數控車削加工中的實用對刀方法探討
2021-8-6 來源:四川新川航空儀器有限責任公司 作者:龍偉,唐毅
摘要:對刀方法在數控車削加工工作中發揮著重要作用,操作人員需要根據零部件特點選擇適宜的對刀方法,通過適宜的對刀方法確定工件坐標系,確保刀具刀尖的協調統一,進而提高數控車削加工質量與效率。基于此,文章簡要概述了數控車削加工工藝中的實用對刀方法及基本原理,并就數控車削加工工藝常用的試切法、對刀儀法及 ATC 對刀法等實用方法進行了概述分析,以期為數控車削加工工作的順利開展夯實基礎。
關鍵詞:數控車削;零件加工;對刀方法;操作原理
利用數控車削加工工藝制作零部件時,需要針對零部件特點及類別選擇適宜的對刀方法,以此確保車削加工工藝中的刀具刀尖朝向一致。為了提高數控車削加工工序精準性,需要確保刀具刀尖運行軌跡嚴格依照坐標程序執行。這里提到的坐標程序需要依照零部件尺寸確定橫縱坐標系,用于明確工件、機床二者位置的分析方法指的就是對刀方法。對刀操作對于數控車削加工工藝而言是確定坐標體系的主要步驟之一,也是確保數控編程系統與數控原點保持一致性的重要操作。在進行對刀操作工藝的時候,操作者需要將對刀指令傳輸至數控車床,以此確保數控車削操作嚴格依照編制程序執行。對刀作為數控車削加工工藝的重要實用技能,對刀方式的精準與否直接關乎著零部件加工
質量與效率。
1、數控車削加工中的實用對刀方法及其原理
1.1 對刀方法概述
對刀方法就是測量計算程序與數控機床間的原點距離,結合實際情況設置好程序原點后,調控刀具刀尖沿著設定坐標系依照程序流程作業。簡言之,就是在明確刀具刀尖起始坐標的前提下依照零部件尺寸特點搭建零部件坐標系、設定位置補償量,以此明確制作零部件與數控機床間的相對關系。在利用對刀方法進行數控車削加工工藝時,需要依照零部件加工原點設定坐標系,隨后綜合考量刀具尺寸對于數控車削加工的諸多影響,以此為基礎錄入刀具補償量,提高數控車削加工工藝質量。
1.2 對刀基本原理
在利用數控車削工藝進行零部件批量生產制造時需要將數控編程與車床加工分開管理,因此在進行程序編訂時需要依照設計圖紙確定坐標系及程序原點。我國數控車削工藝使用的數控刀架多為四工位結構,部分車床使用六工位及轉塔式刀架,雖然使用刀架類別不同,但是其基本工作原理大同小異,現以四工位刀架為例就其數控車削對刀原理進行分析探究。操作人員首先需要將四把刀具安裝到對應刀架上,由于四把刀具位于不同位置且存在一定偏差,此時就需要選定一把刀作為基準,以此為基礎將相關參數輸入其中并進行程序編制,待參數輸入完畢后程序會自動對剩余三把刀具讀取刀補值,并完成對刀處理。
通過與基準刀的碰觸,明確偏差位移,并將測得數據錄入中控系統,在進行數控車削加工工作時,編制程序會自動對每把刀具的偏移差進行補植處理。對刀操作工藝就其實質而言就是根據零部件特點設定數控車削體系、編制數控車削程序,并借助常用的 G92、G59、G54、G50等代碼實現精準對刀處理。對刀方法基本工作原理如圖 1 所示。由圖 1 可知,設定的程序原點通常情況下需要與零部件設計基準處于同一位置,編程人員需要依照坐標系上標定的坐標數據調控編制刀尖走向。位于初始原點的刀尖與程序設定原點間存在X 向及 Z 向的偏移,由此導致刀尖在執行程序指令時也會存在類似偏移情況,此時就需要計算測定這一偏移距離,并通過數控技術調整規范刀尖運行軌跡。
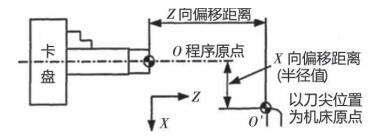
