單拐曲軸多向擠壓模具的設計與優化
2019-1-17 來源: 北京機電研究所 作者:劉麗英,石一磬,徐春國,陳鈺金,鄭建,等
摘要: 單拐曲軸多向擠壓成形較傳統生產方式大大縮短了工藝流程,實現了單拐曲軸的全流線成形,且批量生產對其模具設計也提出了更高的要求,針對單拐曲軸多向擠壓工藝模具的特點,從模具的服役環境出發,對多向模具結構中鑲塊部分進行分析和優化。根據鑲塊分模面的位置不同,設計了 “窄鑲塊”和 “寬鑲塊”兩種類型,通過數值模擬和實驗驗證的方法,進行了較深入的分析和對比。研究結果表明: 采用鑲塊方式設計模具具有可行性, “寬鑲塊”模具結構具有較高強度和剛度;實驗中窄鑲塊易出現 “折痕”缺陷,而采用寬鑲塊結構有效避免了該類缺陷。鑲塊結構有助于降低單拐曲軸模具制造成本和提高產品質量。
關鍵詞: 單拐曲軸; 多向擠壓; 鑲塊設計; 鑲塊分模面; 模具設計
單拐曲軸是動力機械中重要的傳動構件,主要應用于農用機械、小型動力機械、園林機械等設備,實現動力的輸出。曲軸在工作過程中受連桿傳遞的壓力、慣性力及慣性力矩的作用,且承受交變載荷,因此,要求曲軸具有足夠的剛度和疲勞強度以及良好的沖擊性能。
目前,國內外單拐曲軸主要生產商仍采用 預 鍛、終 鍛、切 邊 等 一 系 列 工 序 進 行 生產,該工藝材料利用率低,材料浪費達 30% ,綜合成本較高。然而,單拐曲軸多向擠壓工藝是近年來新興的成形方法,該工藝采用楔橫軋預制坯實現坯料的高效精確成形,采用彎曲工藝實現軸頸材料的轉移,采用閉式雙向擠壓工序實現最終鍛件形狀的成形,該成套工藝具有易于實現自動化、產品精度高、材料利用率高等明顯的技術經濟優勢和良好的應用前景。
1 、單拐曲軸多向擠壓成形工藝
單拐曲軸可分為主軸頸、連桿頸、平衡塊 3 個組成部分,如圖 1 所示。
主軸頸主要用來支撐曲軸,連桿頸用來安裝連桿的大頭一端,是將活塞的往復運動轉化為循環旋轉運動,連桿頸通常被制成中空,目的是為了減輕曲拐旋轉部分的質量,以減小離心力; 平衡塊的作用是平衡曲軸的離心力和離心力矩。
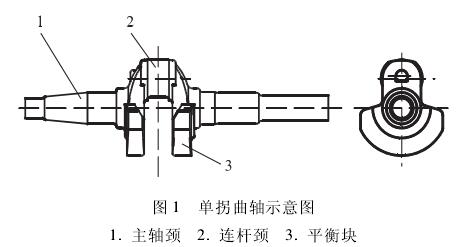
單拐曲軸多向擠壓成形新工藝由下料、楔橫軋制坯、壓彎、閉式擠壓工序組成,如圖 2 所示。其中,楔橫軋制坯和壓彎工序主要實現材料的體積分配和轉移,即楔橫軋工序精確地預分配了兩端平衡塊所需的金屬體積,并完成了主軸頸臺階軸的精確成形,壓彎工序實現了平衡塊部分和連桿頸相對位置的偏心特征,閉式擠壓工序完成了兩側平衡塊部分的最終成形以及主軸頸和連桿頸部分的精整,整個工藝只有楔橫軋料頭的材料損失,材料利用率高達 90% 以上。
整個鍛造成形過程由高剛度楔橫軋機和多向模鍛液壓機兩臺設備完成,楔橫軋機的進料、軋制、出料等自動完成,該工藝的生產線易于實現全自動生產
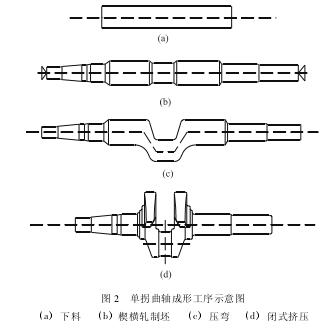
2 、單拐曲軸多向擠壓模具設計
根據產品特點,單拐曲軸多向擠壓模具主要采用上下分模,方便鍛件的放入和取出,以平衡塊形狀為基礎,通過左右沖頭的雙向擠壓成形兩側的平衡塊,從而實現單拐曲軸鍛件的少無飛邊成形。
