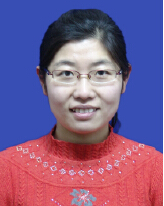
作者之一 :蔣南云
0 引言
隨著人性化理念日益受到關注,企業在追求經濟效益的同時更加關注人與機器之間的協調關系,使人在系統中安全、舒適、高效、健康、經濟地發揮作用,以適應現代化生產。以往文獻[1-3]多從人機尺寸關系、工具改進等單一方面進行人機系統設計。本文綜合運用工業工程的人機工程學[4-5]、現場管理[6]等理論設計實驗內容,以機加工車間常見的XB6140 型臥式銑床為實驗對象,分別從工作臺椅尺寸、輔助工具改進、時間以及操作分析等多個方面進行人機系統優化,使人機系統更加符合動作經濟原則,進而幫助企業提高生產效率。
1 、臥式銑床人機系統存在問題分析
選取機加工車間臥式銑床人機系統為實驗對象,其中“人”是銑床操作員,主要操作銑床完成加工工件表面工序,“機”是XB6140-半自動臥式單頭專用銑床,加工工件表面粗糙度以及溝槽等,還包括一些輔助工具,以便操作銑床。加工工序包括厚度切削和輪齒加工兩步驟,具體如圖1 所示。
圖1 加工工序圖
1. 1 現有人機系統尺寸分析
1. 1. 1 工作椅與工作臺
通過實驗測量,現有人機系統中工作座椅表面高度距離地面690 mm,加工銑床的工作臺面高度距離地面為1 120 mm; 操作員小腿加足高經測量尺寸為388mm,計算可知操作員坐在工作座椅上足底距離地面的高度為690 - 388 = 302 mm,說明當操作員坐在該座椅上工作時,腿部自由下垂,腳部懸空; 操作員坐姿肘高經測量為284 mm,肘關節距離地面為284 + 690 = 974mm,肘關節比機床工作臺低1 120 - 974 = 146 mm,說明操作員工作時須長期抬高肘部工作,給肩關節及肘關節帶來負擔。人機系統詳細尺寸如圖2 所示,工作
臺與操作員接觸面處無腿部活動空間,操作員工作時腿無處擺放,需向前探身工作,易使操作員腰背部肌肉和韌帶長期超負荷使用而引起勞損。
圖2 人機系統尺寸分析( mm)
1. 1. 2 輔助工具
( 1) 手工工具。在加工過程中,需使用工具鉗夾取待加工件。現有工具鉗如圖3 所示,其形狀和普通的剪刀相似。從圖中的箭頭方向和腕部作用點可知,施力方向與作用點不在同一水平線上,長期保持這個姿勢,會造成靜肌負荷,從而引起腕道綜合征,對人體造成傷害。
圖3 工作鉗示意圖
( 2) 操作裝置。在加工過程中,每加工完一個工件需用腳踩地面上的踏板鈕,以便松開夾具取下已加工工件。此時操作員坐在座椅上,腳距離地面302mm,無法完成操作,只能從座椅上下來或半側坐才能觸碰到地面踏板完成操作,既浪費時間也易造成人體關節損傷,急需優化調整。
1. 2 現有人機系統效率分析
由加工工序圖( 見圖1) 可知,待加工件需進行兩道主要工序才能夠完成銑床加工: 厚度切削和輪齒加工,由一名操作員完成。首先操作者利用銑床①進行工件待加工面的厚度切削,不斷重復進行,工作時間為上午3. 5 h,共加工750 個零件; 然后再利用銑床②進行工件的輪齒加工,工作時間為下午4 h,共加工740個零件; 操作員工作7. 5 h。銑床①厚度切削加工時,銑床②閑置,銑床①利用率為: 3. 5 ÷ 7. 5 × 100% =46. 7%; 同樣銑床②輪齒加工時,銑床①閑置,銑床②利用率為: 4 ÷ 7. 5 × 100% = 53. 3%。即便是在銑床①、②的工作時段內,由于裝夾工件、取下工件、清理工作臺鋁屑等也占用時間,銑床仍存在空轉時間。人機系統中機床利用率低,資源浪費大,操作人員缺乏動作標準,隨意性大,急需制定標準作業時間,協調人機操作,提高人機效率。
2 、車間人機系統優化設計
2. 1 實驗一: 人機系統尺寸優化
2. 1. 1 工作椅與工作臺改進
根據高度推薦值[7-9]規范,輕型裝配坐姿作業面高度建議為720 mm,高于肘部110 mm 左右,而實驗中人機系統作業面高度為1 120 mm,因此需將座椅加高至1 120 - 284 - 110 = 726 mm,取整數為720 mm。
2. 1. 2 輔助工具改進
( 1) 手工工具改進。使用工作鉗夾取待加工件時,需避免人體腕部方位與加工方向不協調,應保持手腕順直狀態,因此可設計工作鉗握把彎曲。不僅可以加大施力、減少腕部損傷,而且在機床加工工件時還可用工作鉗觸碰機床暫停按鈕,減少身體前傾或手臂前伸,縮短動作移動時間。改進后工作鉗如圖4 所示。
圖4 改進后工作鉗示意圖
