鍛壓機床系統設計優化路徑
2018-6-14 來源:中鐵十八局機械廠 作者:張唐善
摘要:利用遺傳算法對鍛壓機床系統進行優化設計,在該方法基礎上開發一種多目標優化的設計平臺,運用 Pro/E 的建模和分析能力,既能夠保障模型的精確性,又能夠保障分析結果的準確性,實現多參數和目標的優化,進而提高鍛壓機床系統的設計效率。
關鍵詞:鍛壓機床;系統設計;遺傳算法;多目標優化 DOI:10.16621/j.cnki.issn1001-0599.2017.03.26
0、 前言
鍛壓機床作為汽車制造和交通運輸行業等重要領域的基礎裝備,對其系統進行優化設計能夠提高運行的效率,優化性能,進而為企業的維修節省費用。結構優化的主要內容包括尺寸、拓撲和形狀等的優化,其目的都是在于確定最優的設計方案,提高鍛壓機床的運行效率。機床結構的優化主要包括對其整體結構的優化以及對其尺寸和零部件的優化,進而提高鍛壓機床整體的運行效率。這些優化都是對鍛壓機床結構域的靜態優化和改善,能夠提高鍛壓機床在運動狀態中的穩定性能,進而達到節省材料的作用。本研究主要是運用遺傳算法,結合上述的優化設計方法,以優化全局的思路對鍛壓機床的關鍵部件以及結構進行優化設計,設定鍛壓機床在開關狀態下的目標函數,以達到穩定的性能,同時運用遺傳算法進行多目標的優化設計,進而獲取鍛壓機床最優的結構參數,減少鍛壓機床的機身質量,提升機床的性能和運行效率。
1 、多目標優化設計平臺的結構和優化流程
近年來隨著 CAD/CAE 技術的快速發展,鍛壓機床優化設計在 CAD/CAE 軟件中應用的范圍逐漸的廣泛,能夠將機床系統進行分析計算以達到最優的設計效果。有限元靜態分析主要針對鍛壓機床的機身部件的硬度以及強度進行分析,達到最優的結構和質量,進而降低成本,達到較高的經濟效益。Pro/E,UG 等實體模型軟件能夠將機床的實體模型建立起來并通過 CAE 進行分析,為結構的優化設計提供指導的方向,但也有自身缺點,不能實現多參數的協同優化。MATLAB 等數字分析軟件能夠實現多個參與情況下模型之間的協同優化,但缺少對模型實體的分析,優化的結果不精確。利用 Pro/E 軟件的二次開發功能,結合數字分析軟件 MATLAB 的擴展功能,集成一個多目標的優化設計平臺,對鍛壓機床系統進行優化設計,對鍛壓機床的實體模型進行有限元分析,并結合遺傳算法實現多目標參數的優化。
1.1 平臺結構
多目標優化設計平臺結構見圖1,實體模型庫、調度管理系統、分析計算系統以及參數優化系統 4 個主系統構成了該平臺的主要系統,每一個系統有著自身獨特的優點和性能。實體模型庫系統主要是運用 Pro/E 軟件實現對零件的三維建模,實現裝配模型的功能,進而建立 SQL Server 數據庫,構建出的鍛壓機床模型數據庫完善且精確。分析計算系統主要是是利用 Pro/Mechanical 平臺,優化實體模型的參數和結構,加載計算零件和組織的參數,計算出各種應力和應變的計算結果。參數優化系統是在 MATLAB 軟件平臺下對各種參數進行分析,利用調度管理系統獲得分析和計算的結果,在目標函數的引導下對分析和計算的結果進行多次的處理,優化參數。調度管理系統主要是負責管理其他 3 個系統的管理,也是該平臺的核心系統,能夠將模型庫輸入到分析計算系統中,然后將分析計算系統中的結果輸入到參數優化系統中,獲取優化的結果能夠對模型庫的參數進行修改,分析計算后獲得最優的參數。
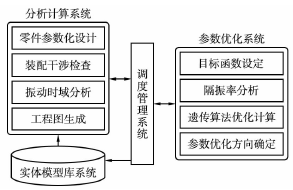
圖 1 多目標優化設計平臺的結構示意圖
1.2 平臺優化流程(圖 2)
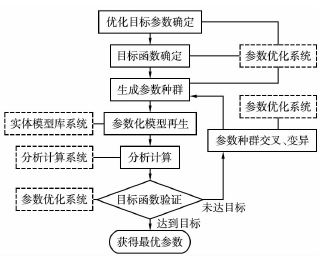
圖 2 多目標優化設計平臺優化流程的性能和運行效率
多目標優化平臺的 4 個主系統分工合作,共同優化鍛壓機床的各個參數。優化平臺能夠根據分析計算的結果對模型庫參數進行設計,根據鍛壓機床的工作特性以及預先確定的最優目標函數,設計出鍛壓機床各個構建的最優參數,通過調度管理系統實現對模型庫參數的改進載入到分析計算系統中得到結果,獲得最優的目標函數,針對結構進行參數的處理和篩選,再次進行迭代計算,獲取最優的參數。
2、 系統設計
2.1 模型庫系統和分析計算系統設計
模型庫系統的主要功能是對鍛壓機床的零件以及組間模型進行存儲,生成文件系統,為外部的調度管理系統提供零件和部件修改的參數,并且能夠快速的將組間的模型參數結果計算出來。鍛壓機床模型作為一種三維實體模型,是在 Pro/E 條件下建立的,能夠分類存儲鍛壓機床各個零件的參數,模型庫中包含了鍛壓機床模型的名稱、結構信息以及位置等,能夠通過調度管理系統查看相關的模型。
分析系統的是利用 Pro/E 軟件中的 Pro/Mechanical 平臺建立的,主要功能是對三維實體模型進行有限元分析。分析系統能夠根據調度系統中的模型庫,給鍛壓機床設計預先的載荷、約束等,將零件的應變力和局部變形結果計算出來,并且將計算的結構傳送到調度系統中。
2.2 調度管理系統設計
調度管理系統主要的功能是幫助其他的幾個子系統訪問模型庫,修改模型庫的參數,管理機床的分析數據,得到計算的結果,并將計算的結果進行傳輸,獲得最佳的優化方案。調度管理系統主要是運用了 Pro/E 軟件的二次開發功能,能夠實現對數據庫的調度和管理,以編程的方式實現特定的功能。在調度管理系統的優化平臺設計中利用 C++的 MFC 類庫,利用二次開發的功能對系統進行優化設計。調度管理系統能夠將模型的 ID 存儲在模型庫中的實體模型中,然后按照模型的參數和尺寸進行重新的配置,檢查裝置是否符合約束的條件。如果條件滿足,就按照最優的設置參數進行模型的設計,建立優化后的模型,利用軟件的分析功能實現模型的驅動。調度管理系統的優化流程見圖 3。調度管理系統能夠優化設計的參數主要是在軟件平臺上開發一個動態的鏈接庫。參數的優化能夠通過參數種群進行分析和篩選,獲得的計算結構反饋給參數優化系統,進而設計目標函數,在遺傳算法的基礎下進行參數的優化,最終得到優化的參數。
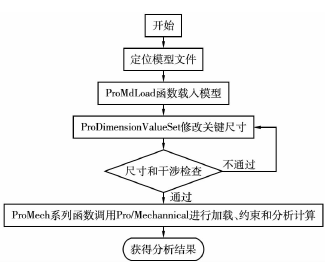
圖 3 調度管理流程
3 、基于遺傳算法的參數優化算法
3.1 變量設計
本系統變量的設計根據不同型號的鍛壓機床優化的目標不同,經過分析和判斷,將鍛壓機床的上下橫梁的縱橫向板厚以及板間距作為變量。
3.2 目標函數
鍛壓機床設計的主要目的在于提高鍛壓機床的準確度和穩定性能,并且將鍛壓機床的材料質量縮小到最低,在應力范圍內設計鍛壓機床的材料,進而降低鍛壓機床的成本,達到穩定的性能。因此本文的目標函數主要作用在鍛壓機床的上下橫梁的縱橫彎曲度以及最大應力和機身的質量上。本系統鍛壓機床的精確度和穩定性主要依靠機床上橫梁的縱橫向彎曲度來確定,彎曲度越大,說明鍛壓機床的精確度越高,抗振性能越高。說明該參數下鍛壓機床較為穩定。在設置優化目標函數時也將這兩個變量作為設計的依據。為了提高鍛壓機床的運行效率和生產成本,在保障其精確度的條件下,優化目標函數將鍛壓機床的機身作為一個考慮的因素。另外應力集中也是優化目標函數需要重點考慮的一個問題。相關實驗表明,鍛壓機床集中應力越大,其磨損度就越嚴重。因此通過以上的分析可以得到以下的目標函數。

