普通組合機床上深孔加工技術的研究
2018-12-14 來源:廣西玉柴機器股份有限公司 作者:馮基
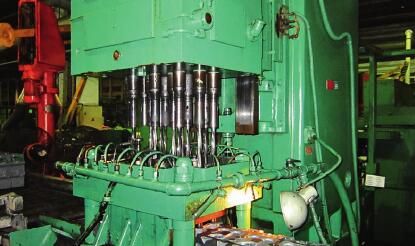
本文提出了基于普通組合機床上加工深孔(階梯深孔)一系列加工技術,解決了加工柴油機發動機氣缸蓋過釘孔、導管底孔、噴油器安裝孔等深孔(階梯深孔)位置度、孔徑難保證的難題,提高了產品的加工質量,降低了生產成本。
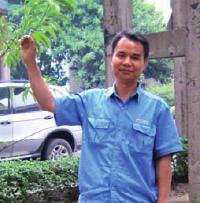
作者:馮基 廣西玉柴機器股份有限公司三發廠技術科主任工程師,從事機加工現場工藝技術的工作已經有20多年,對解決機加工工藝技術疑難問題有著豐富的工作經驗和較深的造詣。
普通組合機床上深孔(階梯深孔)的加工是公認的難題,其位置度(特別是出口位置度)以及孔徑精度很難保證。目前國內外對深孔加工一般采用槍鉆(或槍鉸),但是槍鉆(或槍鉸)對于小孔距的深孔(階梯深孔)的孔系由于其結構的限制不能一次加工完成,需要采用多工位加工,因此,降低了生產效率,增加了加工成本。同時其對設備精度要求較高,普通組合機床不能勝任,因此投入大,不利于廣泛應用。因此,必須突破普通組合機床上傳統加工技術的局限性,發展出全新的深孔(階梯深孔)加工技術。
前、后同時導向深孔加工技術柴油發動機氣缸蓋過釘孔深9 6 m m ,孔徑φ 1 5 m m ,長徑6.4,屬深孔,采用的加工技術為第一道工序鉆φ14mm孔,第二道工序擴φ15mm孔。普通組合機床上傳統的擴孔技術采用如圖1所示的后導向方式,其目的是為了修正第一道鉆孔工序的位置,但是由于擴孔刀在開始切削時受到第一道鉆孔工序位置偏差大的影響而造成加工余量不均勻,受到不對稱的徑向力擠向余量小的方向,因此刀具開始切削就有傾斜的趨勢。隨著加工孔的深度增加,擴孔刀的懸伸也隨之增加,其剛性變得來越差,并且開始出現變形彎曲,越來越傾斜。當加工到達出口時其位置偏移達到最大。可見,傳統的后導向的擴孔技術由于無法解決刀具的剛性問題,因此對過釘孔位置的修正是有限的。
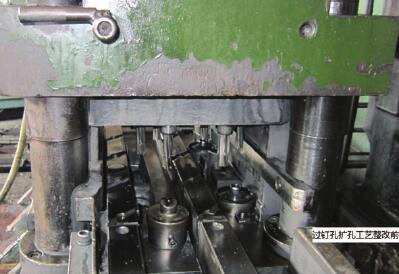
圖1
因此,要解決過釘孔出口位置偏的加工難題,必須解決擴孔刀剛性差的問題。圖2是對擴孔專機的夾具、刀具進行改進,夾具上增加了前導向裝置(由前導向模板、前導向套等組成),擴孔刀增加了前導向。加工時刀具前后導向分別進入前后導向套定位,然后開始切削加工。由于在切削加工過程中刀具始終有前后導向套的支撐定位,因此其剛性得到了顯著加強,從而有效地克服了刀具的變形彎曲,保證了過釘孔入口、出口的位置度。為了解決排屑及掉刀問題,將擴孔刀設計成左旋右切(見圖3),這樣刀具自然形成的負前角可以使切屑順利地向前排出,同時左旋的螺旋槽可以使刀具在回轉時受到一個沿軸向向后的推力,防止刀具退回時被從接桿拉下來卡在工件里。
