基于ANSYS 的激光選區熔化裝備進給傳動系統結構優化設計
2017-2-15 來源:南京理工大學機械工程學院 作者:崔祎赟, 劉婷婷, 廖文和, 張長東
摘要: 成形缸的進給傳動系統作為激光選區熔化裝備的主要組成部分, 其靜動態性能是影響激光選區熔化鋪粉精度的關鍵因素, 而進給傳動系統的結構直接影響靜動態特性的好壞, 因此有必要對其進行設計與分析。以有限元軟件ANSYS 為工具, 采用有限元的方法對進給傳動系統進行靜動態特性分析, 仿真分析了單絲桿有無導柱的支承方式以及滾珠絲桿的安裝位置對進給傳動系統的影響。結果表明: 有導柱支撐并且滾珠絲桿安裝在成形缸正下方時, 系統的靜動態性能最佳。此外, 在工藝方面研究了鋪粉壓力對該進給系統的影響。
關鍵詞: 激光選區熔化; ANSYS; 成形缸; 傳動系統; 絲桿
0.前言
激光選區熔化(Selective Laser Melting, SLM)技術基于離散-堆積原理, 它利用激光掃描產生的熱量快速并完全熔化粉末材料, 可以直接根據3D CAD模型來制造復雜形狀物體[1-3] 。其原理如圖1 所示。
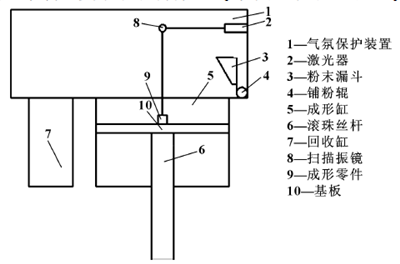
圖1 激光選區熔化裝備結構示意圖
鋪粉輥將粉末漏斗中的粉末材料以一定厚度(約30~50 μm) 鋪在成形缸上方的粉床上, 一次鋪粉完成后激光器通過掃描振鏡在氣氛保護裝置下對粉末進行直接熔化, 該粉層熔化加工完成后, 成形缸中的基板在滾珠絲桿的帶動下相應下降一個粉層厚度的高度, 不斷重復這一過程, 直至成形零件加工成形[4] 。
成形缸進給傳動系統是SLM 激光選區熔化成形設備中的關鍵部件, 用于控制加工過程中成形缸的移動量。在成形缸中, 成形零件固結在基板上, 每次熔化完一層粉末后, 成形零件跟隨基板在成形缸中下降一個粉層厚度的位移。鋪粉精度是影響成形零件質量的重要因素之一[4] , 而每次鋪粉的厚度取決于成形缸中成形零件和基板的下降位移量, 鋪粉的厚度精度又取決于傳動系統驅動基板的下降位移精度, 因此, 優化設計成形缸進給傳動系統結構, 提高系統工作精度, 是激光選區熔化增材制造裝備研制與改進過程中需要考慮的關鍵問題[5] 。
對于成形缸進給傳動系統的設計研究是激光選區熔化增材制造裝備研制過程中的重要環節, 國內外相關領域內的學者和機構為了滿足增材制造實驗需求及商業化裝備的研制對成形缸進給傳動設計進行了相關研究。其中, 陳光霞等[6-7] 在成形缸活塞運動中設計了導向裝置來減少活塞上下運動的擺動誤差和轉動誤差, 同時分析了鋪粉裝置的誤差來源, 提出了若干控制和消除誤差的方法; 黨新安等[4-5] 研究了分別從振動特性和傳動系統動力參數計算等方面來提高鋪粉精度要求。除此之外, 史玉升等[8] 于2005 年研制成功SLM 設備樣機, 目前, 華中科技大學開發了兩套SLM 成形設備: HRPM-Ⅰ和HRPM-Ⅱ、華南理工大學的研究人員激光加工實驗室分別于2004 年、2007年研發了DiMetal-240、DiMetal-280, 并于2012 年推出商用化設備DiMetal-100[9] 。德國EOS 公司的研究人員在研發M270、M280、M290 等金屬成形設備[10]的過程中, 對于成形缸進給傳動系統的設計均進行過相關研究。
