某曲軸平衡重凹槽加工技術攻關
2021-8-23 來源:- 作者:-
摘要:針對某大型曲軸生產研制以來,平衡重凹槽加工中的難點問題。根據實際情況對比分析與模擬仿真,采用車銑中心進行空間3D銑削及相位旋轉與補償的方法逐一加工,完成了6組共12個平衡重凹槽的攻關,為類似零件的研制提供了新的思路與工藝方法。
關鍵詞:大型曲軸;配重槽;仿真;空間三維;銑削相位旋轉與補償
0 引 言
曲軸是發動機中的關鍵零件,起著傳遞動力的作用,工作時承受著復雜的交變應力,曲軸的質量直接影響發動機的動力性能和整機使用壽命。在其每一拐徑上的平衡重凹槽裝配平衡重,是為了平衡連桿大頭、連桿軸頸和曲柄等產生的離心力及其力矩,以使發動機平穩運轉,減少主軸頸負荷。平衡重一般有2種類型:第一種平衡重與曲軸連為一體,也就是與曲柄模鍛為一體,設置在曲柄前端,一般用于小型曲軸中;第二種平衡重是單獨設置一平衡塊,用螺栓與曲柄前端面連接,常用于大型曲軸中。某平行重凹槽為空間遞減3D結構,不易加工與測量,且尺寸精度與形位公差要求嚴格,在每拐徑上分布的相位不同,加工數量多、風險高、難度大,直接影響某型柴油機裝配與試驗進度。1 零件結構與材料切削加工性每一零件在加工前都必須對其結構特點、技術要求、材料可切削性能等進行細致分析,找到加工的關鍵環節及難點所在。以根據實際情況選擇機床、刀具及裝夾方法,最終制定工藝路線。
1)零件結構如圖1所示,其結構特點是:零件為大型軸類鍛件,該曲軸的外形尺寸全長為5495 mm,總質量約為5700 kg,軸頸、拐頸外圓尺寸相同157.5 mm,每一拐頸相位相隔120°呈圓周均勻分布共2組6拐。在拐頸的兩邊都有一個拐臂,拐臂上的凹槽用于掛載平衡重。其工藝參
數要求:R40、R5、120°、30°、20°、159±0.2、83.5、45、Ra0.8、Ra3.2。
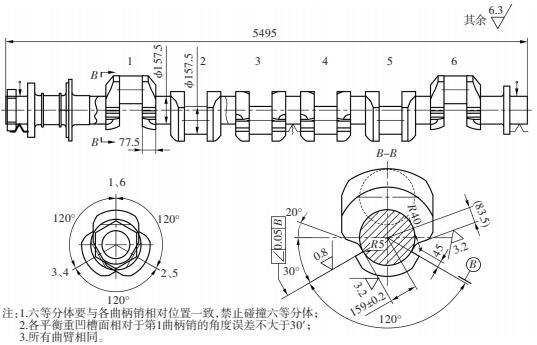
圖 1 某曲軸平衡重加工示意圖
2)零件材料為42GrMo,硬度41~45 HRC屬于難加工材料。由于被加工零件硬度較高,刀具與零件在切削區摩擦因數增大,切削過程中產生的熱量大、溫度高,使硬化加劇。工件材料強度、硬度不斷提高,切削力增大,致使加工刀具磨損較快,機床消耗功率過大[1]。
3)零件加工容差及檢測方法。需要測量相對于基準B面的誤差0.05°,表面粗糙度Ra0.8 μm,以及R40、R5、20°。基于加工后的檢測要制作專用角度卡規以測量0.05°誤差,R40、R5、20°可用樣板測量,以照光間隙測量是否合格。
2 、加工工藝性分析
1)該凹槽不在同一加工平面內為空間尺寸,加工斜面、圓弧、底邊、直角邊,需連續變換相位,形位公差、線性尺寸(159±0.2、83.5)、表面質量要求高(Ra3.2 μm、Ra0.8 μm)。
2)42×R5圓弧面銑刀、D45×R0.8立銑刀加工時刀桿受到凹槽120×51×154.9尺寸限制,直徑(28)小、長度(126)大,造成剛性差、強度低,切削時易產生振動 。
3)整個凹槽加工中,材料不易切削且去除率高,致刀具散熱條件差,切削溫度升高,使刀具的耐用度降低[2]。試切時需反復嘗試改變刀路、修改切削參數、更換切削刀片,以降低切削溫度,提高刀具耐磨性。
4)R40圓弧與底面和斜面相切時,42×R5圓弧面銑刀具路徑需空間三軸連續多次圓弧移動,程序編制難度較大。