圖 1 數控車削對刀方法工作原理
2、數控車削加工中的實用對刀方法及操作技巧
不同類別的數控機床對應的對刀方法存在較大差異,基本對刀流程及操作技巧也存在一定偏差。一般情況下,數控對刀操作主要分為機外對刀、機內對刀這兩大類,其中機內對刀在數控車削加工工藝中最為常見。下面就數控車削加工工藝中常見的實用對刀方法及操作技巧進行簡單概述與分析。
2.1 試切法
試切法在數控車削加工工藝中的應用最為廣泛,采用試切法進行對刀測定時無須其他輔助工具,只需要確保零部件緊密安裝到卡盤中即可。零部件安裝完畢后,機床與工件在坐標系中沒有位于同一位置,為了后續編程計量工作的順利進行,編程人員需要綜合考慮多方因素,在此基礎上設置建立工件坐標系,劃定刀具運行范圍,以確保對刀操作精準無誤,也將刀具走向劃分到合理范圍內,以免影響零部件的數控車削質量。刀具刀尖準確放置在起刀點后,數控機床自動回歸到原始位點,操作人員將綠色指示燈開啟后,系統進入開啟狀態;在操作界面下的 MDI 模式中確定基準刀具,通過切換機床畫面的方式對其他刀具的補償值分別進行設定;在進行手動對刀操作時需要確保對刀方向維持不變,及時記錄 X 軸坐標,并將測量獲得的零部件孔徑及外部直徑輸入到數控機床編程系統中;以同樣方式對平斷面進行試切處理,并確保退刀過程的平穩性,盡量避免出現位置偏移情況,將獲得的補償值轉換為 Z 軸坐標并錄入系統中。剩余刀具的對刀補償與前面所述的方法基本一致,只需加工處理零部件端面即可,無須再進行切削處理。為了提高試切對刀操作工藝準確性,操作人員還需仔細確認刀具半徑、輸入對應補償數值,并將處于不同假想位置的補償數值錄入數控編程系統中。
綜上可知,試切法屬于手工對刀范疇,具有對刀方式簡單、精度控制較高、對刀時間較長的特點,其中刀具尺寸及圓弧半徑的測量精準性直接關系著數控對刀質量。
2.2 對刀儀法
對刀儀法隸屬于機外對刀范疇,操作人員需要整合分析刀尖假想位置、刀具與兩軸間距,并利用對刀儀在數控機床上完成刀具校對工作,隨后才能進入后續的裝機使用操作。對刀儀主要由精度較高的測頭、信號傳輸模塊及兼具硬性、耐磨性的對刀探針這三大核心部件組成。對刀探針直接與刀具接觸,在繞性支撐桿的作用下能夠將其與刀具的作用力傳輸到高精測頭;信號傳輸模塊能夠自動接收來自高精測頭的通(斷)指令,將識別、獲取的刀具參數及補償信息傳輸給數控系統。在利用對刀儀進行對刀控制工作時需要搭建工具臺,安裝刀具臺,并確保刀具臺與刀架尺寸一致,以提高對刀工藝精準性。具體操作流程如下:首先將刀具固定在刀具臺上,順次搖動 X 向、Z 向手柄,確保放大鏡能夠在這兩個方向上平穩移動到與刀尖向重合的位置;隨后利用微型讀數儀采集對應數據,以準確獲得刀具長度信息;最后操作人員需要將刀座一并裝入數控機床上,并將獲得的刀具長度及補償數值輸入數控程序,以便后續的數控車削工藝得以順暢進行。
操作人員在利用對刀儀進行對刀處理時不會使用到數控機床,因此不會影響數控車削工作的正常進行。調查顯示,利用數控車削加工零部件的時間,約有 55% 的占比為純機動時間,剩余的 45% 則是對刀、裝夾等工具的輔助時間,由此可見對刀儀的優越性。綜上可知,對刀儀法相較于其他對刀方法而言具有較高的工作效率,但是由于刀具、刀座需要配合使用,因此需要準備兩份一樣的刀具與刀座,相對而言成本會有所增加。就我國數控車削加工企業而言,為了節省前期生產制造成本,在進行數控車削對刀操作時往往會忽略這一對刀方法,因此這一方法常出現在研究機構中。
