軸齒輪高效復合柔性加工機床研究
2021-2-2 來源:陜西秦川精密數控機床工程研究有限公司 作者:李瑞亮,劉 耀,車亞肖
摘 要:隨著轎車和新能源汽車變速箱需求增加,對軸齒輪的加工提出了更高要求。研究了軸齒輪高效復合加工機床,組合了傳統的軸齒輪熱前加工工藝,將軸齒輪加工的全部工藝集成在一臺機床內,對工件進行一次裝夾,完成所有工藝加工過程。采用了床身立柱一體化設計理念,通過應用高速干切技術和柔性配置功能,大大提高了機床的加工能力和生產效率,實現了軸齒輪高效、高精度、綠色環保的加工需求。
關鍵詞:軸齒輪;高效加工;復合機床
0、引 言
隨著汽車工業的快速發展,傳統轎車和新能源汽車變速箱對軸齒輪的需求大大增加。軸齒輪熱前加工工藝形式復雜,工序繁瑣。目前多數用戶仍在采用工序較長的傳統加工方法,即車削→滾齒→去毛刺→倒棱→銑鍵槽 (鉆孔),加工的全過程時間較長,而且很多用戶面臨招工難、人力成本上升等難題,導致對于軸齒輪這種長工序加工憂心忡忡。本文針對這些問題設計了一種全新的軸齒輪高效復合柔性加工機床。
1、機床性能及布局
機床左邊采用傳統的七軸滾齒機床布局,為了合理利用空間尺寸,與傳統滾齒機相比,進給軸 X 軸采用了傾斜設計,使Y軸與Z軸存在夾角。右邊采用柔性設計單元,根據客戶零件加工工藝柔性配置,下面以其中一種配置為例講述復合機床的功能,具體結構如圖1所示。在右邊柔性單元里面配置了動力刀塔,通過刀塔的旋轉可實現不同工序的加工,集成了軸齒輪車削、滾齒、倒棱、去毛刺、銑鍵槽 (鉆孔)、自動上下料等柔性單元。
該復合機床共有11個數控軸:X軸、Y軸、Z軸、A軸、B軸、C軸、Z2軸、X3軸、Y3軸、Z3軸及C3軸。各軸在機床中的運動關系和作用如下:X軸是滾齒機滾刀的徑向進給軸,X軸運動保證軸齒輪的齒深尺寸;Y 軸是滾齒機滾刀的切向進給軸,隨著加工過程中 Y 軸的移動,可以改變刀具與工件的接觸點位置,有利于刀具壽命的提高;Z軸是滾齒機滾刀的軸向移動軸,Z軸的移動保證軸齒輪的齒寬尺寸;A軸是滾齒機滾刀架角度旋轉軸,根據工件的螺旋角和滾刀的螺旋升角確定A軸的角度;B軸是滾齒機主軸;C軸是工作臺旋轉運動,B軸和 C 軸保持一定的速比關系,兩軸聯動加工出軸齒輪,并保證軸齒輪的精度;同時 C 軸也是車削加工時的工件旋轉主軸;Z2軸是尾座頂尖上下移動軸,實現對工件的自動頂持;X3軸是刀塔徑向移動軸,用于車刀的徑向進給;Y3軸是刀塔的對中運動軸,用于刀塔與工作臺的中心重合;Z3軸是刀塔軸向移動軸,用于車刀的軸向進給,與 X3軸配合使用可加工出軸的圓柱面;C3軸的刀塔旋轉軸,用于選擇不同的刀位進行不同工序的加工;其中滾齒加工過程中 X 軸、Z 軸、B 軸、C軸四軸聯動。

圖1:軸齒輪復合加工機床結構圖
