WMEM|航空發動機關鍵制造技術現狀及趨勢
2019-5-16 來源:轉載 作者:-
航空發動機關鍵制造技術是未來我國航空發動機工業發展的一個重要指標。傳統的制造工藝和生產模式已經無法滿足航空發動機制造在高精度、高質量、高效率、高可靠性等方面的需求,隨之而來的三軸、四軸、五軸數字化加工是未來中國航空發動機制造業發展的重要基礎。
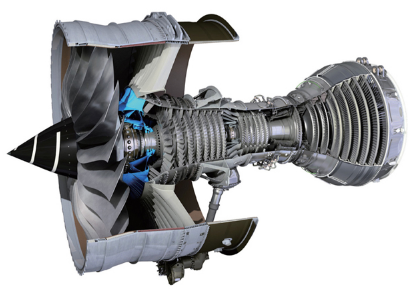
基于航空發動機高復雜性、高可靠性等要求,目前航空發動機制造能力仍然按照“制造→試驗→修正制造→再試驗…”的模式,這就注定了航空發動機研制本身不但是個高科技事業,還是一個高投入的事業。我國在航空發動機研制試驗初期走了不少彎路,幾經坎坷,“三落四起”,目前正處于“第四起”的階段,對我們既是機遇又是挑戰。世界上只有少數的幾個國家具備航空發動機制造技術,它代表了一個國家的科技水平、工業水平和綜合國力。
通過幾代航發人的共同努力,我們實現了由噴氣發動機向渦扇發動機的歷史性跨越,由小推力到中等推力向大推力轉變,由二代半向三代機、四代機轉變。目前正在開展四代機及大推力、大涵道比發動機的研發工作,發展的需求客觀上要求我們用更先進的制造技術引領航空發動機技術的提升。
主要關鍵制造技術有:整體葉盤、葉環制造技術;靜子、轉子葉片制造技術;機匣制造技術;寬弦風扇葉片制造技術;金屬基、陶瓷基及碳/碳復合材料構件等制造技術。
航空發動機需在高空、高速、高溫、高壓、高轉速和交變負荷的惡劣條件下長期、重復、可靠使用,與其他運載系統的動力相比,航空發動機是世界上工作條件最苛刻,結構最復雜的物理系統。正如美國在其國家航空發動機關鍵制造技術推進計劃中寫到的:“這是一個技術精深得使新手難以進入的領域,它需要國家充分保護并利用該領域的成果,需要長期數據和經驗的積累以及國家大量的投資。”
為滿足我國航空發動機更新換代需求,重點需建立、健全航空發動機發展型譜。這就使得近年來發動機機種多,研制周期短,技術難度大。為了能更好地完成各個型號研制的預定目標,科學高效地開展技術創新和工藝突破,提高技術成熟度,成為當務之急。
1.梳理流程
在關鍵制造技術領域,以往的技術工作一般是圍繞型號任務開展。型號任務下達后,設計部門下達技術圖紙和標準,我們圍繞圖樣和標準去開展工藝準備。在消化圖樣和標準的過程中,不斷發現問題,發現新的工藝難點和新技術,再針對新工藝、新材料進行立項攻關。
由于之前沒有技術儲備,往往導致研制周期過長,型號節點一拖再拖。針對相關問題,我們需要重新梳理流程,改變以往下達圖樣→工藝準備→立項攻關→工藝定型的模式,使相關工作與設計過程(MBD)并行實施。即在設計階段(MBD)開展工藝預先研究→三維圖下發→工藝準備→工藝定型。針對設計提出的要求開展新材料、新工藝的預先研究,縮短產品研發時間,提高研發效率。這樣就可以在設計階段即開始新工藝和新技術的攻關工作,為型號研制做好技術儲備。當研制任務正式下達時,可以立即進入生產階段,減少大量的攻關時間,大大提高研發效率。
2.知識管理
隨著科研型號的不斷增多,新材料、新工藝技術應用也越來越多。但往往隨著優秀專家和技術人才的退休離崗,在新材料、新工藝應用過程中產生的寶貴經驗和知識財富也不斷流失。同時,涌入的大量新生力量,缺少相關經驗知識的支持。如此,人才隊伍建設能力不能滿足繁重的型號任務要求。
因此,建立具有專業特色的知識工程平臺,全面解決知識積累、共享瓶頸;打造型號研制創新平臺,提高研發效率,提升工廠綜合創新能力,成為當務之急。將知識工程與工廠型號研發實際結合起來,針對型號產品研發過程中的工裝設計、材料、制造過程模擬、工藝改進、產品檢測等進行知識積累、存儲、共享、應用和創新,建設全面的知識工程支撐平臺和計算機輔助創新工具,實現知識的快速積累、深度挖掘、充分共享和高效應用,全面系統地提高型號研制的科研水平,以利經驗傳承和創新驅動,最終形成基于知識工程的產品創新、研發和生產體系。
3.薄壁難加工材料制造
