立式五軸數控機床機電優化方法研究
2021-5-28 來源:沈陽工業大學電氣 沈陽菲迪亞數控機床 作者:郭志研 夏加寬 時光
摘要: 根據 VMC 立式五軸數控機床結構及其特點,從機械和電氣方面對其進行優化。綜合考慮工藝裝備、裝配工藝、電氣控制、PLC 邏輯及先進的五軸精度檢測方法,提出一套適用于立式五軸數控機床的機電優化方法。通過對比優化前后的性能,證明了其有效性。該研究對國產高端數控機床產品升級具有理論和現實意義。
關鍵詞: 五軸數控機床; 工藝裝備; 機電優化
0 前言
某集團 VMC 系列立式五軸數控機床,是面向航天等領域復雜曲面加工的新一代精密加工設備,該機床采用龍門式框架結構,直線軸為 x、y 和 z; 搖籃式旋轉軸為 A、C,如圖 1 所示。
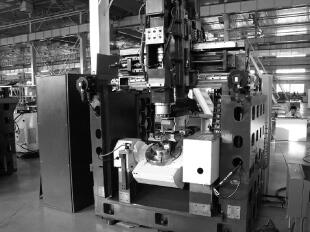
圖 1 立式五軸數控機床
為進一步滿足零件復雜曲面高效高精加工的技術要求,本文作者通過對現有 VMC 五軸數控機床進行機械、電氣全方位優化,使該機床在動靜態性能、加工精度和可靠性等方面達到或超過國際先進水平。
1 、機床現存問題概覽
( 1) 機械裝配方面。
目前,企業在制定裝配工藝規范時主要依賴生產經驗,裝配精度一致性差,可靠性難以保證[1]。對該型號機床采用傳統的機械裝配工藝進行裝配,難以滿足五軸數控機床高精度、復雜曲面加工的性能要求。在裝配階段,影響整機產品可靠性的因素 很 多,各 因 素 件 又 具 有 復 雜 的 交 互 關系[2],主要反映在緊固件選型、公差控制等方面。
此外,在裝配過程中,缺乏必要的工裝檢具,致使各項機械檢測精度得不到保證且工作效率低。裝配工作自由度較大、隨意性較高,差異性的裝配習慣很難保證產品的一致性,使得機械裝配精度處于較低水平。
( 2) 電氣控制方面。
機床電氣柜布局不合理;內部走線凌亂、缺乏統一標準規劃; 機床原始設計時對電磁干擾考慮較少,容易出現不可預期的電磁擾動; 氣動、液動單元空間占用較大,不利于后期保養維護; PLC 控制邏輯冗繁混亂,導致機床外設操控性和安全性難以得到保障。
( 3) 五軸聯動精度檢測方面。
缺乏專業的五軸精度自動化檢測手段和設備,現有的人工檢測手段和方法比較落后,不適應批量生產。機床中應用的搖籃轉臺結構在外形尺寸、定位精度、剛性等方面性能不足,并且控制邏輯混亂,導致旋轉軸與線性軸五軸聯動精度較低、轉臺易出現錯誤報警。
2 、立式五軸數控機床機電優化工作
為解決上文中提到的問題,需要對機床進行全面的機電優化,優化工作主要分為 4 個部分: 優化前的對比試驗、機械部分的優化、電氣部分的優化和HMS 五軸精度測量系統的應用。
2. 1 優化前的對比試驗
在機床進行全面機電優化前對其進行全面的精度檢測,并與同類國際先進產品的精度允差值進行對比,得到如表 1 所示的數據。
表 1 優化前的精度檢測 mm
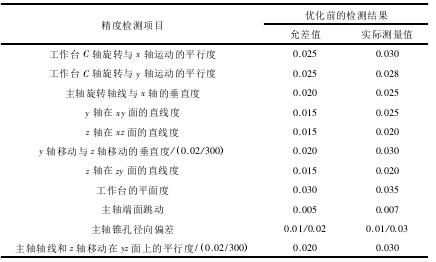