機床設計將軸齒輪加工的全部工藝集成在一臺機床內,對工件進行一次裝夾,利用工作臺的旋轉,通過不同加工刀具的切換,以及對應刀具的軸向和徑向進給來實現對不同規格的軸齒輪進行車削、滾齒、倒棱、去毛刺、銑鍵槽 (鉆孔) 的熱前加工。這種布局方式節省了工件上下料時間,確保了加工基準的統一,提高了加工效率和加工精度。機床是11 軸四聯動高效復合機床,整機還采用高速干切技術,實現軸齒輪高效高精度、節能環保加工,而且自動化和柔性程度高。同時機床具有很好的擴展性,為齒輪生產線配置預留了接口空間及控制反饋接口,便于后期車間自動化產線的實現。
2、床身立柱一體化設計
此復合機床將床身和立柱進行了一體化設計,這樣既保證了機床整體的剛性,又有利于機床裝配質量的提高。對床身立柱整體進行了有限元受力分 析 。 床身立柱材料為HT300,使用通用結構分析軟件 ANSYS Workbench Environ?ment (AWE) 15.0 多物理場協同 CAE 仿真件,建立了立柱有限元實體模型和床身立柱所受載荷情況如圖2所示。
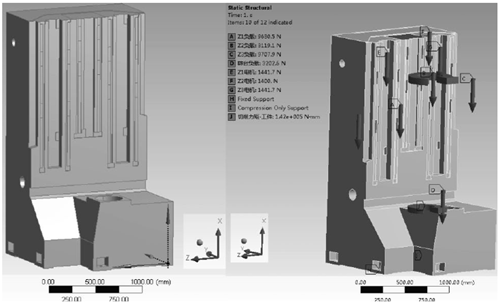
圖2:床身立柱載荷分布
采用自動劃分網格方法對有限元實體模型進行單元網格劃分,由分析知,立柱的最大變形為沿著y軸負方向前傾,最大變形量為30 μm,加工區域變形量約20 μm,該變形符合設計要求,變形情況如圖3所示。

圖3:床身立柱變形圖
3、綠色環保高速干切技術應用
隨著國家環境管理體系標準的實施以及車間環境污染相關法律法規的日益嚴格,機床設備的綠色制造已成為今后發展的重要方向,所以在機床設計時應用了綠色環保的高速干切技術。高速干切主要體現在以下幾個方面。
3.1、排屑系統
隨著國家對環保節能的重視,對生產企業的傳統切削油管理越來越嚴格,地方政府甚至呼吁不使用切削油,所以高速干式切削是以后的發展趨勢[4]。但是沒有切削油,干式切削產生的鐵屑不易排出,而且干式切削產生的鐵屑速度快,溫度高,若不能及時快速的使鐵屑排出,對刀具、工件和床身帶來的熱變形巨大,從而影響軸齒輪的加工精度,因此必須采用有效的排屑系統。在干式加工中,鐵屑是刀具和工件相互擠壓產生,為了減少鐵屑對刀具,工件和床身帶來的影響,必須使鐵屑快速離開刀具及工件,并通過排屑系統快速流走,減少鐵屑與床身的接觸時間。
在設計中改變床身結構,加大鐵屑流道斜度,便于鐵屑及時導出。同時在排屑流道面采用了不銹鋼隔熱罩,隔熱罩與床身之間留有一定的小間隙,不銹鋼材料表面光滑有利于鐵屑排走,而且不銹鋼的熱傳導系數小,可以減少鐵屑熱量的傳遞,同時設計隔熱罩與床身之間沒有完全接觸,減少了床身的熱變形,具體結構如圖4所示。

圖4:干切排屑系統
3.2、高轉速主軸和工作臺
