發動機缸體加工過程動態SPC 質量控制系統設計
2019-1-2 來源:合肥工業大學機械與汽車工程學院 作者:孫 迪
摘要:針對發動機缸體加工過程質量控制問題,首先分析了發動機缸體加工工藝,并對關鍵質量控制點進行了闡述;其次,在分析缸體機加工過程實時數據采集流程的基礎上,建立了一套動態SPC 控制系統(Dynamic SPC,D_SPC);然后,詳細闡述了D_SPC 的硬件架構和軟件架構,并介紹了D_SPC 質量控制系統的功能模塊。最后,以缸孔孔徑的測量為例,說明了該系統可以有效地解決缸體機加工過程的質量控制問題。
關鍵詞:發動機缸體加工;統計過程控制;質量控制系統;實時監控
0 引言
發動機缸體的機加工質量是發動機最終質量的重要保障,其質量的優劣,是衡量一個發動機裝配性能和運行可靠性的重要指標[1] 。在缸體制造過程中,產品制造質量管控能夠對產品的生產質量起到在線監測、把關、預防、改善的作用。統計過程控制(StatisticalProcess Control,SPC)則為產品的質量分析和控制提供了方法支持[2] 。通過SPC 控制圖可及時甄別出生產過程出現的異常趨勢,根據不同的判異規則,及時找出異常發生的具體原因并加以排除,保證產品不在有異常的環境下完成生產,從而保證產品質量。由此可見,要想提高發動機缸體加工過程質量,必須提升機加工過程的質量控制水平。
為此,國內外學者從不同角度對制造過程質量監控做了大量研究。綜合運用神經網絡、統計過程等理論與技術,姜興宇等[3] 利用一種動態工序質量控制模式用以解決網絡化制造環境下工序質量難以控制的問題。ALANEME K K 等[4] 從SPC 動態控制、模糊綜合評判和專家知識庫等方面綜述了質量管理,分析了制造過程中質量異常控制等方面的處理技術。翟敬梅等[5] 提出了一種基于質量統計控制和粗糙集理論的質量集成模型,并發展了一種工序質量診斷模型,用以研究生產參數在工序質量控制過程中的重要性。針對質量診斷過程中出現的不確定、模糊性問題,侯世旺等[6]提出了一種質量推理系統,利用模糊邏輯確定質量診斷過程中質量異常發生的程度。基于標準化樣本方差和霍特林模型,趙永滿等[7] 提出了一種聯合控制圖,用于監控質量二元過程中均值向量和協方差的變異。為了讓傳統的計算機輔助質量系統實現質量過程控制、隨業務需求改變而柔性重構的功能,李成等[8] 提出了一種基于工作流程模型的質量系統體系結構。劉春雷等[9] 針對傳統質量控制方法在解決小批量生產中的局限性問題,提出了一種工序控制系統,應用于制造過程的質量預防、診斷與分析改進。
上述研究為制造過程質量控制提供了方法和技術支撐。動態制造過程質量控制方法可以很好地解決產品制造過程的質量控制問題,提升產品的質量和生產過程穩定性。復雜產品的制造過程質量控制是質量控制的重點和難點,為此本文以發動機缸體機加工過程質量控制為例,運用動態SPC 質量控制系統來提升其制造過程質量。
1、缸體加工過程及參數分析
發動機缸體作為發動機的關鍵組成部件,其加工圖2 D_SPC 的數據庫模型過程由多道工序完成,每道工序具有繁多的質量控制特性需要進行分別控制。缸體在完成粗加工后,依次經過以下操作過程:①缸體產品出生證(唯一編碼)打刻,方便后期的質量數據采集、分析和追溯;②缸體清洗,然后進行缸體的油道試漏檢測,主要包括壓力測試、泄漏量測試等;③曲軸蓋螺栓擰緊,控制10 個曲軸蓋螺栓的力矩和轉角;④缸孔綜合測量,主要是對上游工序的綜合加工結果進行把關控制,主要包括曲軸孔直徑(每個孔取三個截面和兩個方向)、曲軸孔圓柱度、缸孔直徑(每個孔取三個截面和兩個方向)、缸孔圓柱度;⑤缸孔的水道試漏,主要包括壓力測試和泄漏量測試。
2、缸體加工過程D_SPC 系統架構
綜合考慮發動機缸體加工過程的關鍵質量特性,為更好地滿足其加工過程的質量控制要求,構建了D_SPC 系統架構。如圖1 所示,主要分為檢測層、數據采集層、服務層3 個部分。
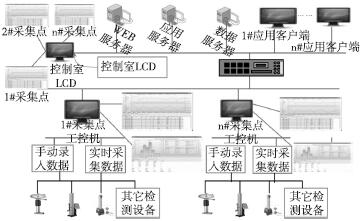
圖1 D_SPC 系統架構