由于過釘孔是深孔,刀具的后導向部分必須得進入已加工孔內,且其長度隨著加工孔深度的增加而增加,故后導向部分與孔壁的摩擦力越來越大,嚴重時刀具被“抱死”,甚至被扭斷,同時電動機因為過載而跳閘。因此,為了減少刀具后導向部分與已加工孔的摩擦力,刀具后導向部分的直徑必須比切削部分的直徑小,優選小0.02~0.03mm,不能小太多,否則會影響導向精度。同時刀具切削部分的材料要選擇耐磨性較好的合金,防止刀具磨損過多后出現“抱死”現象。經過使用驗證, 合金YS8或YS10使用效果很好,新刀加工件數多達9 000件以上,而且可以反復刃磨利用。為了解決定位銷的定位、導向、排屑的問題,如圖3所示,在定位銷上設置了排屑孔、導向孔及讓刀孔。其工作原理如下:前后導向刀具的前導向穿過工件的待加工孔,并進入定位銷中心的導向孔,同時刀具的后導向也進入夾具后導向模板的導向套,接著刀具開始對工件的待加工孔進行切削,產生的切屑的一部分通過刀具前導向的螺旋槽排出,一部分通過定位銷法蘭的3個排屑斜孔排出。當刀具切削刃部分進入定位銷避開刀具的讓刀孔時,整個加工過程完成。
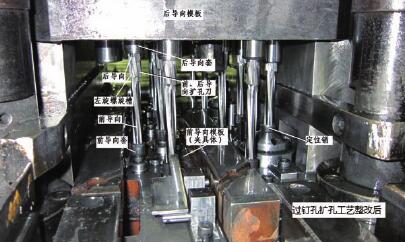
圖2
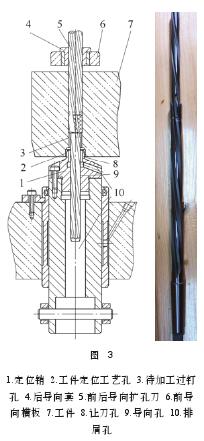
圖3
前導向深孔加工技術柴 油 機 氣 缸 蓋 導 管 底 孔φ15.2mm及氣門座孔組成階梯深孔(其中導管底孔是深孔),為了修正上道工序加工誤差,普通組合機床上其半精加工如圖4所示采用傳統的鏜孔加工技術。但由于導管底孔鏜刀桿直徑小,懸伸長(小鏜刀到氣門座孔鏜刀距離約86mm),剛性不足,加工時受力時擺動大,因此加工的導管底孔孔徑有錐度,直線度、位置度、垂直度等變動大。特別是與氣門座孔不同軸,經常因為這些問題影響精加工工序精鉸導管底孔的精度,如鉸不出,位置度、垂直度、特別是同軸度差等。
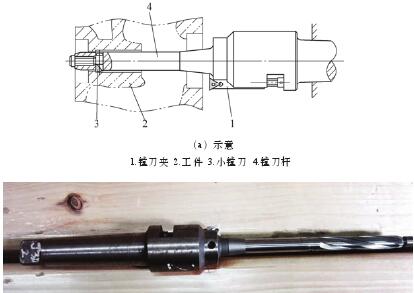
圖4
為了有效解決上述問題,必須將φ15.2mm導管底孔的鏜刀桿的剛性加強,因此,如圖5所示,改進了模板及鏜刀桿。為了降低鏜刀桿的制造難度、制造費用,將其設計成組合裝配式,即將其設計成加工細長導管底孔部分的前導向鏜刀桿及加工較大氣門座孔部分的氣門座孔鏜刀桿,然后將前導向鏜刀桿安裝到氣門座孔鏜刀桿上,兩者采用H6/h5配合聯接,并用夾緊螺釘壓緊前導向鏜刀桿的斜面。一方面可以傳遞轉矩,一方面產生的軸向分力可以使它們的端面緊密貼合,保證裝配后它們的同軸度及剛性;為了提高前導向鏜刀桿抗疲勞強度,將安裝小鏜刀的安裝槽設計成圓形;為了解決小鏜刀的緊固和定位問題,采用了通過螺釘壓分段頂桿去壓小鏜刀的扁位實現,同時也解決了細長螺釘加工困難的問題;為了減少前導向鏜刀桿與導向套的摩擦力,在前導向鏜刀桿上加工出四條15°螺旋槽,形成四條寬度為4~5mm圓柱導向帶。進行加工時,前導向鏜刀桿導向部分部首先進入導向套,然后開始加工細長導管底孔,加工完細長導管底孔后,接著加工較大氣門座孔。