圖1 為某發動機機匣構件,材料為奧氏體不銹鋼難加工材料,牌號0Cr17Ni4Cu4Nb,最小壁厚為1.1mm,外弧面要求輪廓度≯0.08mm,受變形因素影響,輪廓度超差,嚴重制約機匣組件的裝配質量,造成安裝應力,影響到機匣組合件裝配及發動機的效能。改善和控制薄壁環塊變形不單是生產合格零件的需要,更是提升航空制造能力,提高航空發動機性能的先決條件。
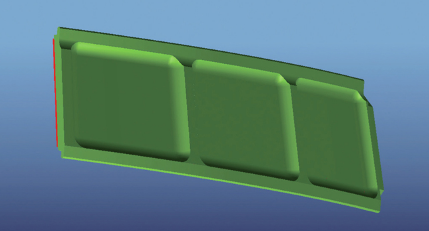
圖1 某發動機機匣構件模型
可通過以下工序滿足構件結構形狀要求:
(1)調整加工余量。
(2)采用數控機床加工,調整、固化加工。
(3)改進零件裝夾方式。
(4)采取對稱銑槽加工。
(5)在銑加工型槽之后增加穩定處理工序,改善二次加工應力。
4.先進的復合材料成型制造技術
樹脂傳遞模塑,即將干態的復合材料經過預定型,放入特定的模具中夾緊,從設置的適當注膠口在一定溫度、壓力下將配好的樹脂注入模具中,使之與增強材料一起固化成型的工藝方法。這是樹脂基復合材料應用較廣的工藝技術,起源于20世紀50年代的冷模澆注,其發展動力是為了使飛機雷達罩的成型技術發展起來。該工藝具有成本低、尺寸精度高的特點,對技術要求高,特別是對原材料和模具要求較高。
由于當時未能解決排除氣泡難、纖維浸潤性差、樹脂流動出現死角等制造技術問題,限制了廣泛應用。直至20世紀90年代,隨著對樹脂傳遞模塑工藝及理論的研究,設備、樹脂和模具技術日臻完善,該工藝發展成了復合材料行業低成本成形工藝之一。與傳統的模壓工藝相比,可提高纖維體含量,有助于樹脂對纖維的浸漬,降低孔隙率,提高產品內在質量。
其工藝特點是:
(1)分為增強材料預成型體成型和樹脂注射固化兩個步驟,具有高度靈活性和組合性。
(2)采用與制品相近的增強材料預成型技術,纖維樹脂浸潤一經完成即固化,可用低粘度快速固化的樹脂,并可對模具進行加熱而進一步提高生產效率及產品質量。
(3)閉模注入樹脂的方式可極大減少樹脂有害成分對人體及環境的毒害。
(4)該技術采取低壓(注射壓力≯4kg/cm2)注射技術,適宜大尺寸、外形復雜,表面粗糙度低的制件。
(5)模具可根據生產規模要求選擇不同的材料,從而降低制造成本。樹脂傳遞模塑隨在國內有許多單位在研制,但一直應用于等厚度、等致密度的產品中去,其膠液的流動狀態和流速易保持一致,產品穩定性好。但對于各截面纖維厚度、致密度、密度變化的諸如復合材料葉片來說,復雜的內部結構應用樹脂傳遞模塑技術會造成膠液流動狀態和速率不一致,從而導致其生產工藝更為復雜,工藝難度增大。其關鍵制造技術:預成型體制造技術。
預成型體制造技術即預定型是樹脂傳遞模塑前工序,其好壞影響樹脂傳遞模塑注射效果。大致可分為五種類型:手工鋪層、紡織法、針織法、熱成型原絲氈法和預成型定向氈法。根據產品使用要求,可使用不同的預制體。紡織體做成的預制體不存在層與層之間的界面問題,力學性能和熱學性能優良。該預制體要求具有疏松的組織結構,以便液態成型時液態樹脂能夠順利地浸潤和浸透結構預制體。要使干態復合材料結構預制體具有基本的自支撐性和形狀保持能力,利于預制體反復的鋪放和定位要求,還要有反復變形的性質,制件見圖2。

圖2 某復合材料制件
5.先進的五軸行寬數控成型制造技術
航空發動機靜子葉片為復雜異型面。起初,考慮加工變形影響,通過多次調整粗、半精、精加工方案,增加工藝過程中校形、人工時效等工序,試加工效果有所改善,但仍不能滿足設計要求。后通過五軸拋銑數控加工實現對其行寬最大化加工,優化加工路線,實現免拋光加工。
6.結語
航空發動機關鍵制造技術的應用,減少了人工干預、人為出錯的概率,克服了技術瓶頸。同時,為我國航空發動機發展提供了堅實的技術保障,實現了制造流程的規范化、自動化,提高了生產效率及產品質量,勢必對我國未來航空發動機產業的發展起到推動作用。
來源: 世界制造技術與裝備市場
投稿箱:
如果您有機床行業、企業相關新聞稿件發表,或進行資訊合作,歡迎聯系本網編輯部, 郵箱:skjcsc@vip.sina.com
如果您有機床行業、企業相關新聞稿件發表,或進行資訊合作,歡迎聯系本網編輯部, 郵箱:skjcsc@vip.sina.com