5)某曲軸全長5495 mm,要求相位誤差不大于30′。每加工一組先要對機床進行檢測,主軸徑距凹槽直角面直線距離159 mm。記錄誤差值做出反方向差值補償。
3、 工藝方案
1)方案1。某曲軸粗、精銑凹槽在落地FPT鏜銑床加工,其加工原理是:把零件定位在V形架上并夾緊,利用六等分體手動保證相位角度,銑頭旋轉后逐一加工。此方案的缺點是加工誤差大、效率低。手動旋轉相位時,松開壓緊的曲軸后慢慢轉動,待端面固定的六等分體大致水平時,利用百分表找平曲臂平面在0.03 mm內,壓緊曲軸加工凹槽豎直部分與R40圓角。然后旋轉銑頭加工20°斜面與R40相切,同時保證83.5 mm尺寸。一組加工完后,再次手動旋轉六等分體及銑頭120°,銑削另一組平衡重凹槽。以此類推全部加工完成。在每組銑削中需手動找正曲軸曲臂平面,費時費力,且存在銑頭旋轉與找正疊加誤差。此方案加工效率低、尺寸誤差大,質量與研制節點難以保證。
2)方案2。車間現有的HTM1251000車銑復合加工中心(如圖2)是沈陽機床廠生產的,目前是國內最大的車銑復合加工中心。該機床采用西門子840D數控系統,配有左右兩個旋軸B﹑C和X﹑Y﹑Z三個直角坐標,左旋轉頭為主頭用于車﹑銑加工,通過左右轉頭使相位自動旋轉,以有效保證120°相位角,同時在加工中利用相位的變換,縮短刀具與刀柄的長度,減少刀具費用并提高刀具剛度,有效地對側臂與斜面進行精加工,同時對于不同拐徑上的凹槽尺寸一致性好,加工精度高、質量穩定、效率高。
結合工藝要求經對比分析,充分利用車間現有技術、設備、刀具,確定為在HTM1251000車銑復合加工中心上加工。先粗銑去除大部分余量,二次開粗進行半精加工,最后利用相位角的變換進行光整加工。粗、半精、精加工分步進行,使得整個生產過程精確、高效、可靠。
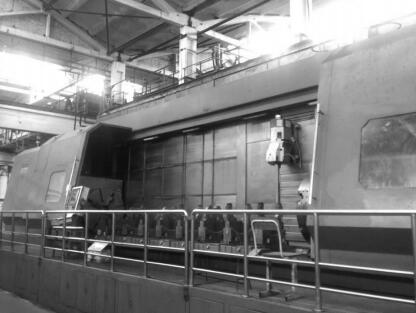
圖2 HTM1251000車銑復合中心示意圖
3.1 刀具選用
平衡重凹槽空間材料去除率大、形位公差小、表面質量要求高,相誤差不大于30′。這就要求在刀具選擇上,既要高質量又要高效率。通過對零件圖樣尺寸精度、材料等綜合分析,選用數控機夾刀具進行切削[3]。粗、精銑選用42×R5銑刀,精銑120°側面選用25平底立銑刀,精銑20°斜面選用50平底立銑刀。某曲軸粗、精銑單個曲臂平衡重凹槽面刀具選用表如表1所示。
表1 某曲軸粗、精銑單個曲臂平衡重凹槽面刀具選用表
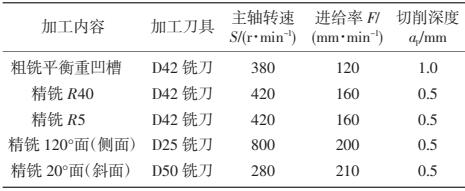
3.2 數控程序編制
數控程序的編制包括:三維模型的建立、粗精加工刀具切削參數的設定、模擬仿真、程序的導出。本程序通過以下步驟來加工整個平衡重凹槽。
1)根據圖樣要求建立三維模型。編寫程序時所涉及的刀具位置軌跡,需在三維軟件中做出曲軸平衡重凹槽數字模型。打開NX軟件,進入XOY平面建立草圖,繪制B-B剖視圖截面,拉伸出實體即可。
2)粗銑平衡重凹槽。用 42×R5銑刀進行3D空間凹槽開粗,單邊預留1 mm余量。由于材料不易加工,且要從實心處去除材料,材料去除率高。在開粗時要選用刀桿較短的刀柄,以防止切削中的振動,在切削過程中加注乳化液,從而降低切削區的溫度,以減少工件變形、保持刀具的硬度和尺寸,同時利于切屑的排出,保證切削順暢不被卡住。切削深度為1 mm,主軸轉速為380
r/min,切削速度為120 mm/min,逼近速度為1000 mm/min,進刀速度為100mm/min、移刀速度為1000 mm/min[4]。