如圖 3 所示,采用整體式上下模具的方式,該方式有效地保證了該區域模具強度,但由于模具磨損不可避免,需更換整體上下模具。連桿頸和左右平衡塊部分金屬流動較為復雜,是模具磨損和熱應力產生的重要區域,也是模具設計的關鍵部分。
考慮到經濟性,將平衡塊內側部分采用鑲塊結構代,如圖 4 所示。當磨損嚴重時,只需更換鑲塊部分模具,從而降低模具成本。
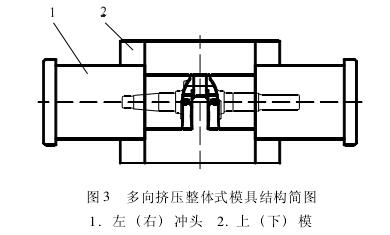
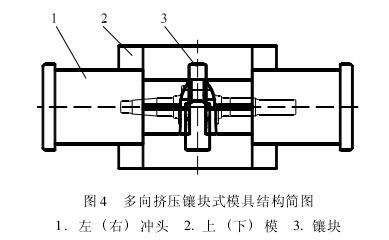
從單拐曲軸鍛件的形狀可以看出,該零件的左右部分 ( 包括平衡塊) 是非對稱的,連桿頸和平衡塊沿軸線也是非對稱的,而從上下合模方向來看,是對稱的。因此,設計鑲塊結構需兼顧考慮通用和防錯裝。
上下對稱部分設計為對稱結構,在連桿頸和平衡塊的非對稱方向上,連桿頸一側設計出一個寬度不一致的臺階形狀,以實現自動防錯安裝,如圖 5 所示。單拐曲軸多向擠壓工藝的上下模具、中間的平衡塊內襠和連桿頸部分形成凸塊,該部位的金屬流動劇烈,是整個模具最主要的受力區域,也是模具磨損的重點區域,因此,將該凸塊部位設計為鑲塊結構,該鑲塊的寬度基本與左右方向的分模面重合,如圖 5a 示。
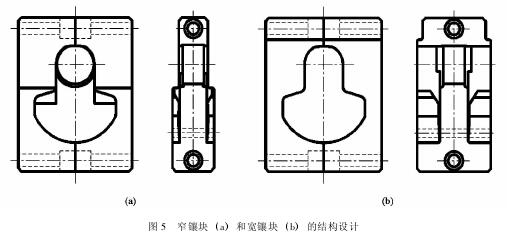
綜合考慮鑲塊的強度和鍛件的成形質量,可將鑲塊適當加寬,使鑲塊的寬度大于最終成形的單拐曲軸鍛件的平衡塊寬度,使平衡塊的最大輪廓部分的金屬充填過程完全在鑲塊內完成,加寬后鑲塊部分的剛性更好,如圖 5b 所示。
前者鑲塊質量小,加工方便,節約較昂貴的模具材料,后者強度和剛度較好,鍛件成形質量更好。
3 、鑲塊的有限元分析
3. 1 模擬條件
根據上述問題對模具鑲塊部分強度和剛度進行數值模擬分析,分別對窄鑲塊和寬鑲塊進行數值模擬,分析其強度和剛度。鑲塊采用 H13 模具 鋼,200 ℃ 下材料彈性模量為 210 GPa,泊松比為 0. 3,屈服強度 Re L為 520 MPa,抗拉強度 Rm為 808 MPa。由于多向模鍛液壓機兩側缸存在一定的同步誤差,故設置鑲塊與坯料接觸面的壓力為 200 k N,設置另一側的鑲塊與模具接觸為完全固定約束,底面限制一個方向的自由度,如圖 6 所示,將其離散為三維四面體二次實體單元進行模擬。
3. 2 模擬對比結果
3. 2. 1 等效應力對比分析
窄鑲塊和寬鑲塊的等效應力云圖如圖 7 所示。由圖 7 可知,窄鑲塊的最大等效應力為 765 MPa,寬鑲塊的最大等效應力為 507 MPa。根據應力分布區域可知,窄鑲塊的大部分區域尤其是成形連桿頸部位應力較大,而寬鑲塊因周圍材料的約束而應力有所改善。因此,寬鑲塊強度較好,有效地改善了應力分布。
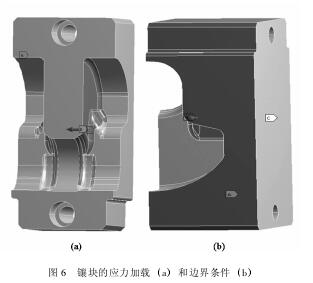
3. 2. 2 鑲塊剛度分析
