高效加工氣缸蓋電熱塞孔的工藝安排
2018-3-27 來源: 山東華源萊動內燃機有限公司 作者:姜興國,冷長庚
摘要: 本文通過對柴油機氣缸蓋電熱塞孔的結構分析及加工工藝改進,介紹了在批量生產時采用組合機床、組合刀具高效加工氣缸蓋電熱塞孔的工藝。
關鍵詞: 電熱塞孔; 組合機床; 復合刀具
引 言
柴油機氣缸蓋電熱塞孔受氣缸蓋整體結構、布局的影響,通常為較復雜的多參數的深孔結構,電熱塞孔與發動機燃燒室相通,其密封性能直接影響發動機整機的性能,為此,加工工藝的合理性直接影響電熱塞孔的加工精度和效率。
某型柴油機氣缸蓋電熱塞孔的結構如圖 1 所示: 角度為復合角度( 28°,15°) 、孔徑為復合孔徑( M8 × 1,Ф7,Ф4. 5) 、孔深為深孔( 89mm) ,其中 Ф7孔的底端為密封面,電熱塞孔的結構復雜,屬于深孔加工,加工有一定難度。
在產品試制時,氣缸蓋電熱塞孔是安排在加工中心上完成的。加工精度雖然能夠保證產品設計圖紙要求,但生產效率低下,嚴重制約產能的提高。為此應在批量生產時探討,采用高效加工氣缸蓋電熱塞孔的工藝安排.
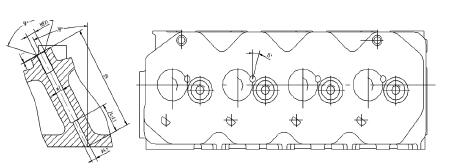
圖 1 4TD60 型柴油機氣缸蓋電熱塞孔結構
1 、用于批量生產的高效加工氣缸蓋電熱塞
孔的工藝批量生產時,通過深入分析論證,確定采用多軸組合機床與復合刀具加工的工藝方案進行氣缸蓋電熱塞孔的加工,具體內容如下:按照試制時加工中心安排的工藝流程,需要五臺組合機床,通過對刀具優化,采用了復合刀具,合并了加工工步,可以用三臺組合機床完成電熱塞孔加工,從而減少了組合機床設備的資金投入。
為保證氣缸蓋電熱塞孔的位置加工精度,在第一臺組合機床設計時,采用滑動導套,使其刀具的導向端面盡量靠近加工平面。
通過油缸,拉塊帶動滑套運動,當液壓插銷發出指令,帶動滑套前送,進給滑臺工進,加工完成,進給滑臺退回,滑套退回。如圖 2 所示。
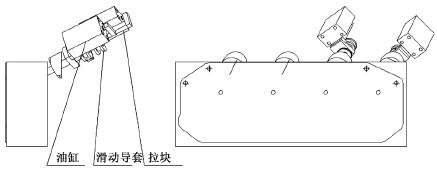
圖 2 組合機床示意圖
第一臺組合機床動作循環過程: 將氣缸蓋推入機床夾具中→按下啟動開關→定位銷油缸與滑動導套油缸同時動作,完成工件定位與滑動導套移動靠近加工面→定位完成后發出指令,夾緊油缸動作夾緊工件→夾緊完成后發出指令,進給滑臺工進,加工完成→加工完成后發出指令,進給滑臺退回→滑臺退回后發出指令,定位銷油缸與滑動導套油缸同時動作,完成工件定位銷退回與滑動導套移退回→將工件推出夾具,進入下一個工作循環。
氣缸蓋電熱塞孔在第一臺組合機床夾具中的位置是孔口朝斜上方向,鉆孔后部分鐵屑會留在電熱塞孔內,為防止后續鉆孔及锪端面工序孔內鐵屑累積引起斷刀具問題的發生,在第一臺組合機床與第二臺組合機床之間安排了鉆孔后的鐵屑清理,用風吹凈孔內鐵屑。
在第二臺組合機床采用了 12×7 ×45 復合刀具,一次加工完成孔口倒角、锪平7 臺階面、鉆 45 孔。同時為減少刀具的浪費,倒角刀與復合鉆采用分體結構,在復合鉆或倒角刀磨鈍時單獨更換,避免了整體更換刀具的浪費,刀具簡圖如圖 3所示。
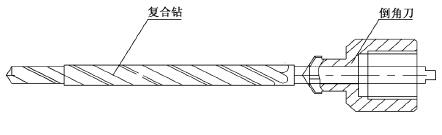
圖 3 刀具簡圖
2 、效果分析
通過以上加工工藝安排,機床工裝,刀具的設計改進,減少了生產工序,提高了加工效率,正常需要五臺設備完成的工序,優化后只需要三臺設備,最大限度的減少了設備數量和投資。同時每臺設備加工的生產節拍≤2. 1 分鐘( 含工件上下料時間) ,并在組合機床設計中,復合了另一面上大多數孔的加工,生產效率比加工中心設備提高了幾十倍,最大限度的降低了單件加工成本。
3 、小 結
對于氣缸蓋電熱塞孔的加工,產品試制階段和批量生產階段的側重點不同,因此其加工工藝安排和使用的設備也就不同,試制階段,主要以利用已有的加工中心通用設備和標準刀具,新增復合角度的專用夾具完成加工,達到產品圖紙要求為主,生產效率及生產成本不是主要考慮的因素; 而批量生產階段主要考慮在保證加工精度的前提下,以提高生產效率,保證生產節拍,降低單件生產成本為主,因此,本文中對氣缸蓋電熱塞孔加工的批量生產階段重點分析論證,采用了組合機床與復合刀具的方式安排加工,應用最優化、最高效的加工氣缸蓋電熱塞孔工藝,達到了預期效果。為今后同類孔結構的加工積累了經驗,提供了借鑒依據。
投稿箱:
如果您有機床行業、企業相關新聞稿件發表,或進行資訊合作,歡迎聯系本網編輯部, 郵箱:skjcsc@vip.sina.com
如果您有機床行業、企業相關新聞稿件發表,或進行資訊合作,歡迎聯系本網編輯部, 郵箱:skjcsc@vip.sina.com