由于鏜刀在整個加工過程中(包括細長導管底孔、較大的氣門座孔加工)前導向鏜刀桿都有前導向套的定位導向,因此鏜刀桿特別是細長導管底孔前導向鏜刀桿的剛性得到顯著增強,從而根本上解決了加工細長導管底孔因鏜刀桿直徑小、懸伸長剛性不足所引起的擺動,進而解決了加工細長導管底孔孔徑有錐度,直線度、位置度、垂直度變動大,及其與較大氣門座孔不同軸等加工難題。
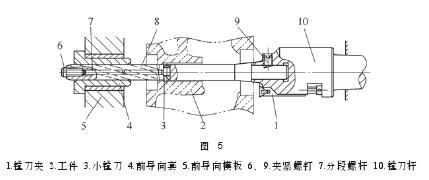
圖5
先后導向,然后前、后導向深孔加工技術 如 圖 6 所 示 , 柴 油 機 氣 缸 φ25mm×φ12mm×φ9.3mm噴油器孔是階梯深孔(其中φ12mm、φ9.3mm是深孔),上部φ25mm
孔與下部φ25mm之間是空腔,其軸線與氣缸蓋底面成67°夾角,普通組合機床上傳統的精加工技術采用如圖7所示的后導式復合精鉸。由于是階梯斜孔,加工時極易偏移,φ25mm孔中間的空腔降低了刀具在φ25mm孔內的自導作用,刀具φ9.3mm部分懸伸長(切削刃端面到導向套端面約90 mm),剛性不足、擺動大,因此φ9.3mm噴油器孔出口軸線與底面交點到定位孔的尺寸(83±0.1)mm很難保證,長期以來該尺寸都無法得到了有效控制,而該尺寸卻是噴油器孔的關鍵尺寸,其加工的好壞直接影響噴油器安裝的配合精度及位置精度,從而影響整機的性能和可靠性。
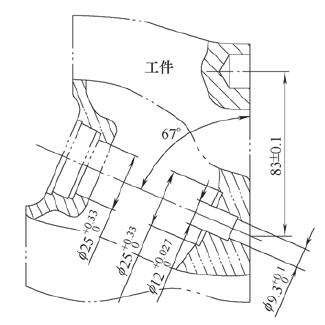
圖6
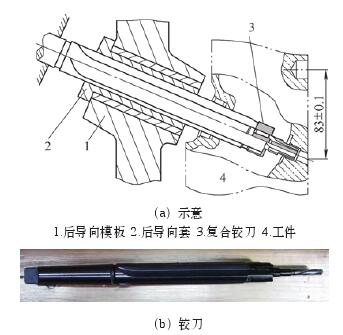
圖7
針對上述階梯噴油器孔精加工技術的缺陷,開發出了一種全新新的精加工技術,具體為,本技術采用前后導向型復合鉸刀分兩步進行精加工,加工上部φ25mm孔(見圖6)時,如圖8所示,由于上部φ 25m m孔靠近后導向套,前后導向型復合鉸刀的導向精度高、剛性好,首先保證上部φ25孔的位置精度;加工下部φ25mm、φ12mm、φ9.3mm孔時,前后導型復合鉸刀的前導向段已經伸入前導向套,此時,前后導向型復合鉸刀不僅有后導向套的定位,而且有靠近下部孔的前導向套定位,刀具的剛性得到了加強,提高了定位精度,因此,保證了下部孔的位置精度。
結語
組合機床上深孔加工技術的開發應用成果適用于機加工行業深孔(階梯深孔)的加工,解決深孔(階梯深孔)加工位置度、孔徑等難保證的難題,提高了產品的加工質量,降低了生產成本,提升了產品的市場競爭力,產生了巨大的直接、間接的經濟效益、社會效益,在機加工行業有著廣泛的推廣價值。
投稿箱:
如果您有機床行業、企業相關新聞稿件發表,或進行資訊合作,歡迎聯系本網編輯部, 郵箱:skjcsc@vip.sina.com
如果您有機床行業、企業相關新聞稿件發表,或進行資訊合作,歡迎聯系本網編輯部, 郵箱:skjcsc@vip.sina.com
更多相關信息