本文作者以激光選區熔化裝備成形缸進給傳動系統的優化設計、提高系統工作精度為目標, 利用ANSYS有限元分析軟件構建進給傳動系統的仿真模型,對進給傳動系統進行靜動態分析, 并且模擬不同壓力下鋪粉輥的鋪粉過程對成形缸進給傳動系統的影響。基于仿真分析結果, 優化、改進成形缸進給傳動系統結構, 為自主激光選區熔化增材制造裝備研制提供相應部件的設計方案。
1.成形缸進給傳動系統建模
成形缸進給傳動系統主要由成形缸體、基板、活塞、固定板、導柱、滾珠絲桿副、支撐板和底板等組件構成成。文中采用Pro/E 軟件繪制進給傳動系統的三維CAD 模型如圖2 所示。在保證分析結果的精度和可靠性的前提下, 為了提高有限元分析的計算速度, 避免不必要的計算量, 對模型進行簡化[11] , 主要包括:以等直徑光桿代替滾珠絲桿副; 去除模型的倒圓倒角以及基板、固定板、支撐板和底板等結構上的小螺栓孔等小特征區域[12] 。
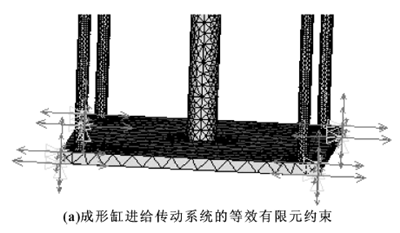
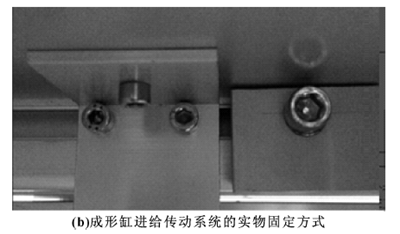
圖4 成形缸進給傳動系統的固定方式
三維模型建立之后, 導入有限元軟件ANSYS 中進行分析處理, 整個結構實體單元類型選擇Solid185單元, 采用自由劃分和人工干預相結合進行網格劃分[13] 。由于組成成形缸進給傳動系統的各個零部件在穩態下保持相對靜止, 在不考慮結合面動態參數特性的情況下, 各零部件之間采用剛性聯接[11] 。有限元模型如圖3 所示。
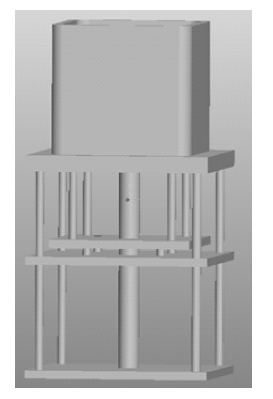
圖2 進給傳動系統Pro/E 建模圖
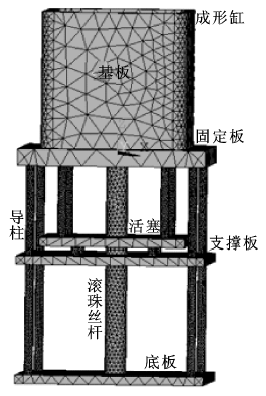
圖3 進給傳動系統有限元建模圖
設定成形缸進給傳動系統滾珠絲桿副的螺母運動方向為設備的Z 軸(向上為正方向), 鋪粉輥的直線運動方向為X 軸(向右為正方向), 再根據笛卡爾坐標系即可確定設備的Y 軸方向。
文中成形缸進給傳動中的滾珠絲桿和導柱的頂部和底部通過螺母座分別固定在固定板和底板上, 通過ANSYS 有限元軟件布爾運算的“add” 操作將成形缸進給傳動系統“加” 為一個整體; 成形缸的底板利用螺栓固定連接在設備鋁合金總框架上, 因此ANSYS有限元軟件分析的等效約束是: 在底板頂點處建立節點, 約束是這些節點X、Y、Z 3 個方向上的自由度, 固定約束如圖4 所示。成形缸設計尺寸為150mm×150 mm×100 mm, 最大的承載鈷鉻合金粉末質量約為20 kg, 等效于在ANSYS 分析中, 在基板表面沿Z 軸負方向施加104 Pa 的壓強。