D_SPC 系統通過標準化數據接口與設備、生產線、ERP 系統等集成在一起,是上層系統和底層設備間的中間系統。檢測層和數據采集層實時采集缸體機加工過程的關鍵質量數據,并根據設置的判異規則,實時繪制動態SPC 控制圖,并通過企業的統一信息服務平臺進行發布。在缸體的制造過程中采集的數據主要包括缸體質量特性數據、產品異常信息、糾正與改善信息、分析出的異常信息、檢測設備數據信息等。這些信息以手動或自動方式存入不同的數據庫中。自動采集的數據輸入至D_SPC 系統,自動生成各類控制圖,分析產品當前的制造過程是否處于穩定狀態;手動錄入的數據可以用于后期對生產過程的統計分析和追溯,為生產過程產品的質量改善提供支持。控制室LCD 用于顯示各個數據采集點的實時數據分析圖,并計算出上控制線、下控制線、CPK(工序能力指數)等。服務器主要由實時數據采集服務器、歷史數據服務器和WEB 服務器三部分組成,以此為D_SPC 系統的運行提供支撐。
3、缸體加工過程系統設計
3. 1 D-SPC 的數據庫模型
圖2 所示為D_SPC 系統的整體數據庫結構。主要包括產品_產品清單、工作站清單、質量規范清單、人員_人員基本信息表、人員_部門基本信息表、質量分析設置表、工作站_質量規范關聯表、產品_故障類型表、產品_故障類型清單、檔案_產品故障與故障原因關聯表、檔案_故障產品詳細信息表、權限_權限基本信息表、工作站_人員關聯表。上述數據庫模型闡述了各個表之間的對應關系,以及表中的主鍵和外鍵約束,為建立規范化的數據模型打下了基礎。
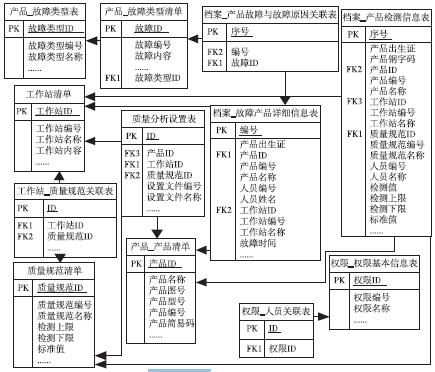
圖2 D_SPC 的數據庫模型
3. 2 D_SPC 的軟件架構
根據上述D_SPC 質量控制體系和數據庫模型,本文構建了D_SPC 的軟件架構。如圖3 所示,主要由底層數據采集、系統總體業務、系統總體功能、企業信息系統數據通信接口、數據處理中心和關鍵質量信息發布等六部分構成。
底層數據采集模塊主要是開發一套生產車間底層控制系統,從PLC、智能儀器儀表和機器設備進行自動數據采集,具備手動數據錄入功能。系統總體業務包含建立產品基本信息、定義工作站信息、配置產品對應檢測規范信息、系統權限管理、人員基本信息、系統數據采集客戶端定義、樣本規則定義、判異規則定義、故障原因分析、控制圖自定義設置等內容。系統總體功能主要是對產品信息、工作站信息、質量規范信息、權限信息、人員信息、采集數據信息、故障原因信息等進行管理。
企業信息系統數據通信接口主要是通過Webservice、Files、Socket、Message queue 等接口方式, 將MES、ERP、PDM 等系統的關鍵數據接收至D_SPC 系統,對D_SPC 的使用提供支持,并可以將采集的質量數據、分析結果數據實時上傳至上層應用系統。數據處理中心為各個功能模塊數據處理提供支持,動態采集的生產過程。實時數據被存入實時數據庫,用于生產過程的實時狀態監控和控制。歷史數據被存入歷史數據庫,用于對生產過程信息的追溯和統計分析。需要進行網頁發布的數據被存入Web 數據庫,用于信息的網頁發布和多部門間的共享。關鍵質量信息發布主要是將制造過程中的質量數據和統計分析數據實時向工人或質量管理人員發送,包括各個工序的生產能力指數、返修率、合格率等。
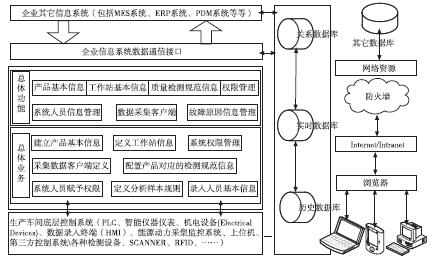
圖3 D_SPC 的軟件模型
4、應用實例
綜合上述分析, 本文基于. NET 平臺中, 采用SQL2008 數據庫,采用C#語言開發了D_SPC 系統的原型系統,并將該原型系統應用于發動機缸體制造過程中。圖4 所示為關鍵工序SPC 實時監控界面,主要含異常處理按鈕、標題區、功能按鈕區、原始數據區和控制圖區。
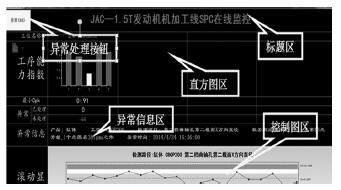
圖4 D_SPC 系統在缸體制造過程中的實例
在該監控畫面上,可以實時顯示關鍵質量控制點的工序能力指數,異常信息,動態SPC 控制圖等信息,管理人員通過辦公室的LED 大屏幕就能實時監控生產現場的生產狀況。
5、結論
本文構建了一種面向制造過程的動態SPC 質量控制體系,詳細闡述了D_SPC 的體系架構、數據庫模型、軟件架構。該系統能夠根據實時制造工況信息對當前在制品的質量進行動態分析,保障了產品的整體制造精度和穩定性。動態對在制品的質量狀況分析能及時甄別出制造過程中的異常情況,及時給出預警提示,防止出現批量不合格品,為生產過程的主動質量控制提供了思路和方法。本文構建的系統可推廣應用到缸蓋加工過程、發動機裝配過程、變速箱裝配過程等機械產品的制造過程中。
投稿箱:
如果您有機床行業、企業相關新聞稿件發表,或進行資訊合作,歡迎聯系本網編輯部, 郵箱:skjcsc@vip.sina.com
如果您有機床行業、企業相關新聞稿件發表,或進行資訊合作,歡迎聯系本網編輯部, 郵箱:skjcsc@vip.sina.com
更多相關信息