉆切削參數的選擇:槍鉆首先以轉速為120 r/min,進給速度為 220 mm/min,以低轉速快進給地進入引導孔,進入引導孔 2/3 處后,打開切削液并提高切削速度到正常值,經過工藝人員現場多次試加工驗證,比較適宜的切削參數是轉速為 3 000r/min,進給速度為 230 mm/min,一次性加工至預定深度可不退刀。
3)加工達到圖樣要求的深度后,關閉冷卻液,降低轉速并快速退出槍鉆至孔口。
在數控加工中心上使用槍鉆進行深孔加工,能有效保證鉤體深孔的尺寸精度及表面粗糙度;選用合適槍鉆可大大提高機床主軸轉速及刀具進刀速率;同時槍鉆加工過程中刀具排屑更加順暢,槍鉆頭部冷卻更充分,充分延長了刀具使用壽命,因而使深孔加工取得較高的加工效率。
4、結論
車鉤體結構特點決定了其加工難度,在整個加工過程中,我們重點解決了以下幾個難點:
1)臥加專用反刮刀具的設計,順利地解決了數控機床普通刀具無法無法完成的反刮加工難題,實現了在臥加上車鉤體通孔內側面反刮切削數控加工;
2)采用成形銑刀進行凹槽機加工,解決了和鉤體連接面在一次安裝中加工,無需立車加工,簡化了加工流程,提高了生產效率;
3)探索了在臥式加工中心進行深孔加工的工藝,為同類產品提供了有益的借鑒。
投稿箱:
如果您有機床行業、企業相關新聞稿件發表,或進行資訊合作,歡迎聯系本網編輯部, 郵箱:skjcsc@vip.sina.com
如果您有機床行業、企業相關新聞稿件發表,或進行資訊合作,歡迎聯系本網編輯部, 郵箱:skjcsc@vip.sina.com