模型中除了絲桿材料是軸承鋼GCr15 和基板材料是不銹鋼304 之外, 其余材料為鋁合金3003。材料參數見表1。
表1 材料參數
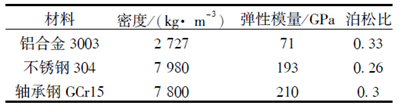
2.導柱對成形缸進給傳動系統的影響
成形缸中采用滾珠絲桿在豎直方向上的上下直線運動帶動基板的直線運動, 導柱在裝置中主要作用是: (1) 支撐作用。導柱安裝在固定板上, 對成形缸體有一定的支撐作用; (2) 導向作用, 使支撐板在滾珠絲桿的作用下沿導柱上下運動以實現基板的上下運動[6] 。下面探討有無導柱對進給傳動系統運行精度的影響。文中設計滾珠絲桿的頂部固連在固定板中心位置, 基于ANSYS 有限元平臺分別對固定板4 個角有導柱和無導柱兩種設計進行靜動態分析。
2.1有無導柱的兩種進給傳動系統靜力學分析
靜力分析顯示: 有導柱支撐時, 成形缸進給傳動系統的總變形量最大值為3暢45 μm; 最大值位于基板中心位置, 最小值位于施加約束的底板的頂點上; 成形缸進給傳動3 個方向中變形最大為Z 方向, 如圖5 (a)所示。無導柱時, 總變形量最大值為15暢1 μm,如圖5 (b) 所示, 該變形量是有導柱支撐結構的近5 倍; 一般而言, 激光選區熔化過程成形缸進給量為一個粉層厚度, 約30~50 μm, 而無導柱支撐結構的最大總變形量接近粉層厚度的一半, 誤差較大; 相比而言, 有導柱支撐結構增加了傳動進給沿軸向的靜剛度,能減少最大總變形量, 從而提高加工中的進給精度。
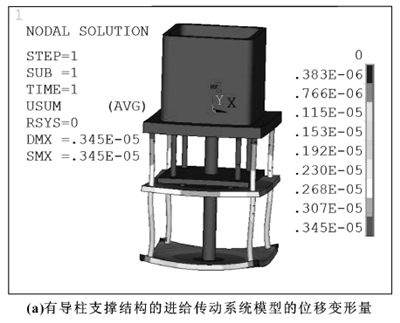
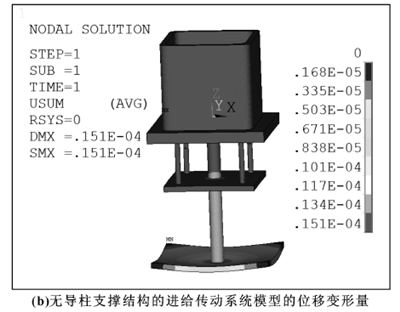
圖5 有無導柱支撐結構的兩種進給傳動系統模型的位移變形量
2.2 有無導柱兩種進給傳動系統的模態分析
在ANSYS 中采用BlockLanczos 模態提取法對有無導柱支撐這兩種進給傳動系統進行模態分析, 提取前10 階固有頻率, 一般而言, 低階固有頻率起主導作用, 高階固有頻率在通常情況下是無法激發的。圖6 為該兩種傳動進給系統前10 階模態頻率對比圖。
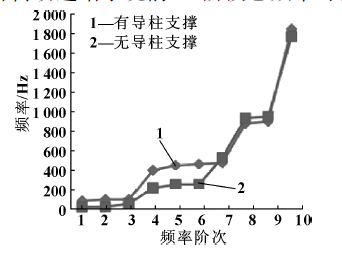
圖6 有無導柱兩種進給傳動系統模型的模態頻率對比圖
可知: 當有導柱支撐時, 其模態頻率比沒有導柱支撐時高, 因而在質量相近情況下, 有導柱的進給傳動系統剛度更大。除此之外, 固有頻率的提高能在一該傳動進給系統的動態性能。
3.絲桿的安裝位置對成形缸進給傳動系統的影響