通過對比發現,在優化前的一些機床精度檢測關鍵項目上,該機床距國際先進水平機床產品的精度允差值存在一定超差。機械精度和控制系統無直接關系,如果機械本身的精度不足,則任何先進檢測和控制系統都很難發揮其應有的作用
[3]。
因此,判斷該機床在機械的裝配過程中存在一定缺陷,可以通過優化來進行機械精度的提升,以期在精度上達到或超越同類國際先進機床的水平。
2. 2 機械部分的優化
VMC 立式五軸數控機床機械部分的優化主要包括以下幾個方面: 工藝裝備的改進、裝配工藝優化和高性能轉臺的應用及優化。
2. 2. 1 工藝裝備的改進
原 VMC 機床裝配過程中,適配的工裝夾具較少,對機床裝配、精度測量等方面有較大影響。因此,對現有工裝夾具進行優化并提出新工裝的制作方案和使用方法,新制作了絲杠表座、直線導軌彎板、z 向托板等十余種適配于此機床的新型工裝,如圖 2—4 所示; 改進了軸承孔檢棒等現有工裝,如圖 5 所示。
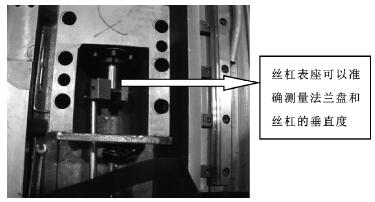
圖 2 絲杠表座
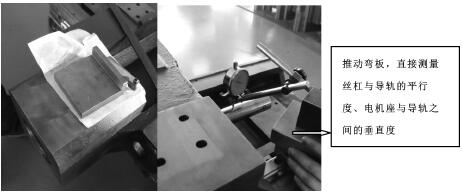
圖 3 直線導軌彎板
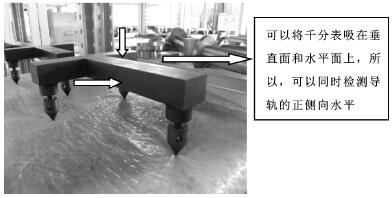
圖 4 z 向托板
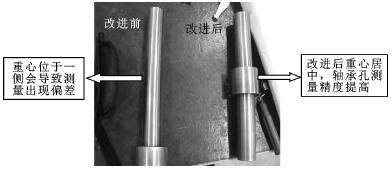
圖 5 軸承孔檢棒
2. 2. 2 機床裝配工藝優化
裝配工藝水平直接決定了數控機床的機械精度、剛性和穩定性。考慮到優化前裝配中存在的各種問題,提出了如下優化方案:
( 1) 將電機座的底面磨薄,加裝調整墊并以此為基準,確保電機與地面的平行度。
( 2) 固定直線導軌的螺栓,加裝碟形墊片,以增加螺釘的剛性。
( 3) 測量立柱 ( y 軸) 兩側的正向、側向、合向精度、合向扭曲,以提高測量精度。
( 4) 簡化氣動柜的結構。
將 A/C 軸的夾緊松開方式變為氣動,減小液壓站的負荷,從而使液壓站的體積大大減小。
( 5) 對各伺服軸的導軌滑塊加裝調整墊,通過研磨調整墊來控制導軌的各項精度。
采用以上優化方案,機床的剛性、可靠性以及各項精度 得 到 提 升,優 化 后 的 精 度 檢 測 結 果 如 表 2所示。
表 2 優化后的精度檢測 mm
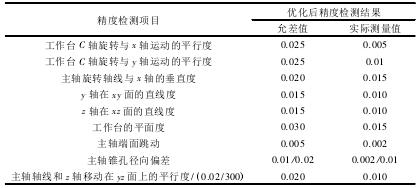
2. 2. 3 高性能轉臺的應用及優化
VMC 機床標配臺灣旭陽轉臺,在剛性、控制精度和穩定性方面略有不足,且控制該轉臺的 PLC 邏輯不夠合理,容易造成機床加工過程中出現過載、通信故障報警等問題。為了全面提高轉臺性能,選用意大利 LCM 高性能轉臺,如圖 6 所示。
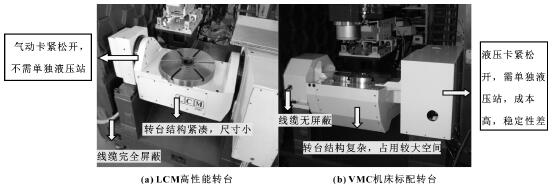
圖 6 2 種轉臺的應用現場
圖中左側為LCM 高性能轉臺,右側為 VMC 機床原標配的轉臺。LCM 轉臺具有剛性好、 響應快、 性能穩定等優點,并且在五軸加工領域被廣泛應用。對控制轉臺動作的PLC 邏輯進行全面優化,優化前后對比如表 3 所示。
表 3 轉臺優化前后對比