圖 8 為窄鑲塊和寬鑲塊的等效應變云圖。由圖8 可知,兩者應變分布區域相似,成形連桿頸處模具的等效應變值較大,窄鑲塊的最大等效應變值為0. 011,寬鑲塊的最大等效應變為 0. 0025。為考察鑲塊在厚度方向的變形,圖 9 為鑲塊 X 方向 ( 即寬度方向) 位移圖,窄鑲塊最大位移為 0. 057 mm,寬鑲塊最大位移為 0. 0567 mm,變形量相差甚微。
圖10 為鑲塊受力面示意圖。黑色陰影部分為鑲塊與坯料接觸部分的投影,由窄鑲塊的受力可以看出,坯料在成形時,由于左右側缸不同步,產生的位移量為 0. 057 m,會增大模具間隙,從而會在曲軸平衡塊位置留下痕跡。對于寬鑲塊而言,由于與坯料接觸部分的投影,包含在整個鑲塊的投影范圍內,故雖然產生一定的彈性變形量,但不會在平衡塊位置留下痕跡。
綜上分析可知,窄鑲塊的剛度較差,而采用寬鑲塊結構有效地改善了剛度,且改善了單拐曲軸平衡塊位置的成形質量。
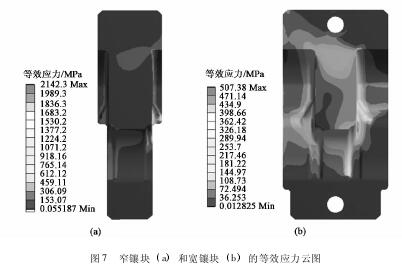
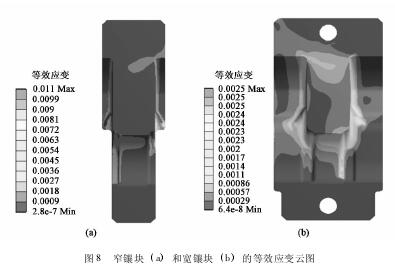
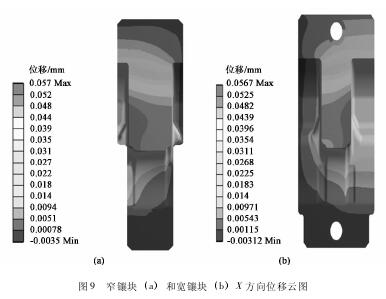
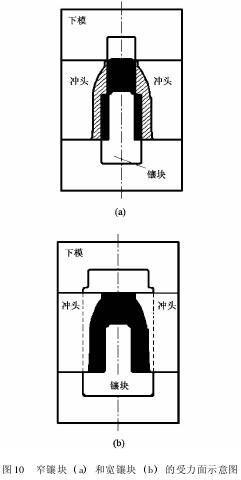
4 、實驗驗證結果與討論
4. 1 實驗設備與模具
單拐曲軸實驗設備采用多向模鍛液壓機,其主缸最大成形力為 4000 k N,左右側缸成形力為 4000 k N,分別采用窄鑲塊和寬鑲塊進行實驗,實驗鑲塊對比如圖 11 所示。
4. 2 實驗結果與討論
圖 12 為采用鑲塊結構成形出的樣件。由圖 12可知,樣件成形質量較好,驗證了采用鑲塊結構具有可行性,比整體式模具結構具有綜合優勢。
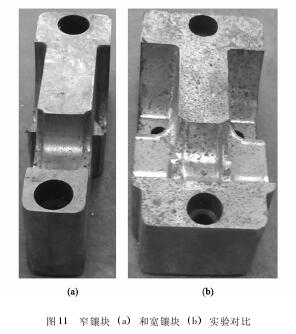
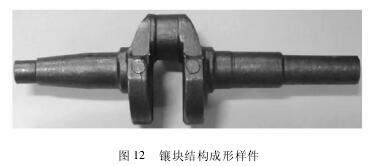
實驗過程中發現,采用窄鑲塊成形時,鍛件連桿頸邊緣表面會產生 “折痕” 缺陷,如圖 13a 所示。而采用寬鑲塊成形時,該處成形較好,如圖13b 所示。根據有限元分析和實驗驗證可知,鑲塊成形桿頸位置處的變形較大,鑲塊壓縮變形,且窄鑲塊在平衡塊內側為接縫位置,綜合影響下,產生了較大的模具間隙,該間隙導致了 “折痕” 缺陷。而寬鑲塊變形較小,且其接縫位置遠離平衡塊一段距離,包含了整個連桿頸和平衡塊部分,避免了“折痕”缺陷的產生。
5 、結論
( 1) 采用鑲塊結構代替整體式模具結構具有可行性,具有加工成本低、壽命高等綜合優勢。
( 2) 寬鑲塊比窄鑲塊具有更高的強度和剛度。
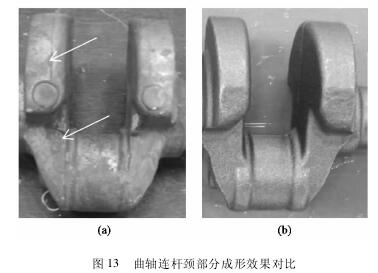
( 3) 實驗中 “折痕”缺陷主要是由于窄鑲塊寬度方向變形較大和模具接縫間隙綜合原因導致,寬鑲塊結構可以有效避免 “折痕”缺陷的產生。
投稿箱:
如果您有機床行業、企業相關新聞稿件發表,或進行資訊合作,歡迎聯系本網編輯部, 郵箱:skjcsc@vip.sina.com
如果您有機床行業、企業相關新聞稿件發表,或進行資訊合作,歡迎聯系本網編輯部, 郵箱:skjcsc@vip.sina.com