激光選區熔化成形技術通常采用粒徑30 μm 左右的超細粉末為原材料[14] , 在成形缸進給傳動過程中, 滾珠絲桿在豎直方向上帶動基板做上下直線運動, 從而推動成形缸中的成形零件和成形缸內微細粉末上下運動, 因此, 在運行過程中不免有粉末從基板與成形缸內壁的間隙中泄漏, 從而透過縫隙下落。然而, 若滾珠絲桿副安裝在成形缸正下方, 則微細粉末可能會進入滾珠絲桿, 使得滾珠絲桿磨損, 導致滾珠絲桿的運行精度降低, 從而影響成形缸進給精度。因此, 文中設計滾珠絲桿副兩種不同的安裝位置(滾珠絲桿副安裝在成形缸正下方與右側), 基于ANSYS有限元軟件進行靜動態分析, 如第1 節所述在基板表面沿Z 軸負方向施加104 Pa 的壓強, 在底板頂點處建立節點, 約束這些節點X、Y、Z 3 個方向上的自由度。
3.1 滾珠絲桿不同安裝位置下兩種進給傳動系統模型的靜力學分析
靜力分析顯示: 絲桿安裝在成形缸右側位置時,成形缸進給傳動系統的總變形量最大值為7暢06 μm;最大值位于成形缸左側頂部位置, 約為絲桿安裝在正下方位置時變形量最大值的兩倍, 如圖7 (b) 所示;同時, 依據表2 以及圖7 (c) — (h) 所示。
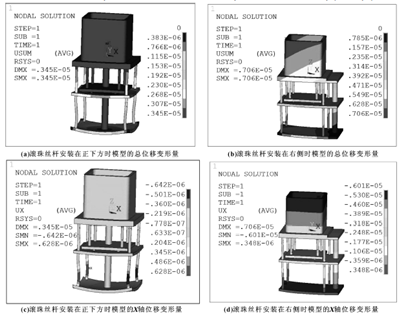
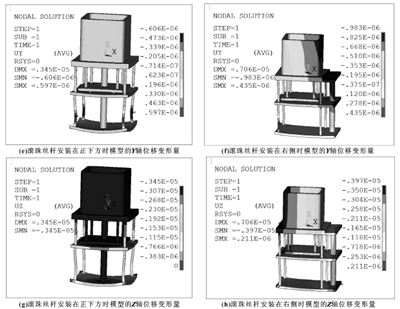
圖7 滾珠絲桿不同安裝位置時兩種模型的位移變形量對比圖
絲桿安裝在成形缸正下方時, X、Y 軸方向的位移變形量幾乎相同, 節點位移的最大值和最小值數值相等, 符號相反, 變形量集中在導柱下半部分, 導柱產生小量彎曲變形, 基板以及成形零件的在X、Y 軸方向上的位移變形量最小; 然而若使用絲桿在成形缸右側的安裝方式時候, X、Y、Z 3 個方向上節點位移最大值和最小值數值相差較大, 存在傾斜, 這使得整個成形缸進給傳動系統傾斜, 從而可能導致成形零件變形或者翹曲。
表2 滾珠絲桿不同安裝位置下兩種進給傳動系統模型總位移以及X、Y、Z 3 個方向位移
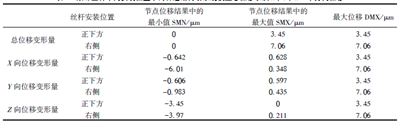
3.2 滾珠絲桿不同安裝位置下兩種進給傳動系統模型的模態分析
為了提取兩系統的固有頻率和各階振型, 在ANSYS中采用BlockLanczos 模態提取法對它們進行模態分析, 考慮到系統低階模態主要表現為X、Y、Z 3 個方向的振動以及扭轉變形[13] , 高階固有頻率很少出現,故提取前10 階固有頻率, 見表3。相同振型下, 滾珠絲桿不同安裝位置下兩種進給傳動系統固有頻率最大相差767 Hz, 滾珠絲桿安裝在成形缸正下方比安裝在右側固有頻率提高了71暢2%, 該頻率下, 系統沿Z 軸上下振動; 其次, 在第一階次時, 安裝在正下方的位置比右側提高了53暢9%, 該頻率下, 成形缸以及活塞等系統的上半部分繞Z 軸扭轉變形; 在第4 階次時,安裝在正下方的位置比右側提高了41暢8%, 該頻率下,活塞繞Z 軸扭轉變形; 而Z 軸方向為成形缸的進給方向, 提高Z 方向的精度可直接減少成形缸進給誤差。
表3 滾珠絲桿不同安裝位置下兩種進給傳動系統模型在同一振型下的固有頻率值
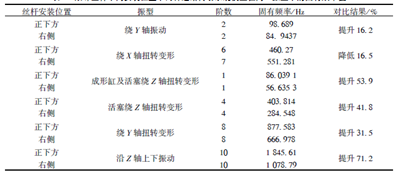