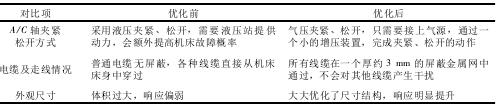
2. 3 電氣部分的優化情況
VMC 機床電氣部分的優化,主要包含以下幾個方面: 電器柜的優化與設計、PLC 邏輯的優化以及HMS 測量系統在五軸精度檢測中的應用。
2. 3. 1 電氣柜的設計
重新對 VMC 機床的電氣柜進行設計,新設計的電氣柜如圖 7 所示。
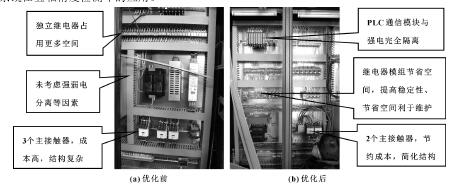
圖 7 電器柜優化前后對比
主要進行了以下改進:
( 1) 強弱電分開,減小了電磁干擾。
( 2) 將電氣圖紙進行標準化處理,為保證機床未來進入歐美市場,將原有的中文圖紙豐富為符合CE 標準的中英文對照圖紙。
( 3) 優化電氣柜結構,將控制星角轉換的接觸器由 3個減小為 2 個,節省了電氣元件,節約了成本,簡化了電路結構。
( 4) 將繼電器組改為繼電器模塊,減小了占用空間,節約成本; 將電氣柜內的元件全部換為符合CE 標準的零部件。
2. 3. 2 PLC 邏輯優化
通過優化完善 PLC 的邏輯,根據氣動液壓結構的改變,增加了更多的邏輯互鎖保護,如表 4 所示。
表 4 PLC 邏輯優化前后對比

2. 3. 3 HMS 系統在五軸精度檢測中的應用
HMS ( Head measure system) 是某公司開發的五軸精度自動檢測工具[4],如圖 8 所示。
相較于傳統的手動五軸精度檢 測 ( 千分表配合 球頭 檢棒人工測量) ,HMS 具有以下優點:
( 1) 手動五軸精度測量依靠人工控制,對操作員技術水平要求高; 而采用 HMS 系統測量五軸精度,是由系統控制來自動完成的,只需要對操作人員進行適當培訓即可。
( 2) 手動測量準備、測量時間長,易產生隨機誤差,效率低; 采用 HMS 系統測量速度快,每測量完一項精度,系統自動糾正誤差,可靠性高。
( 3) 手動測量只能尋找 A/C 軸旋轉中心,不能對 A/C 軸進行旋轉軸的螺距補償。五軸機床做復雜曲面加工,需要對旋轉軸的誤差進行控制,HMS 系統可以對 A/C 軸進行旋轉軸的螺距補償。
( 4) 手動測量時,當轉臺旋轉角度較大時,千分表的誤差會加大,而 HMS 系統的 3 個空間傳感器不會受到轉臺角度的影響,使其精度始終保持穩定。
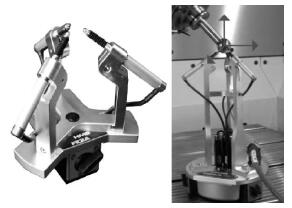
圖 8 HMS 系統
3 、結束語
對現有 VMC 立式五軸數控機床進行機械、電氣方面的優化,從裝配工藝、電氣控制以及零部件選配等方面改進機床的各項性能指標、提升制造水平、提高 VMC 立式五軸數控機床的市場競力。同時,在工作中摸索總結出一套應用于五軸數控機床產品的機電優化方法,為企業高精尖產品的技術升級提供了指導。
投稿箱:
如果您有機床行業、企業相關新聞稿件發表,或進行資訊合作,歡迎聯系本網編輯部, 郵箱:skjcsc@vip.sina.com
如果您有機床行業、企業相關新聞稿件發表,或進行資訊合作,歡迎聯系本網編輯部, 郵箱:skjcsc@vip.sina.com
更多相關信息