( 2) 操作裝置改進。操作員控制卡盤松開工件需腳踩腳踏板。坐姿操作時,工作椅座面與工作椅支腳距離一般為450 mm[9],那么座椅支腳離地面高度應設計為: 720 - 450 = 270 mm; 此時將操作者腿部正前方的機床向里凹進距離地面300 mm,寬200 mm,高500mm 立體空間,將腳踏板放置于該空間內,如圖5 所示。這樣操作者坐在座椅上踩腳踏板時,可以直接從支腳移至腳踏板上或者直接將腳放在凹進的立體空間內,不僅減少操作者上下座椅動作,節約操作時間,而且保證腿部足夠的活動空間,避免操作者上身長期前
傾帶來的背部損傷。
圖5 人機系統尺寸改進( mm)
2. 2 實驗二: 人機系統時間研究
由于人機系統尺寸和加工工具的改進,縮短了操作人員加工時動作移動距離,降低了工作疲勞度,因此利用模特排時法[10]重新對厚度切削操作進行動作分解以制定標準作業時間[11]: ① 拿取待加工工件至卡盤附近M3( 小臂動作) ; ② 利用工作鉗夾取物件M1( 手指動作) ; ③ 打開機床開關M1( 手指動作) ; ④ 開始加工伸向開關處按下運行M5( 大臂動作) ; ⑤ 刀具自動加工10 s( 無需人參與) ; ⑥ 完成后按下暫停M5( 大臂動作) ; ⑦ 松開卡盤時需完成腳踏板操作F3( 下肢動作) ; ⑧ 取下已經完成輪齒加工工序的部件放入收納盒M3( 小臂動作) ; ⑨ 往臨時工件收納盒中放入已加工部件P2( 終結動作) 。
計算可得,厚度切削人員作業時間= M3 + M1 +M1 + M5 + M5 + F3 + M3 + P2 = 23 × 0. 129 = 2. 967 s,加上刀具自動加工時間10 s,可得厚度切削標準作業時間為12. 967 s( ≈13 s) 。輪齒加工與切削加工的人員操作動作完全一致,只是輪齒加工機床的刀具自動加工時間為12 s,因此輪齒加工標準作業時間為2. 967 s + 12 s = 14. 967 s( ≈15 s) 。
2. 3 實驗三: 人機系統操作分析
由以上標準作業分析可知,在厚度切削機床刀具自動加工的10 s 和輪齒加工機床刀具自動加工的12 s時間中,操作人員處于等待空閑狀態,不需完成任何操作,存在浪費。可以充分利用這段時間,讓操作人員移動至另一機床處進行操作,完成另一機床的裝夾工件、卸下工件等操作,使兩臺機床同時交替加工,提高操作人員工作效率。
經模特排時法可知,由操作人員在兩機床之間移動動作為6 × W5,需耗時30MOD × 0. 129 s /MOD =3. 87 s( ≈4 s) ,往返需8 s,由上節分析可得在機床自動加工前進行的裝夾加工件等準備工作,耗時10MOD× 0. 129 s /MOD = 1. 29 s,卸下已加工工件耗時13MOD× 0. 129 s /MOD =1. 677 s,三者時間相加為10. 967 s,小于銑床①、②的刀具自動加工時間最大值12 s,操作人員時間足夠,因此兩機同時交替工作完全可行。
實驗操作時,同時打開銑床①和銑床②; 先在銑床①上裝夾工件; 待銑床①自動進行厚度切削時,操作員可移動至銑床②進行裝夾工件,在銑床②自動進行輪齒加工后移動回銑床①卸下已加工件并裝夾新工作,循環往復。兩機交替操作的時間間隔( 相當于節拍)取兩機加工的最大值,即輪齒加工時間15 s。因此原先加工一個工件所需要完成的兩道工序時間累計為28 s,現改為兩機交替工作,完成同樣工序只需15 s。
3 、人機系統優化實驗結果
經人機系統尺寸改進及工具調整后,肘部距離工作臺距離由146 mm 縮短為116 mm; 踏板鈕距離腳的距離由332 mm 縮短為32 mm。操作人員加工工件時,無需上下座椅踩踏控制卡盤的踏鈕,每加工一個工件可減少一次不必要的站立動作S30 = 30MOD = 30 × 0. 129 = 3. 87 s制定標準作業時間后,厚度切削標準時間是13 s,輪齒加工標準時間是15 s,利用機床自動加工時間進行兩機聯合工作,可在15 s 內同時完成厚度切削及輪齒加工兩道工序,7. 5 h 內可加工工件數為1 800 個,理論日產能比優化前的740 個提高了143. 24%。
4 、結語
人機系統優化是一個循序漸進的過程 ]。本文綜合應用工業工程多種方法,設計實驗步驟,根據實際加工過程改進人機系統尺寸、制定標準作業時間、進行人機操作分析對人機系統優化設計,大大提高了XB6140-半自動臥式機床的利用率,為人機系統設計提供了一種示范和思路。本文的實驗結果已在航海機械集團機加工車間得到應用,生產效率大幅提高。在現有的人機系統中發現問題,充分考慮人的因素,將人與機相結合,優化設計出協調的人機系統,既能為企業帶來巨大的經濟效益,也是現代化生產的必然要求。
如果您有機床行業、企業相關新聞稿件發表,或進行資訊合作,歡迎聯系本網編輯部, 郵箱:skjcsc@vip.sina.com