基于第3暢1 節靜力學分析和第3暢2 節模態分析的結果可知: 滾珠絲桿安裝在成形缸正下方位置可以避免系統傾斜變形, 并且可以減少總位移變形量; 同時可以較好的提升進給傳動系統沿絲桿軸向的動剛度,這有利于提高進給傳動系統的精度和負載能力。與滾珠絲桿安裝在正下方的方式相比, 滾珠絲桿安裝在右側的方式雖然可以避免粉末污染磨損絲桿, 但是此安裝方式的靜動態性能不好, 特別影響進給傳動系統在Z 軸的運行精度, 綜上所述采用滾珠絲桿安裝在成形缸正下方的方式, 該方式可以提高Z 軸精度, 從而提高成形缸的進給精度, 同時為了避免粉末侵入滾珠絲桿, 采用防塵密封圈及防塵裝置。
4.鋪粉輥不同鋪粉壓力對成形缸進給傳動系統的影響
激光選區熔化技術所需的鋪粉過程采用鋪粉輥將粉末均勻地鋪覆在成形缸上方的粉床上。粉末不像致密體那樣具有固定的形狀, 其表現為與液體相似的流動性; 由于顆粒之間相對移動時存在摩擦, 粉末的流動性又很有限, 粉末在松散堆集時顆粒之間存在大量的孔隙, 松散粉末的密度只有致密體的20% ~50%[15] , 而粉層的粉末密度大小直接影響成形零件的密度, 從而影響零件的強度、收縮和翹曲變形。為了鋪出具有較高致密度的粉末層, 鋪粉輥在水平運動的同時, 對粉末層施加向下的壓力使之壓實, 這也對成形缸進給傳動系統產生了一定影響。鋪粉輥的受力分析如下: 如圖8 所示, 鋪粉輥對粉末產生正壓力F的作用, 其分力F1 推動粉末向前運動, 分力F2 對粉末起到壓實的作用[16] 。而正壓力F 與鋪粉輥的質量有關, 因此鋪粉輥的質量大小決定分力F2的大小。文中以有導柱支撐并且滾珠絲桿安裝在成形缸正下方的鋪粉進給傳動系統模型為例, 設計鋪粉輥的直徑為40 mm, 長約為170 mm, 材料為不銹鋼304 (鋪粉輥的重力約為15 N)。在鋪粉輥對粉末施加壓力下, 研究鋪粉輥從右向左鋪粉過程中成形缸進給傳動系統的變形, 并且研究不同壓力大小(分別施加1、2、4、6、8、10 N 的壓力) 對成形缸進給傳動系統的變形影響。
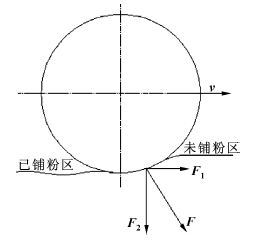
圖8 鋪粉輥鋪粉時粉末受力示意圖
在ANSYS 有限元中, 鋪粉輥對粉末施加壓力等效于對成形缸上表面施加一項移動載荷, 鋪粉過程中圓柱形鋪粉輥與成形缸成線接觸, 等效成對成形缸進給系統施加一個移動的線載荷, 因此每次只需將載荷施加在規定線單元上的各個節點處, 而采用GUI 方式會占用大量時間, 利用APDL 語言可以加快分析過程中的加載和求解[17] 。設置每次載荷步結束時間為1, 載荷步數為5, 從成形缸最右端每隔1 s 依次向左移動到作用規定的節點上, 直到載荷移動到最左端的規定節點位置, 一次鋪粉運動完成。移動載荷命令流如下:
TIME,1
NSUBST,5,2
F,725,726,727,728,729,730,731,732,FY,-1
LSWRITE,1
TIME,2
FDELE,All,ALL
F,745,746,747,748,749,750,751,752,FY,-1.......