3)精銑R40。粗加工后大體的形狀已加工完成,對于根部大圓角R40,用42×R5精銑刀具進行光整加工,采用擬合逐步逼近的方法。為保證表面質量,通過提高轉速、降低進給量、減小步距來進行精加工,且在加工中選擇步距應用在部件上,以保證加工刀路在零件上的均勻。
4)精銑R5。用42×R5精銑刀精銑R5,由于刀具圓角半徑與平衡重凹槽根部相同,故順銑一刀完成精銑加工。在加工中注意與R40圓角過渡接刀光滑。
5)精銑 120°側面、20°斜面。精加工操作,同時旋轉B、C軸,使120°側面與主軸平行,用25立銑刀精銑出側面并與底部R5相切。滿足圖樣Ra0.8 μm表面粗糙度和角度誤差0.05°。同理,相位角轉過20°,用50立銑刀精銑出斜面與R40圓弧另一側相切。保證尺寸83.5 mm、表面粗糙度Ra3.2 μm。
6)加工前的數字化驗證。曲軸屬大型關鍵件,加工要求高、研制風險大。為確保正確無誤,要進行3D模擬仿真加工與試件實操加工[3]。為此我們制定了《曲軸平衡重凹槽三維模型與仿真模擬加工方案》,用來提前進行數字化模擬驗證,來進一步確定方案的可行性與程序的正確性,以保證萬無一失。加工模擬仿真如圖3所示。
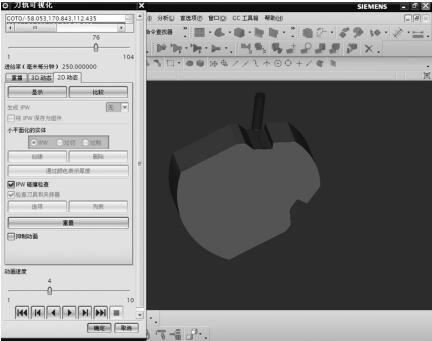
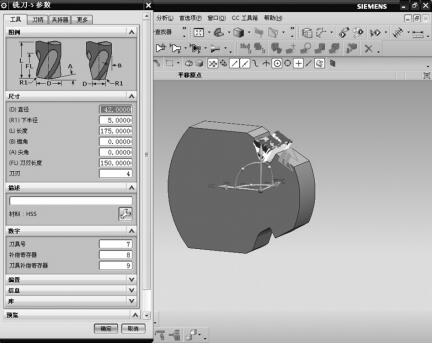
圖3 加工模擬仿真圖
7) 制作后處理導出數控程序。由于數控機床種類繁多,控制系統多樣,每一機床的NC代碼廠家自定義的指令各有不同,因此刀軌數據輸出,必須經過定制的后處理生成機床可識別的指令。編寫程序時所涉及的刀軌數據,需在三維軟件中做出曲軸數字模型、建立曲軸中心仿真系統模塊、配置刀具、選擇加工策略,生成刀路、后置處理,輸出程序。最終編輯為機床用數控程序。同時結合刀具、機床、零件計算理論切削參數。程序輸出示意圖如圖4
所示。
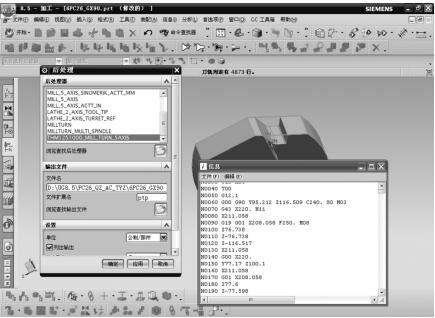
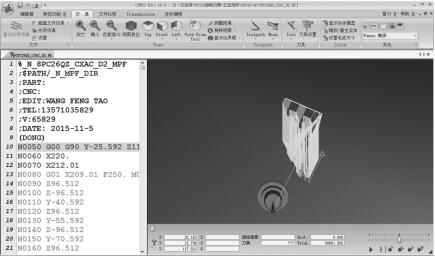
圖4 程序輸出示意圖
4 、加工后的平衡重凹槽與專檢結果
由于加工前準備充分,成品某曲軸平衡重在首次加工過程中,切削抗力小、刀具運行平穩、機床載荷均勻、相位旋轉準確,加工十分順利。凹槽加工尺寸與表面質量好。測量結果滿足工藝要求,僅用了1個班次就完成了首個平衡重凹槽的加工。加工后的平衡重凹槽如圖5所示。
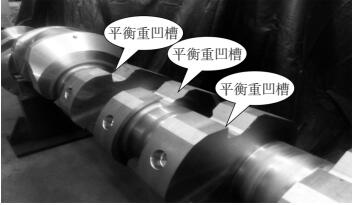
圖5 加工后的平衡重凹槽圖
5、結 語
通過對平衡重加工工藝的試驗和技術攻關。采用數字化驗證及對比加工方法進行研究后,保證了最佳方法在實際生產中的有效應用,為后續生產大型、特型零件的首件調試提供了新的工藝方法,且數字化驗證較原有試加工驗證更具先進性和科學性,能有效排除加工質量風險、優化加工程序、提高生產效率,并確保一次加工合格,縮短產品研制周期。
作者:王逢濤1,童勇智1,金許濤1,陳浩安1,田永維2
來源:1.陜西柴油機重工有限責任公司, 2.駐咸陽地區軍事代表
投稿箱:
如果您有機床行業、企業相關新聞稿件發表,或進行資訊合作,歡迎聯系本網編輯部, 郵箱:skjcsc@vip.sina.com
如果您有機床行業、企業相關新聞稿件發表,或進行資訊合作,歡迎聯系本網編輯部, 郵箱:skjcsc@vip.sina.com
更多相關信息