高速干切加工必須要刀具和工件的高速旋轉才能滿足干式切削的需求,干式滾切加工中滾刀線速度的要求為200 m/min甚至更高,目前一般涂層的高速鋼滾刀可以達到這個速度,但是硬質合金滾刀線速度可以達到300~400 m/min,這就需要滾刀主軸達到高轉速。而對于工作臺面為了達到車削時干式切削,同樣也要設計為高轉速工作臺。為了實現高速加工,對于刀具主軸通常采用電主軸或者直驅電機來實現;對于工作臺,采用直驅電機來實現。這臺復合機床刀具主軸設計轉速4000 r/min,工作臺面設計轉速2000 r/min。
3.3、高速刀具
干式切削用的刀具材料發展初期采用硬質合金鋼,但由于硬質合金鋼滾刀成本昂貴,近幾年發展的粉末冶金高速鋼滾刀以及 TiAIN 涂層高速鋼滾刀取代了硬質合金鋼滾刀。最新研究報告和實際使用效果來看,干式滾切相對于常規濕滾而言,加工時間短,成本更低。采用粉末冶金高速鋼滾刀甚至比采用硬質合金鋼滾刀具有更好的干式滾切加工效果。目前我國漢江工具生產的涂層滾刀線速度已經可以達到240~300 m/min,國外格里森的涂層滾刀線速度已經可以達到300 m/min 以上。干式滾切加工機床的切削速度可達傳統加工的 4 倍,生產效率可以提高 3 倍。與濕式加工相比,加工成本降低,能得到更好的零件質量,且無油污污染,車間工作環境更加潔凈。
4、復合柔性功能設計
對于這臺復合機床,圖 1 所示的只是其中一種柔性配置,在這一種配置中,刀塔共有 12 個刀位,可以根據客戶工藝需求配置不同的功能,可以配置車刀、倒棱、去毛細、銑刀、鉆頭、測頭、手抓等功能,刀塔配置圖如圖 5所示。
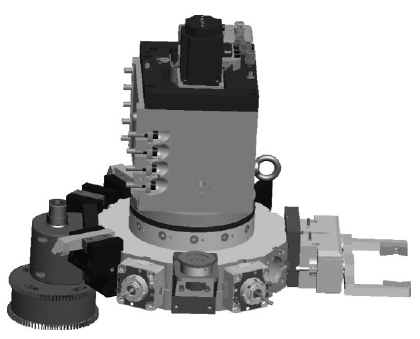
圖5:刀塔刀位配置
除了圖 1 的配置外,還有其他柔性配置結構,柔性單元配置部分可以采用去毛刺、倒棱和桁架上下料機構的形式,如圖 6 所示。除了以上幾種配置外還可以采取其他的配置形式,大大增大了機床加工的柔性功能。
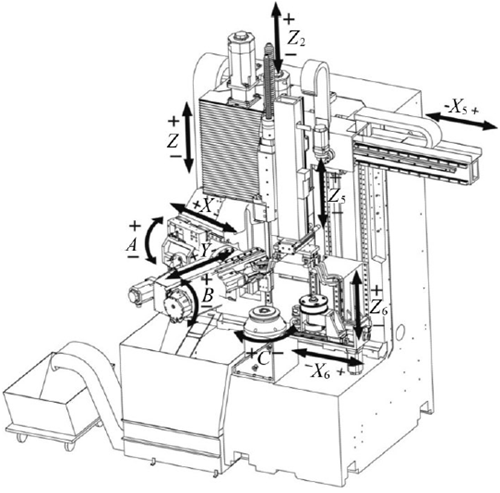
圖6:機床配置形式
5、結束語
本文設計的軸齒輪高效復合柔性加工機床體現了以人為本、綠色制造的設計理念,特別適合于傳統轎車和新能源汽車變速箱軸齒輪大批量、高精度加工。經過實際使用,滾刀平均滾切線速度可達200 m/min以上,復合加工效率為傳統工藝的 2~3 倍,軸齒輪加工精度可達 GB/T10095.1-2008 的 6 級,配備自動上下料機械手可自動抓取和卸放工件,配備料倉后可實現 12 h 無人值守工作模式,提高產品加工效率,提高企業自動化水平。
投稿箱:
如果您有機床行業、企業相關新聞稿件發表,或進行資訊合作,歡迎聯系本網編輯部, 郵箱:skjcsc@vip.sina.com
如果您有機床行業、企業相關新聞稿件發表,或進行資訊合作,歡迎聯系本網編輯部, 郵箱:skjcsc@vip.sina.com
更多相關信息