2.3 ATC 對刀法
ATC 對刀法(Automatically Tool Calculated)又被稱為光學對刀法,隸屬于機內對刀法范疇,主要利用顯微鏡技術對刀具長度、刀尖位置、圓弧直徑、主(幅)偏角進行測定分析。一般情況下,操作人員需將顯微鏡及刀架拆卸下來,只有進行對刀操作時才需要將它們重新安裝到主軸箱上。操作人員需要將刀尖放置在顯微鏡合理檢測范圍內,并通過手動移動的方式調整刀架位置,以確保假想刀尖與顯微鏡中心相重合,此時點擊分析按鈕獲得刀具在X 軸及 Z 軸的長度,計算獲得刀具補償值。具體操作流程:操作人員依照測定規范安裝好基準刀及顯微鏡,確保刀具處于基準點位置,手動調節刀架、轉動刀位,預留出安裝鏜孔刀具的位置;根據鏜孔刀具外形特點確定安裝位置、設定對刀程序,緩慢移動刀架到對刀位置后點擊暫停按鈕,并完成鏜刀安裝工作;待鏜刀刀尖與中心位點重合時點擊對刀按鈕,對刀結束后確保刀架歸位才能在對其余的刀具進行對刀處理。
ATC對刀法相較于其他對刀法而言表現出較高的品質、較高的精度,且刀具之間不會相互接觸,因此常被用于螺紋、仿形等特殊角度刀具的對刀處理,且不會對刀具刀尖造成不良影響。但是該對刀方法價格成本更高,需要操作人員妥善保管顯微鏡等測量工具;操作工序較為復雜,每次對刀操作前需要裝卸顯微鏡模塊,極易因安裝誤差影響數控車削對刀工藝精準性。除此之外,操作人員在進行零部件加工時需要將偏移量準確錄入數控程序中,一旦出現錄入錯誤也會影響對刀操作準確性、穩定性。
2.4 全自動對刀法
為了進一步提高對刀操作工序的工作效率與質量,研究人員成功將計算機數控系統(Computer Numerical Control,CNC)應用到了數控車削對刀工序上。CNC 系統中的存儲器涵蓋了多個智能程序,能夠通過接口電路及伺服驅動裝置與特定計算機網絡相連,并通過對操作人員輸入的加工程序進行數據處理及插補運算,計算獲得最佳運動軌跡,并將相關新型傳輸到執行模塊,以此控制數控車床加工生產出特定的零部件。數據機床在這一智能系統的支持下能夠自動對 X 軸、Z 軸長度進行測定分析,并通過后臺系統計算出刀具補償值,不會因后臺計算而導致數控車削工序出現停頓問題,由此進一步保證了數控車削質量與效率。自動對刀裝置涵蓋了硬件系統及軟件程序兩大模塊,常由 CNC 制造廠家負責刀尖檢測程序的安裝與調試。為了確保對刀操作精準性,至少需要連續進行兩次對刀操作工序,兩次的刀檢差值只有在 2um 的合理范圍內才可進行后續的數控車削操作。全自動對刀法相較于其他對刀操作而言精準性更高、操作更為簡便,因此已然成為新興對刀方法,并在多個數控車削機床上得到了廣泛應用。
3、結束語
數控車削加工工藝涉及到多個類別的刀具,由于刀具尺寸、規格不同,需要根據實際情況選擇適宜的對刀方法,并在此基礎上調試好數控程序,保證對刀參數及補償數值的精準性。操作人員在進行數控車削對刀工藝時需要調試好刀具安裝位置、準確錄入補償參數,以加工制造出符合規定標準的零部件,進而提高數控車削加工的工作效率與質量。
投稿箱:
如果您有機床行業、企業相關新聞稿件發表,或進行資訊合作,歡迎聯系本網編輯部, 郵箱:skjcsc@vip.sina.com
如果您有機床行業、企業相關新聞稿件發表,或進行資訊合作,歡迎聯系本網編輯部, 郵箱:skjcsc@vip.sina.com
更多相關信息