3.3 遺傳算法
本系統的編碼采用自定義函數,變量的數目為 4 個,變量離散值個數為 mi個,設計變量為 x。設置遺傳算子,采用 MATLAB進行,并將其作為比例函數的 Rank,參數的選擇采用隨機分布的方式,參數的再生利用遺傳算法的缺省進行,約束的處理采用懲罰函數法,每一個個體的適應度上添加一個懲罰因子,這樣能夠滿足個體的適應度,也就是:
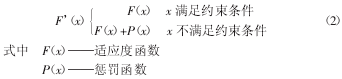
4、 實例計算
本文以某型號的鍛壓機床為例對其系統進行優化設計。表1 和表 2 為優化前后鍛壓機床各參數的變化情況和技術指標對比。

表 1 優化前后參數的變化

表 2 優化前后技術指標的變化
鍛壓機床經過多目標優化后,縱向變形差縮小到 0.28mm,橫向變形差縮小到 0.38 mm,最大應力減小到 196 MPa,機身的總重量減小到 255 880 kg,達到了多個目標的優化,同時能夠減輕機身的質量,使得機床的結構更加的穩定,性能提高,應力分配在數值范圍內,提高了鍛壓機床的運行效率。說明多目優化的遺傳算法能夠將鍛壓機床系統設計到最佳的性能。
5 、結語
通過對鍛壓機床進行優化設計,設計出一個保障鍛壓機床設計性能的良好平臺,在該平臺上進行調度管理系統、分析計算系統和參數優化系統的設計,實現對鍛壓機床機身結構以及參數的協同管理和優化計算,利用有限元分析和多目標的遺傳算法,優化鍛壓機床縱橫向的變形差、最大應力以及機身的質量,實現了最優的目標。
投稿箱:
如果您有機床行業、企業相關新聞稿件發表,或進行資訊合作,歡迎聯系本網編輯部, 郵箱:skjcsc@vip.sina.com
如果您有機床行業、企業相關新聞稿件發表,或進行資訊合作,歡迎聯系本網編輯部, 郵箱:skjcsc@vip.sina.com