以此循環, 完成鋪粉壓力為1 N 下的一次鋪粉過程, 而后改變壓力為2、4、6、8、10 N, 利用有限元ANSYS 分析每次鋪粉過程成形缸進給傳動系統的變形量。
4.1 成形缸進給傳動系統一次鋪粉過程的變形
施加的鋪粉壓力使成形缸產生Z 軸負方向的位移變形, 對于X、Y 軸可忽略不計。由于成形缸傳動進給系統結構對稱, 在鋪粉輥從右向左運動過程中, 該系統的變形成對稱分布。如圖9 所示, 以鋪粉壓力1 N 為例, 分析一次鋪粉過程內成形缸進給傳動系統的變形。
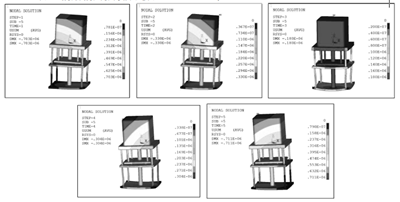
圖9 鋪粉壓力1 N 時各載荷步下成形缸進給傳動系統變形圖
在中間位置時即載荷步3, 整個系統的最大變形量最小, 系統變形呈整體下降趨勢。各載荷步下最大變形量的最大值處在成形缸最右端和最左端即載荷步1、5, 下降變形最大, 約是載荷步3 處變形的4 倍。鋪粉過程, 成形缸傳動系統的變形處在彈性階段, 呈橢圓體狀; 鋪粉結束時, 恢復原狀, 因此鋪覆在左右兩端的粉末最多, 并且向中間位置處逐漸減少, 粉層呈不均勻分布, 從而可能使得成形零件產生翹曲等變形。
4.2 不同鋪粉壓力對成形缸進給傳動系統的變形影響
結果表明: 在鋪粉壓力10 N 以下時, 整個鋪粉過程, 成形缸進給傳動系統的變形趨勢一致, 變形處于彈性階段; 隨著壓力的增加, 各個載荷步的最大變形量成線性增加如表4。如圖10, 鋪粉壓力越小, 成形缸進給傳動系統的變形越小, 鋪覆在成形缸粉床上的粉層越均勻。當鋪粉壓力為4 N, 鋪粉過程中變形量的差值為2.13 μm, 即左右兩端高于中心位置2.13μm, 該數值近似于每次鋪粉厚度(約50 μm) 的4.26%; 若增大鋪粉壓力至10 N, 則變形差值增大為5.31 μm, 接近每次鋪粉厚度( 約50 μm) 的10.62%, 誤差較大; 若繼續增大壓力時, 變形差值也相應增大, 則翹曲變形更為嚴重, 因此為了保證誤差控制在10%以內, 則在本裝置設計的成型實驗中,鋪粉壓力應小于10 N。
表4 不同壓力各載荷步下進給傳動系統的最大變形量 μm

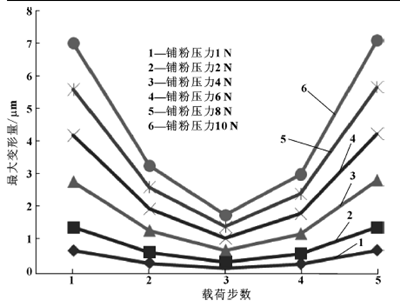
圖10 不同壓力各載荷步下成形缸進給傳動系統的最大變形量折線圖
5.結論
(1) 由靜態分析結果和模態分析對比結果可知,有導柱支撐的進給傳動系統軸向靜態剛度相比無導柱時提升了77%, 同時也提高了系統固有頻率, 在一定程度上避免共振的產生。這有利于提高系統的負載能力和使用壽命。
(2) 滾珠絲桿在成形缸正下方的安裝方式使得該進給傳動系統的靜態剛度相比一側安裝提升了51%, 也避免了系統傾斜, 同時提高進給傳動系統沿絲桿軸向的動剛度, 這有利于提高進給傳動系統的精度和負載能力。
(3) 鋪粉壓力在10 N 以下時, 成形缸進給傳動系統處于彈性變形階段, 不同壓力下鋪粉過程的變形趨勢一致; 當鋪粉壓力超過10 N, 鋪覆的粉層的中心位置與兩端的高度差值大于每次鋪粉厚度的10.62%, 若繼續增加壓力, 粉層中心與兩端高度差越大, 則翹曲變形加重。
投稿箱:
如果您有機床行業、企業相關新聞稿件發表,或進行資訊合作,歡迎聯系本網編輯部, 郵箱:skjcsc@vip.sina.com
如果您有機床行業、企業相關新聞稿件發表,或進行資訊合作,歡迎聯系本網編輯部, 郵箱:skjcsc@vip.sina.com
更多相關信息